
Date: 4 December 2023
The production of Insulating Glass Units (IGUs) involves a careful quality control process to ensure these units meet the industry standards of performance and energy efficiency. One crucial aspect of glass quality control process is the measurement of insulating gas concentration inside the IGU. This article explores the various stages of the quality control process and emphasizes the crucial role of insulating gas concentration measurement which completes the quality inspection.
READ HOW SKAALA UTILIZED LASER PORTABLE IN THEIR PRODUCTION
Material Inspection and Selection
Before the assembly process begins, it’s essential to inspect and select high-quality materials. This includes ensuring the glass panes are defect-free, the spacer material is thermally efficient or suitable for its purpose, and the desiccant used effectively manages moisture within the IGU. However, sometimes you do not have use desiccant if the structure is solid. High-quality materials form the foundation for a reliable and long-lasting insulating glass unit.
Spacer Assembly and Sealing
The spacer assembly is a critical component influencing the overall thermal performance of the IGU. During this stage, precision in spacer placement, adequate desiccant distribution, and meticulous sealing are essential. Any deviations at this point can affect the insulating gas concentration within the unit, making it imperative to address potential issues during quality control checks.
Gas Filling Process
The controlled introduction of insulating gases such as argon or krypton into the sealed airspace significantly contributes to the thermal insulation properties of the IGU. An insulating gas unit without insulating gas can have up to 30% lower U-value than with gas filling over 85-90%. This stage requires strict compliance to specified gas concentrations. The sufficient insulating gas level is over 85. Therefore, quality control measures must be in place to verify accurate gas filling, preventing underfilling or overfilling, both of which can impact the unit’s overall production efficiency. Automated measurement system, Sparklike Laser Integrated pairs well with control of gas fill.
Sealing Integrity Check
The effectiveness of the gas-filled airspace is contingent on the integrity of the seal. Quality control checks should include accurate assessments of the seals to ensure they are gastight and free from defects. Any compromises in the sealing process can result in gas leakage, altering the insulating gas concentration and, consequently, the IGU’s thermal performance.
Insulating Gas Concentration Measurement
Placing insulating gas concentration measurement at the heart of the quality control process is crucial. Utilizing advanced gas level measurement tools, manufacturers can obtain real-time measurements, allowing for immediate adjustments if gas concentrations deviate from the specified levels. Integrating this measurement into the production line ensures a proactive approach to maintaining product quality.
Sparklike devices:
- Sparklike Handheld™ – for double glazed insulating glass units
- Sparklike Laser Portable™ – for double and triple glazed insulating glass units with coatings and lamination
- Sparklike Laser Integrated™ insulating gas measurement station integrated to the IG-line – for double and triple glazed insulating glass units with coatings and lamination.
Temperature and Humidity Testing
Beyond gas concentration, the quality control process can involve temperature and humidity testing to simulate real-world conditions. However, this quality assurance is optional and can be hard to execute. Also, if the quality process is done well, the IG units are prepared for the versatile weather conditions. This step ensures the IGUs will perform optimally in diverse climates, further validating the effectiveness of the insulating gas concentration in different environmental scenarios.
Final Inspection and Packaging
The last stage of quality control involves a comprehensive final inspection of each IGU. This includes a review of all components, gas concentration verification, and a check for any visual defects. Only units meeting the stringent quality criteria should proceed to packaging, ensuring that end-users receive IGUs that meet the highest industry standards.
Conclusion
In the quality control for Insulating Glass Units, the measurement of insulating gas concentration is important part to finalize the process. Placing this measurement to the production process ensures that each IGU delivers on its promise of energy efficiency and optimal thermal performance. By recognizing the significance of insulating gas concentration within the broader quality control framework, manufacturers can guarantee the reliability and longevity of their IGUs, meeting the demands of both regulatory standards and customer expectations.
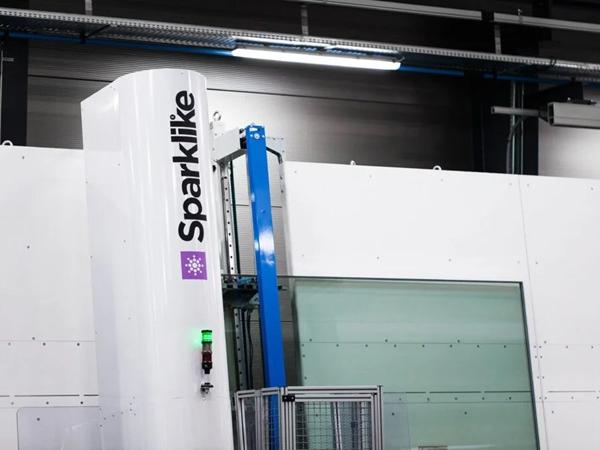

Add new comment