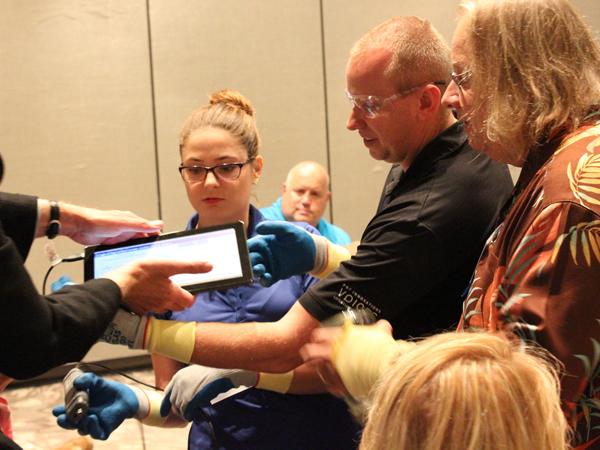
Date: 10 October 2019
During the summer, the memberships of AAMA and IGMA both voted to proceed with combining into one organization with a new name, Fenestration and Glazing Industry Alliance (FGIA), beginning January 1, 2020. The IGMA speakers took center stage to inform those at the conference about the effect hurricanes have on insulating glass unit performance, as well as how to wash and cut glass and how to conduct a frost point test.
Hurricanes and Insulating Glass (IG) Unit Performance
Bill Lingnell (Lingnell Consulting Services) is an IGMA Technical Consultant who presented "The Effect of Hurricanes on Insulating Glass Unit Performance."
“Hurricanes can have a significant impact on the long-term performance of insulating glass units, even those that are not broken by wind-borne debris,” said Lingnell.
Lingnell reviewed impacting factors, including the effects of window pressure, water and moisture in the glazing system, windblown debris and structural damage, barometric pressure and/or temperature changes.
Lingnell showed the makeup of a generic IG unit, which has a spacer, a primary seal and a secondary seal.
“A structural model of IG pressures shows atmospheric pressure, air space pressure and applied uniform lateral load,” said Lingnell. “The structural model must be in equilibrium under the applied loads as a main condition for the analysis.”
During a hurricane, along with high winds, water accumulation in glazing systems can be an issue, Lignell said. Glazing systems must be designed with water exits in mind.
"A lot of these conditions you see will affect insulating glass either directly or eventually over time, as water continues to stay in a zone and can't get out,” said Lingnell.
Lingnell concluded that, in addition to all the issues presented, changes in barometric pressure will cause stress on the edge seals and stresses in the glass, which should also be considered in designing IG units.
IGMA IG Glass Fabricators Hands-On Workshops
During several sessions at the conference, experts from the IGMA Insulating Glass Fabricators Hands-On Workshop showed off two of their stations: one demonstrating glass washing and cutting, and the other showing how to conduct a frost point test.
Bill Briese (GED) led eight participants in each session on cutting and washing. Volunteers wore personal protective equipment (PPE) that included capped sleeves, Kevlar gloves and safety glasses as Briese led them through each step.
In one demonstration, Briese asked participants to clean one half of a glass unit with 91 isopropyl alcohol and the other half with glass cleaner. Then he had them apply a strip of clear tape to each half to compare which was easier to remove. The alcohol solution proved more effective at cleaning than the glass cleaner, and the strip of tape came off that side more easily.
“Even though it was visually clean, there was a barrier between the glass and the tape,” said Briese. “You need to make sure it’s actually clean. Oils, fingerprints and detergents bring more sodiums, which can lead to dirty glass or stains on glass.”
Briese also recommended using lint-free wipes for spot cleaning and suggested changing washing fluid every day.
With glass cutting, volunteers used water and four different angle cutting wheels. Briese said the four factors that go into cutting glass successfully include the angle of cutting wheel, speed, diameter and force applied.
“The most important of these is that you want as little force or stress as possible,” he said.
Stress runs perpendicular to the edge of the cutting wheel. Sharp angles will drive more parallel, or along the glass edge.
“Cutting fluid is a very important part of scoring or cutting glass,” said Briese. “It helps keep the cutting wheel alive longer and from wearing out. Usually I recommend replacing your wheel about every shift. You’ll get really good edge quality.”
He recommended finding cutting fluid with the right amount of evaporating time for each individual’s purposes. “Don’t let the fluid sit too long, though,” he said. “And as soon as it’s scored, don’t leave it on the table.”
Lingnell and Randi Ernst (FDR Design) led a second workshop on conducting a frost point test on glass. Frost point, or lack of humidity in the glass cavity, is critical for the longevity of a sealed unit both installed and submitted for IGMA certification.
“The frost point test is used as part of ASTM 2188/2189/2190 certification accelerated aging tests to demonstrate that the hermetic seal around the parameter of the sealed unit is robust and that adequate desiccant has been placed in the cavity to draw down the relative humidity in the cavity to a frost point of at least minus 40 degrees Celsius,” said Ernst.
Those at the workshop were outfitted with appropriate safety gear, and cryogenic safety clothing was also shown and discussed. Participants were shown the “official” certification method to measure, with a D100 frost point instrument used by certification laboratories, including loading the device with dry ice and setting it to the proper measurement temperature.
They were also shown field screening methods developed by Lingnell, including utilizing small portable devices filled with solid chunks of dry ice in an alcohol bath, as well as “freeze spray” readily available from a number of suppliers.
Participants then used all these different devices to measure for visible condensation inside the cavity.
“These can be valuable screening devices to help determine the life left in an installed sealed unit and help building owners make informed decisions on when to replace units,” said Lignell.
A tablet computer was used to access small electronic sensors that were sealed within the units. These “iTiG” sensors can measure argon (or krypton), relative humidity, absolute pressure, temperature and UV light. From these measurements, one can calculate frost point, moisture by volume and thermal conductivity of the gas.
The workshop concluded with the use a device that shot a high voltage spark through the glass into the cavity, causing the gas to emit photons that were analyzed by a spectrometer for cavity gas content.
A full version of the IGMA IG Fabricator’s Workshop will be held November 12-14 in Plano, TX. Register now.
More information about AAMA and its activities can be found on the AAMA website.
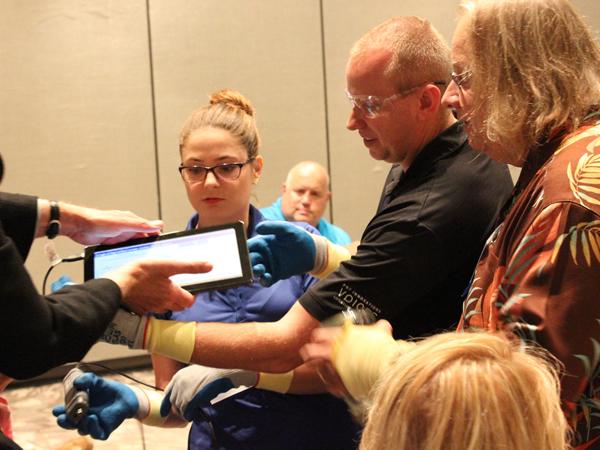

Add new comment