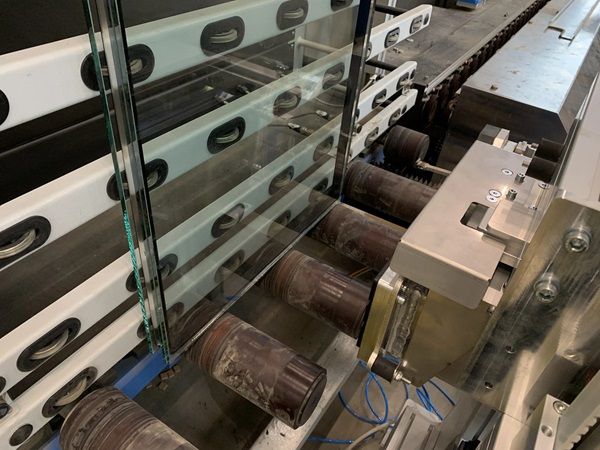
Date: 30 September 2024
The use of gas filling equipment to introduce inert gases such as argon, krypton, or xenon between the glass panes is an established method to improve thermal insulation and energy efficiency. However, even with the most advanced filling machines, challenges such as inconsistent gas fill levels, leaks, or contamination can arise, threatening the overall integrity of the units.
For manufacturers, the implications of such issues extend far beyond immediate production defects. Poor gas filling accuracy can lead to long-term performance degradation, customer dissatisfaction, and costly warranty claims. In competitive markets, where energy efficiency standards are continuously rising, ensuring the gas concentration in each IGU meets specified requirements is more crucial than ever.
But there is a solution to this common production challenge. At Sparklike, we offer a suite of non-invasive gas measurement devices designed to support manufacturers in verifying gas concentration inside IGUs without disrupting production lines. Our devices provide real-time, reliable data, allowing manufacturers to detect and address issues immediately, thus minimizing downtime and reducing costly rework.
The Role of Gas Filling Equipment in IGU Production
Gas filling equipment is an important part of the manufacturing process, designed to inject the specified gas at precise concentrations. There are various types of gas filling machines, each tailored to the specific needs of production lines, whether for small-scale production or large automated facilities. These machines are generally built to handle different gas types, filling pressures, and production rates.
However, even when working within optimal parameters, challenges persist:
- Leakage during or after filling: Sealant issues or equipment malfunctions can lead to gas escaping during the filling process.
- Inaccurate fill levels: Calibration problems or improper settings can result in the gas concentration falling below the required percentage, significantly reducing the insulating value of the unit.
- Contamination: During the filling process, air or moisture can inadvertently be introduced into the IGU, compromising the quality of the gas fill.
These issues, if undetected, not only affect the immediate quality of the insulating glass unit but can result in long-term performance failures, making robust quality control essential.
Sparklike’s Non-Invasive Gas Measurement Solutions: A Critical Quality Control Tool
Traditional methods of gas concentration measurement in IGUs have been invasive and time-consuming, requiring sample units to be destroyed or production lines to be halted for testing. Sparklike’s technology changes this. Our non-invasive devices enable manufacturers to perform real-time gas concentration measurements on fully assembled IGUs without disrupting the production process.
This offers several key advantages:
Cost Reduction: Minimizing rework, reducing scrap rates, and avoiding customer complaints related to poor performance significantly lowers operational costs over time.
Increased Production Efficiency: By enabling non-destructive testing, Sparklike devices allow continuous quality control without the need for production line stoppages.
Accurate and Immediate Feedback: Our devices provide precise data on gas concentration, allowing operators to adjust equipment settings or address potential issues instantly.
Ensuring Compliance with Industry Standards
In addition to addressing operational challenges, manufacturers of IGUs are increasingly held to higher regulatory standards, particularly in the construction and energy efficiency sectors. National and international building codes often require specific gas concentrations in insulating glass units to meet thermal performance criteria. For instance, maintaining a 90% argon fill in double-glazed units is often necessary to achieve U-value targets set by regulatory bodies. Failure to meet these standards can lead to product recalls, or even penalties and the loss of certifications. Watch video from Pilkington Polska about their Argon quality control.
