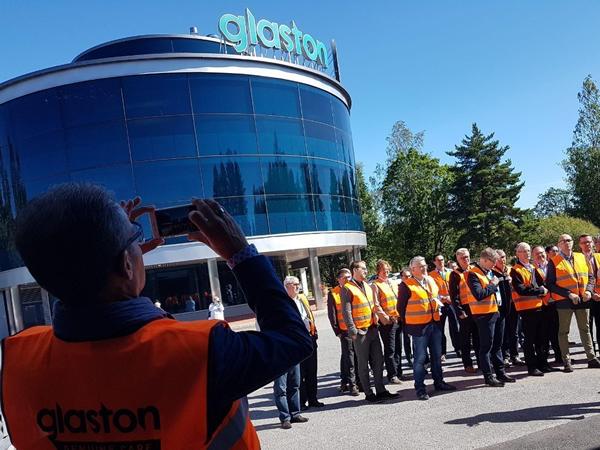
Date: 28 June 2019
Visitors had the opportunity to see the company’s glass processing machines in operation, check the actual end product quality and hear first-hand about some of Glaston’s latest innovations.
The tour began with a live tempering demonstration of Glaston’s FC Series tempering line. From large furnace displays, visitors could see essential data, such as calculations from the glass surface tension. A smaller display next to the line enabled the operators to control the process effortlessly.
“It’s becoming increasingly important for furnaces to provide a highly controlled way to temper glass,” explained Anna Holmqvist, Project Manager at Glaston, “With the latest iLooK glass quality measurement system integrated into the line, accurate quality control is delivered consistently and with ease.”
When a complex 8 mm low-e glass with extremely wide 100mm edge deletion came out of the tempering furnace, the edge kink was measured, showing an outstanding result of 0.01 mm.
Anna shared the company’s latest developments for edge kink control. “It is extremely hard to get this kind of result with a conventional machine. Yet Glaston FC Series consistently achieves excellent results,” she said.
The group then got to try out the brand-new Glaston Siru mobile application on a piece of broken glass. According to Anna, the application was officially launched on the app stores just a couple of days ago.
“With Glaston Siru, everyone can perform tempered glass fragmentation test automatically with a mobile phone,” she said. “It’s an easy and quick alternative for manual counting.”
Another special tempering furnace, GlastonAir for tempering thin glass down to 2 mm, was also on display.
Assembly factory ‒ a look within
In the automotive glass bending machine assembly section of the factory, Jukka Immonen, Product Manager, explained the differences between Glaston’s Matrix and ScreenMax.
Today, these represent the most sought-after technologies when it comes to automotive glass bending. During the tour, everyone had a chance to see how the machines and their modular bending lines look from the inside and out.
A highlight in the hall was the large Glaston Jumbo Series furnace installation. Wide and powerful, this tempering giant was a thrill for the group to see up close.
“Glaston Jumbo offers the best heating control available for high-quality jumbo glass,” Markus Kivelä, Product Manager says. “A highlight of this machine type is its unique Fusion feature, which gives you double-chamber capacity to temper different types of glass simultaneously in one run.”
Laminating like a pro
The Glaston ProL flat glass laminating line crowned the end of the tour. “That’s where all the fun happens,” said Glaston’s Product Manager Riku Färm. “The best part about Glaston ProL is its ease of operating. You only need to determine the desired sandwich thickness – and the machine is ready to go.”
Normally, glass processors have to worry about a range of settings, like furnace temperature or glass type. “With Glaston ProL, all this doesn’t matter. That’s because we’ve replaced traditional infrared heating with full convection technology. Convection doesn’t care about what kind of glass you are running, whether it is coated or not, black or transparent,” he went on. “It produces great end-product quality regardless.”
After demo runs of several glass types with different interlayers, the visitors had a chance to examine the consistent end results.
In essence, the visit to Glaston’s facilities was a tour of innovations. It provided guests from around the world with an inspiring preview of a myriadof cutting-edge technologies that will take glass processing capabilities to a level beyond any before.
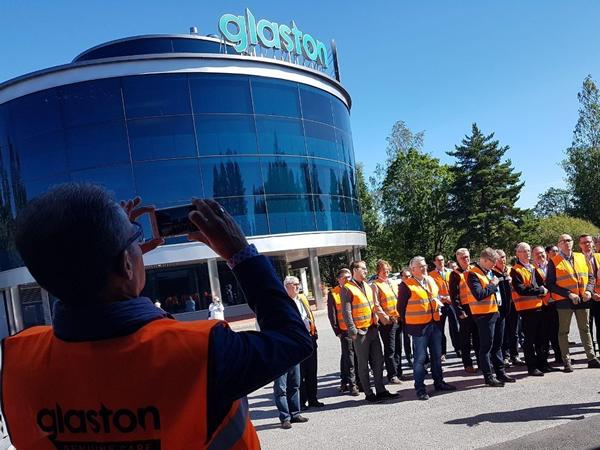

Add new comment