As automation progresses, more and more robots are finding their way onto the shopfloors of the flat glass industry. Robot technology improves process reliability as well as the quality of glass products.
Where are robots currently being used? And what specific advantages do they bring? An analysis based on years of user and technology know-how.
ROBOTS SPECIALLY FOR THE GLASS INDUSTRY
As an industry pioneer, LiSEC has long been concerned with the question of how robot technology can be used in the glass industry. Material-specific factors must be taken into account, such as the gentle placement of glass to prevent breakage or the appropriate suction cup technology. Through extensive tests in a realistic environment, potential weak points were identified, and optimal solutions found to ensure smooth integration of robots into the production process.
Robots are currently used at three points in flat glass processing in particular: during loading/unloading and frame setting in insulating glass production and in the tempering process during tempering bed loading.
LOADING AND UNLOADING
In IG production, robots with a special gripper are suitable for loading from a glass rack onto a vertical line or from a vertical line onto a glass rack. They can lift glass weights of up to 480 kg! This means that the insulating glass line can be loaded fully automatically with individual panes or unloaded with insulating glass elements.
The robot's vacuum suction gripper adapts flexibly to the products and glass blocks. The linear arrangement of the suction pads enables the elements to be turned if necessary, and the fixed support fingers and extendable suction pads enable elements with thermoplastic spacers to be transported gently.
WHY ROBOTS FOR LOADING AND UNLOADING THE IG LINE?
Automated loading and unloading ensures a continuous production. If the panes are set down manually, the suction cup can slip and damage the glass surface. Robots always set down with the same precision, so the optimized suction and set-down process ensures consistent product quality. In conjunction with identification of the glass racks, robots can also stack flexibly on different transport containers.
FRAME MOUNTING
Another possible application for robots in insulating glass production is as a link between the frame production line and the IG line. Here, the robot takes spacer frames with butyl applied on both sides from a vertical transport line for coated frames, aligns the frames in the required position using a gripper system and swivels to the IG line. There, the frame is mounted with high positioning accuracy on the glass pane, which is aligned exactly in the middle of a predetermined position on the frame setting station. Such systems are suitable for all common rigid spacer bar types. Even Georgian bars can be processed.
WHY ROBOTS FOR FRAME MOUNTING?
Frame mounting requires precision and efficiency. The use of a robot enables optimized frame positioning, resulting in high-quality end products. As the frame is always clamped on all sides from lifting after butyl coating to placement on the glass, this results in a process-stable production sequence for all frame sizes. Additional advantages are the extended spatial possibilities resulting from the robot's large range of movement. This means that the frame production can be positioned at almost any angle to the IG line.
TOUGHENING BED LOADING
During the tempering process in the furnace, the glass is heated to approx. 700 °C and then rapidly cooled using an air stream. For this process, uniform heat distribution on the glass pane is critical. If this is not ensured, waves are created on the glass surface, which have a negative impact on the optical quality of the end product. To prevent uneven heating, the tempering bed is covered with precisely positioned glass, calculated by a powerful optimization software.
The actual positioning is carried out by a robot, which ensures the stable and continuous loading and unloading of the tempering bed. When the pane reaches the removal position, the robot lowers the required suction cups on the gripper and activates the vacuum. Far more flexible than roller conveyor systems, it can turn the pane if necessary and place it in the exact position calculated directly at the toughening furnace inlet. The gripper with its low-pressure suction cups can also process panes with cut-outs.
WHY ROBOTS FOR TOUGHENING BED LOADING?
Continuous loading of the tempering furnace ensures the best possible utilization. It also ensures that production is of consistent quality around the clock, as the toughening bed is always loaded according to the same algorithm.
MORE ABOUT AUTOMATION:
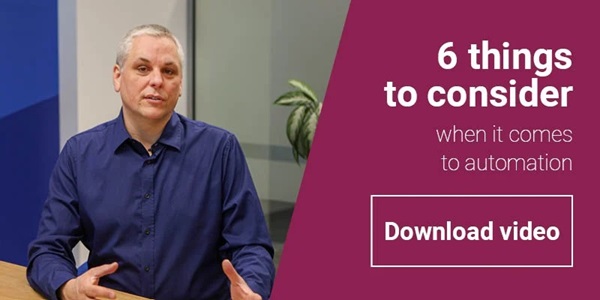
SUMMARY
Robots offer advantages over human employees: they carry out operations with the same precision time and time again and do not become tired or inattentive in the process. They take over repetitive and time-consuming tasks, while employees can concentrate their skills on more demanding activities, such as loading and unloading the insulating glass line, setting frames or loading the tempering bed. This leads to an increase in overall productivity and product quality.
Comments
The integration of robots into the flat glass industry offers numerous benefits, including improved process reliability, enhanced product quality, and increased efficiency. As technology continues to advance, we can expect further innovations and optimizations in robotic applications within the industry. Soundville Music Studio Nashville