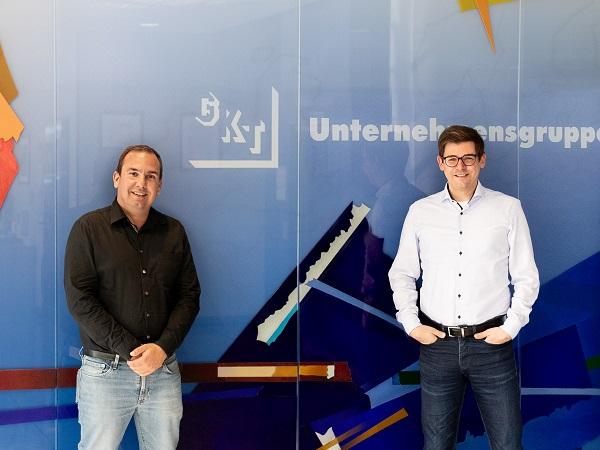
Date: 1 October 2021
There are many reasons for this, including: growing cost pressure, the increasing proportion of complex products and the goals of Industry 4.0. As a result, requirements are continually rising to a higher level. New machine generations with more sensors, high-tech control units and extensive options are not only a consequence of this development: they also contribute to the transformation. With a significantly higher throughput and increasingly common system daisy-chaining, process complexity has increased to the point that intelligent, user-friendly and flexible software is necessary for companies that want to produce at full potential.
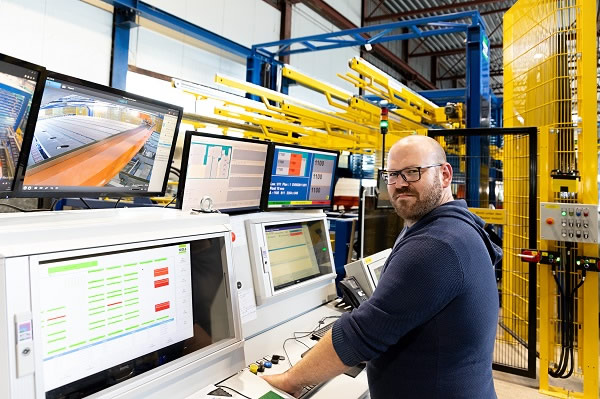
Overarching machine optimisation and centralised software solution
At the beginning of this year, the GKT Group from Brakel in Germany (Eastern Westphalia-Lippe) geared up for the future by expanding its production technology and implementing a new software system. For even greater flexibility, automation and further growth, the company invested in a double edging and drilling machine, a highly automated float glass cutting system with a breakout system and an insulated glass line.
Almost in parallel, the company switched to an ERP and production planning software from HEGLA-HANIC that drives the machines and processing lines according to need. It optimises individual production steps, automates them in precise synchronisation with the cycle, and monitors and transparently maps them. For the newly implemented ERP functionality, all processes – such as order entry, work preparation, purchasing, warehouse management and logistics – are centrally pooled and directly accessible.
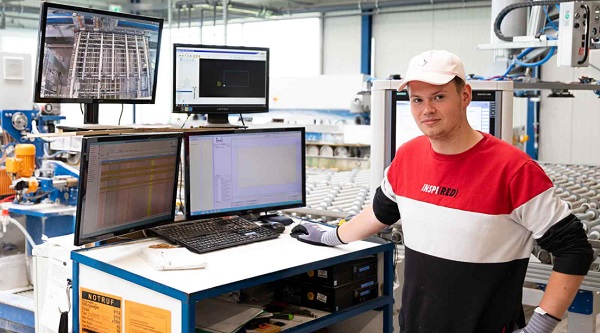
Higher complexity, shorter cycles
“Every system has its time,” said GKT Managing Director Peter Egg with conviction. “We were well positioned, our processes functioned properly and we probably could have continued to work with the existing software.” However, our experiences in recent years showed that the complexity of incoming orders would continue to increase, as would customers’ desires for shorter delivery times and ultimately, the competitive pressure driving faster and faster cycle times. “As a medium-sized provider, we are appreciated for delivering on schedule, for our high quality, broad product spectrum – and for our flexibility,” reported Egg.
