This paper was first presented at GPD 2023.
Link to the full GPD 2023 conference book: https://www.gpd.fi/GPD2023_proceedings_book/
Author: Dr. Juliane Brandt-Slowik, SCHOTT Technical Glass Solutions Jena, Germany
Within the large material class “glass”, different types have the amorphous structure as well as the time-dependent glass transformation behavior in common. The individual structure is formed depending on the composition of the glass. The structure of a material determines its properties and this in turn, enables its use in certain applications.
Glass Composition
The most common glass is soda-lime glass, which is widely used in architecture, in automotive glazing as well as for glass containers. The structure-property correlations are shown when we compare traditional borosilicate glass with standard soda-lime glass. The chemical composition of these glass types in shown in Figure 1.
Network formers like silicon dioxide (SiO₂ ) and boron oxide (B₂ O₃ ) build up the interconnected backbone of the glass network. In classical borosilicate glass, the amount of network former, at 94 %, is very high. Network modifiers like sodium oxide (Na₂ O) and calcium oxide (CaO) alter the glass structure by breaking bonds and thus reducing the process temperature in the glass production.
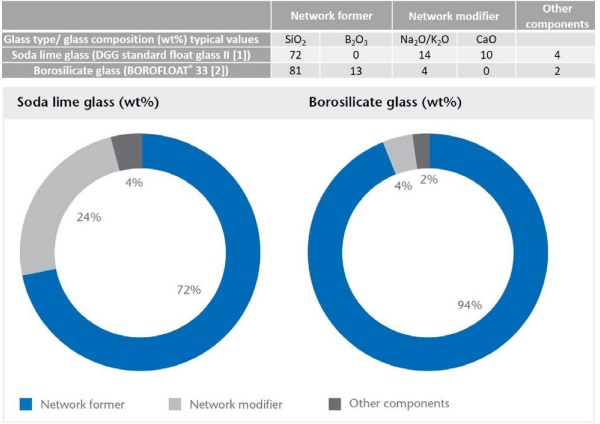
Glass Structure
The structure of soda-lime glass is dominated by groups of structural units, where one silicon atom is connected to three bridging oxygen atoms and one non-bridging one (Q³-groups), leading to a network connectivity of approximately three, see Figure 2 left. The negatively charged non-brigding oxygen atoms (red in the Figure) are charge-balanced by network modifier ions (green in the Figure). Overall the glass network has a relatively large ionic bond share. The packing density of the atoms in the glass is comparatively high leading to a stiffening of the glass structure, i.e. a high elastic modulus.
The borosilicate glass structure exhibits a highly connected glass network, Figure 2 right.
There is a large number of Q⁴ groups including AIO⁻₄ and BO⁻₄ groups. The network modifier ions bind preferentially to AIO⁻₄ groups, the remaining network modifier ions to BO⁻₄. As well as approximately 23% BO₄ , the majority of boron is present as trigonal BO3 species (77%) [3]. Only less than 1-2 % non-bridging oxygen atoms are present [4] in the glass structure formed of BO₃ –rich clusters in a SiO₂ rich matrix. The bond structure in the borosilicate glass is predominantly covalent. The packing density of the borosilicate glass is comparatively low. The free volume is large, which leads to a relatively elastic behaviour, i.e. a low elastic modulus.
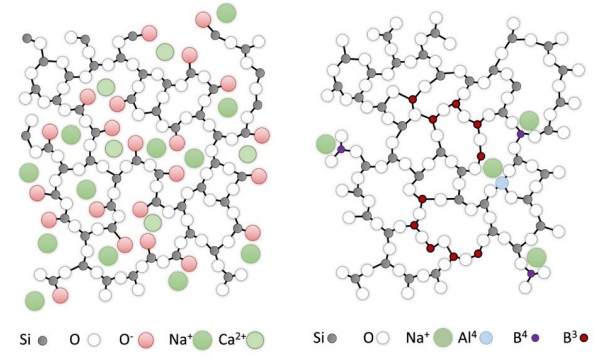
Because of the high amount of network modifiers in soda-lime glass in contrast to borosilicate glass, many non-bridging oxygen atoms are formed, see formula 1, and the glass network connections are decreased. The decrease in network connectivity leads to a change of the properties.
Besides the well-known application of borosilicate glass in the chemical laboratory, the special structure leads to the unique properties, which enables the use in a diverse range of applications.
Mechanical properties
In this section we will compare the mechanical properties of BOROFLOAT® 33 with standard soda-lime glass. The first part focuses on abrasion and scratch tests, whereas the second part is about indentation and impact tests.
A typical abrasion test is the PEI (porcelain enamel institute) test, Figure 3. The microscopy pictures after abrading the glass surfaces in this set-up show for BOROFLOAT® 33 minor surface defects, whereas for sodalime glass the defects are longer, deeper and more pronounced. In comparison to soda-lime glass, BOROFLOAT® 33 is particularly abrasion resistant.
