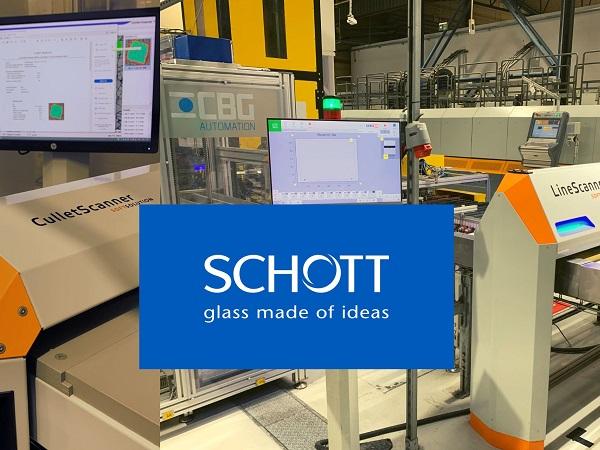
Date: 21 July 2022
Markus Stefan, International Sales Manager at Softsolution talked to Stepan Chmelar, Quality Manager at SCHOTT Flat Glass CR about the beginning of their successful collaboration.
When exactly did the collaboration start and how did you assess the products?
The cooperation with SOFTSOLUTION started in 2018 with the installation of the CulletScanner as the main tool for the inspection of glass fragmentation grade at the end of tempering furnace at Home Appliance.
CulletScanner was the first device in Schott AG using Softsolution linear scanning technology. To evaluate its capability multiple tests have been carried out before its introduction. It should be mentioned here that CulletScanner is located in a harsh industrial environment in the vicinity of grinding and tempering line, mostly operated in 3 shift mode. Therefore its reliability has been tracked carefully for more than 1 year.
Why did you decide that you would implement more Softsolution products?
As CulletScanner fully confirmed its capability and operational reliability under conditions of the Schott Flat Glass production line, we have started a discussion about utilizing this technology also in the area of visual defect detection.
Due to dimensional restrictions in our line together with the fact, that we have realized the benefit of real scanning technology, camera systems were not taken into consideration. So there started the second round of cooperation with SOFTSOLUTION. It was really challenging to define all needed project inputs like the definition of defects, scanner sensitivity and technical solution of the installation followed, of course, by multiple testing on real Schott samples in Waidhofen.
What specific method of quality assurance does SCHOTT FLAT GLASS CR perform with the LineScanner?
We have finally decided to install the LineScanner in combination with an automatic buffer at our automatic grinding line producing mainly oven front door glasses for home appliances. The LineScanner system is designed to reveal glass material defects, grinding and drilling defects, and scratches of all kinds.
Which procedure do you follow with NOK (defective) lites?
LineScanner is currently working with an automatic buffer system from local company CBG Automation s.r.o. for more than 6 months and its benefits are obvious. The NOK evaluated parts from LineScanner are now automatically rejected from a subsequent production process and stored in the buffer standing next to the production line. The operator can check later by himself on the display the exact location and nature of the defect on each part. But it is not about sorting OK and NOK parts only. Now we also have a clear connection between particular defects and previous processes which may cause them. The LineScanner is a reliable and important data source for our continuous improvement.
Will there be any new exciting projects with further automation possibilities?
Looking to the future we see further potential for LineScanner in the area of Food Display products. Together with our new project „Food Island“ which consists of the installation of a new production line dedicated for Food Display products we are planning to launch a study on LineScanner utilization within this line.
SCHOTT Flat Glass CR
SCHOTT Flat Glass CR belongs to the Business Unit Flat Glass of SCHOTT AG which is a worldwide supplier of glass components for home appliance manufacturers and insulation door solutions for commercial cooling and refrigeration. SCHOTT Flat Glass CR consists of 2 divisions Home Appliance and Food Display.
SOFTSOLUTION warmly thanks Stephan Chmelar from SCHOTT Flat Glass CR for the interview and for the opportunity to publish this information. Markus Stefan is looking forward to further cooperation and new exciting projects.
Mr. Markus Stefan:
"We warmly thank Stephan Chmelar from SCHOTT Flat Glass CR for the interview and for the opportunity to publish this information. We are looking forward to further cooperation and new exciting projects."


Add new comment