That is why his project requirements included creating an overarching, company-wide data structure with even greater clarity and transparency in the spirit of integrated corporate management. Simple visualisation of KPIs, along with real-time access to every single order and an overview of the available capacity on the toughened glass furnace or the insulated glass line, were on his shopping list. The goals of maximum cycle time optimisation, process support for automated and semi-automated workflows and optimal dovetailing were defined in partnership with HEGLA-HANIC.
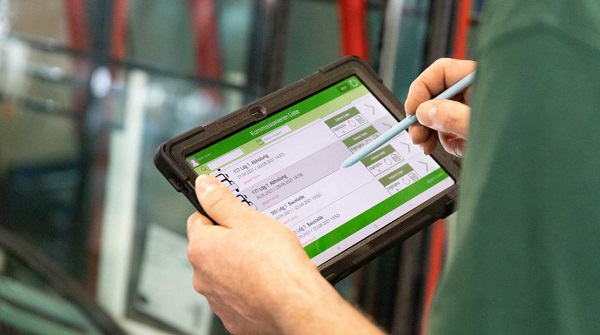
Networked work areas with integrated processes and data
Since the production processes and commercial tasks were migrated to the new system, the individual work areas are networked even more closely. For example, all orders are first recorded in the ERP and then broken down into their processing steps by the system. Warehouse inventories are checked and, if required, a purchase requisition is generated that can be digitally exchanged with one or several suppliers. The PPS takes factors such as delivery dates, machine capacity, inventory and material utilisation into consideration while optimally compiling orders and then forwards them to the relevant production stations as a work order.
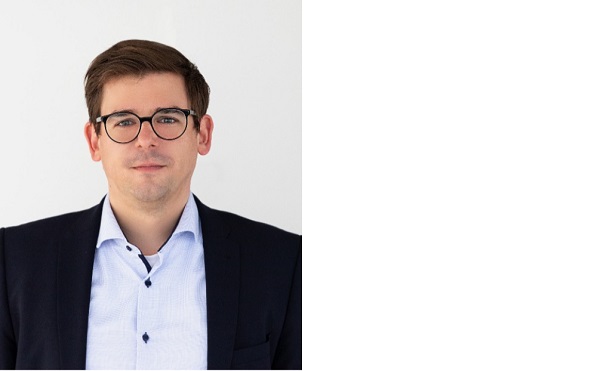
“For our production, this means a high level of automation and daisy-chaining the individual processing steps with short cycle times and a degree of workflow perfection that is impossible to achieve without the corresponding software support,” explained Dr. Jan Schäpers, the managing director of HEGLA-HANIC. The new software also contributes other benefits when it comes to handling complex and precisely timed workflows, and above all, work preparation. Production progress can be tracked and machine capacity can be viewed at any time, and if priorities change, a machine malfunctions or an urgent order comes in, managers can react immediately. The existing production plan is adjustable based on recommended or free parameters. “In this way, it is possible to ensure a continuous production flow even in the face of unexpected incidents, either manually or through the user-friendly system, across all processing stations,” added Schäpers.
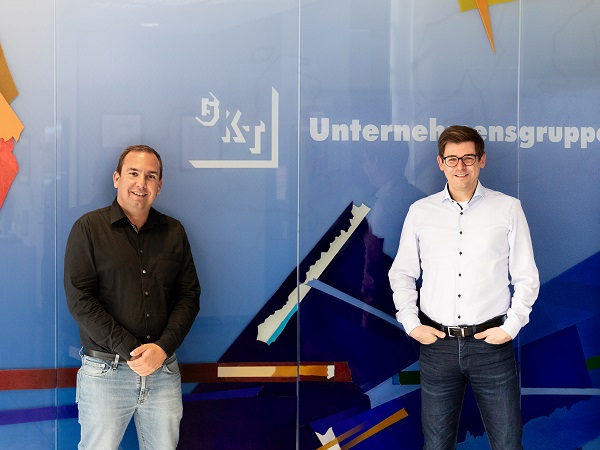
Accelerated processes through centralised data management
“We were able to boost the level of digitalisation and automation in Production. The status of production orders can be viewed at almost any workstation, which dramatically accelerates our processes and ensures that orders are completed on schedule and with the quality required,” said Peter Egg. The master and order data are centrally filed, making them available error-free to Accounting, Production and even Logistics. The processes for recording orders were also simplified. With the integrated CAD module, processing has been automated using saved templates and a customer-specific free form can be either directly drawn or imported as a DXF file.