Sparklike devices play a critical role in helping manufacturers maintain compliance. By providing an accurate, non-invasive means to measure gas concentrations in-line or post-production, our solutions ensure that each unit meets the required gas fill levels before leaving the factory floor. This not only helps companies stay compliant but also safeguards their reputation as producers of high-quality IGUs.
Enhancing Production Line Integration with Sparklike Technology
One of the significant advantages of Sparklike’s gas measurement devices is their ability to seamlessly integrate into existing production environments. Whether a manufacturer operates a fully automated production line or a more hands-on, manual process, Sparklike devices can be easily incorporated to enhance quality control measures. Explore Sparklike devices.
For highly automated production lines, our Sparklike Laser Integrated can be integrated to provide continuous, real-time monitoring of gas filling accuracy without interrupting the flow of production. This enables manufacturers to detect deviations from target gas concentrations immediately, reducing the risk of producing subpar units and ensuring the efficiency of the entire operation.
In smaller-scale or more manual environments, Sparklike devices Sparklike Laser Portable and Sparklike Handheld offer the flexibility to test specific batches or even individual units as needed, providing a cost-effective solution to maintain consistent quality. This adaptability ensures that manufacturers of all sizes can benefit from the precision and reliability that our technology offers.
The Business Case for Investing in Sparklike Solutions
Investing in quality control equipment is not just about meeting regulatory requirements or improving production efficiency—it’s about protecting the long-term profitability of the business. Poor gas fill quality can lead to increased warranty claims, customer dissatisfaction, and damaged brand reputation. By using Sparklike’s non-invasive gas analyzers, manufacturers can mitigate these risks while simultaneously optimizing production processes.
Operational Cost Savings: Sparklike’s solutions minimize costly rework, reduce waste, and help manufacturers optimize their processes, resulting in lower operational costs over time.
Reduced Warranty Claims: Sparklike devices help to identify and prevent underfilled or leaking IGUs from reaching the market, drastically reducing the risk of warranty claims and replacements.
Improved Customer Satisfaction: Consistently delivering IGUs with the correct gas concentration enhances product performance, which leads to fewer complaints and greater customer loyalty.
Conclusion: Setting New Standards in IGU Production with Sparklike
In an industry where precision, efficiency, and compliance are vital, investing in advanced quality control technologies is no longer optional—it’s essential. Sparklike’s non-invasive gas measurement devices provide manufacturers with the tools they need to ensure that every IGU produced meets the highest standards of quality and performance.
By integrating our solutions into your production line, you can address common gas filling challenges, improve operational efficiency, and protect the long-term profitability of your business. Whether you are facing issues with gas fill accuracy, leakage, or contamination, Sparklike offers the innovative technology required to maintain the integrity and reliability of your insulating glass units.
Contact Sparklike for more information and support on measuring argon concentration in IGUs.
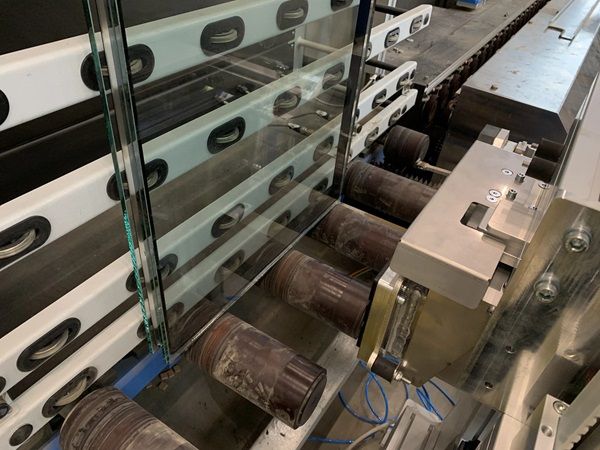

Add new comment