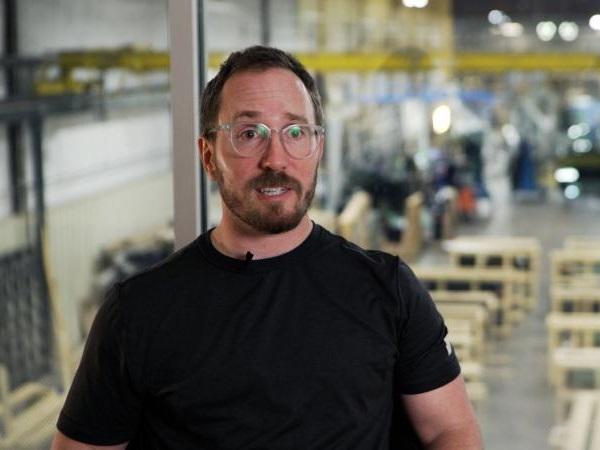
Date: 16 November 2021
When making first-class architectural glass, being able to produce high-quality glass consistently is key. Tristar Glass Inc. specializes in fabricating large architectural glass that can be used in interior and exterior applications. The manufacturing process needs to be well thought-out and completed, as they are committed to delivering their customers with the highest quality glass in the shortest possible lead time. After Glaston upgraded Tristar’s existing lamination lines, they have been able to manufacture all of their products with a significantly lower rejection rate.
Since starting their business in 2005, Tristar has become a certified glass fabricator and laminator. They are constantly looking for ways to further improve their own processes to be able to offer their customers even better quality and shorter lead times.
Tristar’s lamination line was upgraded with Glaston’s ProL oven and nip roller section. They could not be more pleased with their purchase and the cooperation.
– This has been a real game changer for us, says Tristar’s Mechanical Engineer, Robert Carlson, excitedly.
– The technology we now have when we use the ProL-zone makes a large difference in the consistency of the heat transfer to the glass, which directly translates into a faster overall process as we have fewer rejections, he continues.
Glaston is integratable with existing machinery
It was important for Tristar to be able to run all types of glass with various different thicknesses through the same line. Furthermore, it was crucial for them to upgrade their equipment as efficiently as possible to reduce downtime for the production. Glaston was able to upgrade Tristar’s already existing technology which saved both time and money.
– It was considerably cheaper and faster to upgrade our existing equipment than to install brand new equipment, Carlson says.
Upgrading their already existing equipment also reduced the overall footprint of the equipment at their facility.
– Thanks to the adjustable convection heating process, the ProL enables us to do every type of glass with the same oven and nip section. That saves us from having to have multiple ovens for different glass types, Carlson praises.
Drastic reduction in rejection rates
Tristar is committed to ensuring that their products are defect free. For this purpose, they use real time distortion measurement and comprehensive defect tracking. Since they started their cooperation with Glaston, their rejection rate is lower than ever before.
– Our rejection rate went from 35-40 percent to maybe three percent, Carlson states.
Overall, Carlson has been pleased with their decision to upgrade their machines with Glaston.
– I think Glaston’s machines are great for both lamination and tempering. Thanks to the ease of use, long-term durability and the upgrade ability, I would definitely recommend Glaston to others, he concludes.
Related products
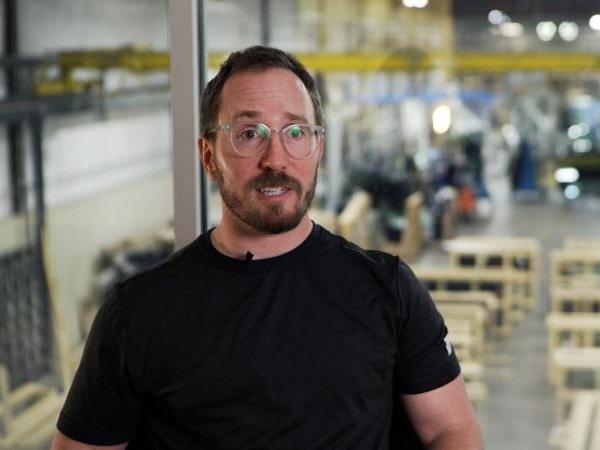

Add new comment