The position of a hole or mullion can be directly saved in the system and automatically transferred to the production system. The software also has a shipping module that provides digital added value and direct feedback. As soon as a unit is sent to Shipping, feedback is sent to the order system, enabling production progress to be tracked transparently and at any time. To provide integrated support to Shipping, HEGLA New Technology developed a tablet app specifically for GKT and its process requirements. It completely digitalises, documents and simplifies the workflows in picking and shipping.
In the new HEGLA-HANIC system, the next (external) digitalisation step has already been completed for GKT. Both customer orders and in-house orders for purchased parts and services can be digitally exchanged between the IT systems.
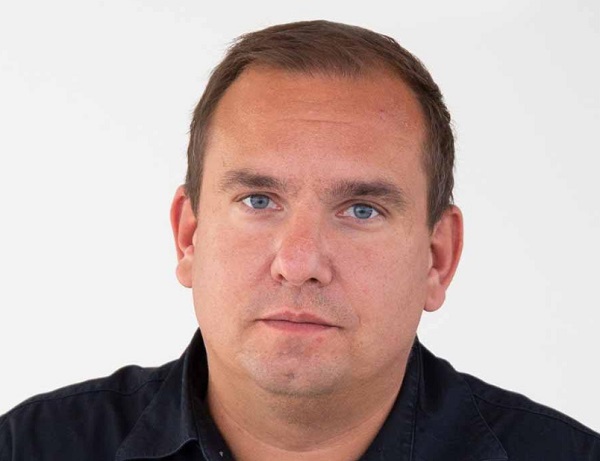
Re-evaluation of the value chain
“The decision to implement new software is also a question of trust, mutual goals and constructive collaboration,” explained Egg. Together, the companies created a vision and were able to implement it in a very short time. The agreed-upon project duration of only seven months was comparatively short. The successful implementation shows all the more how focused the analysis and optimisation of processes and their integration into the software can be, even in a project with such a high level of complexity.
GKT Managing Director Peter Egg designed the timing to support another goal for the well-being of his employees: the project schedule needed to be as compact as possible in order to avoid unnecessary stress for the participants.
The GKT Group in the Eastern Westphalian town of Brakel was founded in 1978 and currently has around 150 employees. Peter Egg is the second generation to manage the company. The product portfolio includes insulated glass, single-pane safety glass, laminated glass and mullions for insulated glass in a wide variety of designs and combinations. Germany and its immediate neighbours comprise the core sales region of the GKT Group. The Group’s customers are window companies, metalworkers, joiners, distributors, interior converters, workshops and private/end customers.
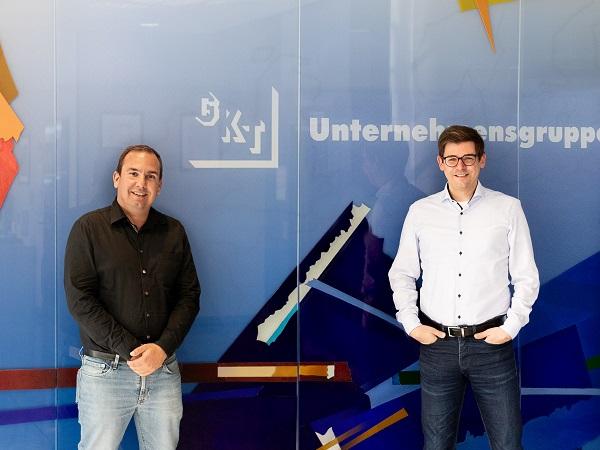

Add new comment