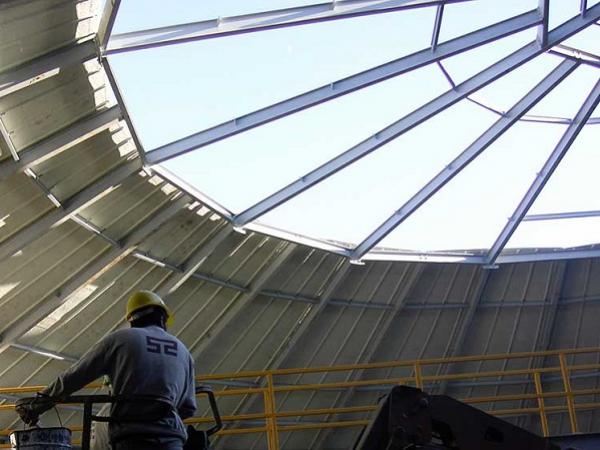
Date: 7 March 2019
These profiles were tested at the Material Testing Laboratory of Politecnico di Milano; a series of mechanical and physical experimental tests were performed according to the European code EN 13706. The properties of TRIGLASS® High Performance materials result higher than the requirements of the E23 class, that presents the most stringent quality parameters.
Click here to download the technical sheet with the mechanical and physical properties achieved from the TRIGLASS® High Performance profiles.
Pultruded profiles in buildings and infrastructure
In the last decade the use of FRP pultruded profiles in civil and building engineering was more and more widespread. This material presents many advantages respect to the traditional techniques: resistance to aggressive environments, lightweight, speed of execution, greater load bearing capacity, optimum compatibility with prefabricated structures, great geometrical adaptability.
The applications are multiple:
– shell and sandwich structures for industrial or residential environments [1];
– pedestrian and vehicular bridge structures or decks light structures for emergency situation[2];
– retrofitting of historical structures [3];
– reinforcement of new concrete and prestressed concrete – elements [4], [5].
The pultruded profiles used as structural elements must present mechanical and physical properties higher respect to the classical pultruded materials used for other purposes. In particular they must be characterized by a tensile, compressive and flexural strength and modulus higher than a specific imposed limit. They have to present an higher bearing and shear capacityin order to guarantee a good mechanical behavior in the connection. Moreover they must have an high fire reaction and resistance.
The regulations
Due to the increasing use of these materials, it was necessary to develop a standardization document in Europe for the production of FRP structural elements and for the structural design. In September 2018 the European Technical Committee 250 (CEN/TC250) presented the “Prospect for new guidance in the design of FRP structures”, and some European Assessment Documents were published both for the structural profiles and the use of FRP bars as reinforcement of structural elements.
[1] Abdolpour H., Garzon-Roca J., Escusa G., Sena-Cruz J.M., Barros J., Valente I. 2016. Development of a composite prototype with GFRP profiles and sandwich panels used as a floor module of an emergency house. Composite Structures, 153: 81-95
[2] Sonneschein R., Gajdosova K., Holly I. 2016. FRP composites and their using in the construction of bridges. Procedia Engineering, 161: 477-482
[3] Carozzi F.G., Colombi P., Fava G., Poggi C. 2018. Mechanical and bond properties of FRP anchor spikes in concrete and masonry blocks. Composite Structures, 183: 185-198
[4] Rossini M., Nanni A. 2019. Composite strands for prestressed concrete: State-of-the-practice and experimental investigation into mild prestressing with GFRP. Construction and Building Materials, 205: 486-498
[5] Dal Lago B., Taylor S. E., Deegan P., Ferrara L., Sonebi M., Crosset P., Pattarini A. 2017. Full-scale testing and numerical analysis of a precast fibre reinforced self-compacting concrete slab pre-stressed with basalt fibre reinforced polymer bars. Composites Part B, 128: 120-133
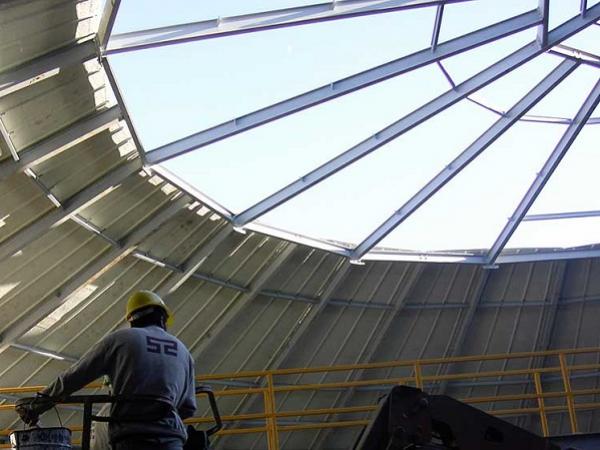

Add new comment