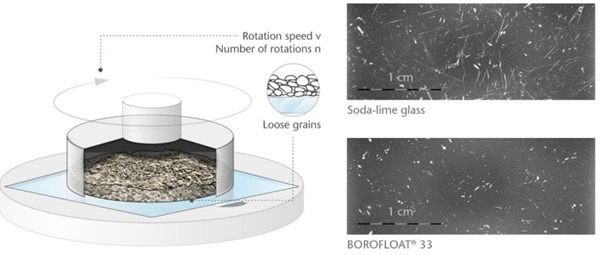
Scratch tests were carried out while varying the load between 1N and 7N, see Figure 4 (Content is subject of pending patent applications of SCHOTT). For soda-lime glass the results show chipping starting at 4N. The scratch resistance is much higher for BOROFLOAT® 33 than for soda-lime glass. When using Vickers-Indentation test, a diamond tip is pushed onto the glass surface, set-up see Figure 5. Afterwards the imprint is investigated under a microscope. For soda-lime glass at 2N four cracks around the imprint have occured starting at the corners. BOROFLOAT® 33 even at double load (4N) does not crack, which shows that the crack initiation load is much higher in comparison to sodalime glass.
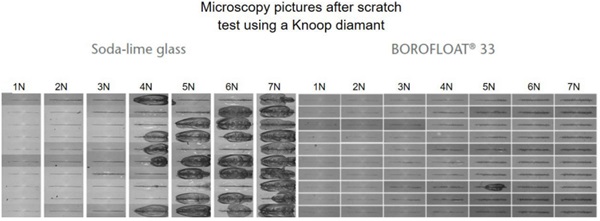
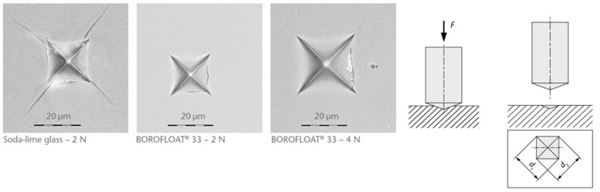
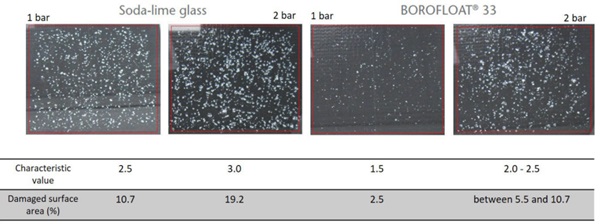
Stone impact test (DIN EN ISO 20567-1) was carried out for soda-lime glass and BOROFLOAT® 33 at 1 bar and 2 bar. The damaged surface area at 1 bar is 10.7 % for soda-lime glass, while it is only 2.5 % for BOROFLOAT® 33. At 2 bar the damaged surface area is 19.2 % for soda-lime glass, while it is between 5.5 and 10.7 % for BOROFLOAT® 33. The stone impact resistance is much higher for BOROFLOAT® 33 in comparison to soda-lime glass.
The sharp impact resistance in different impact angles was verified using basalt grit, Figure 7. Under a microscope, pictures of the damaged surfaces show less defects in number and extent for BOROFLOAT® 33 in comparison to soda-lime glass, Figure 8 (Content is subject of pending patent applications of SCHOTT). The borosilicate glass shows a high sharp impact resistance in the basalt impact test. During basalt impact test on BOROFLOAT® 33 less defects occur in comparison to sodalime glass. As less defects scatter less light, this leads to less haze for BOROFLOAT® 33, see Figure 9, which is especially beneficial for sensors and cameras behind the glazing. The content is subject of pending patent applications of SCHOTT.
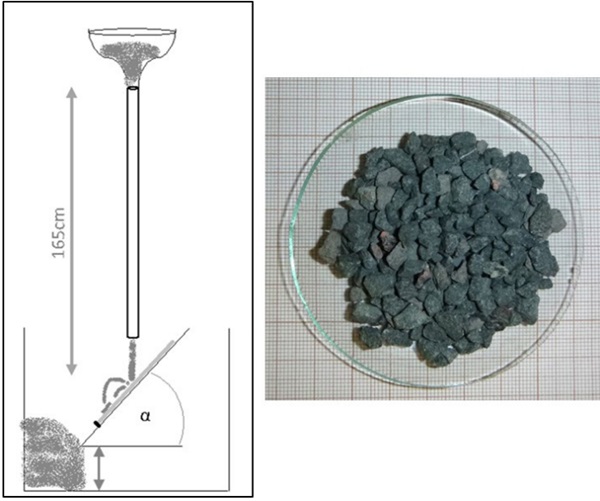
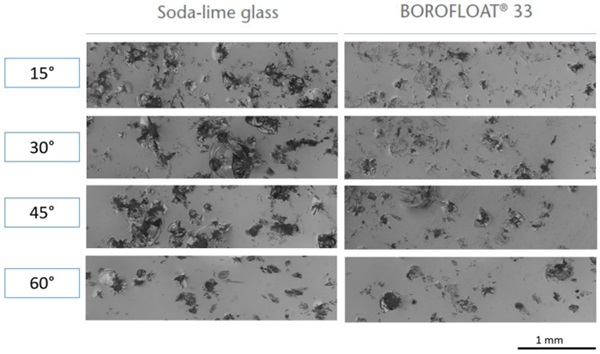
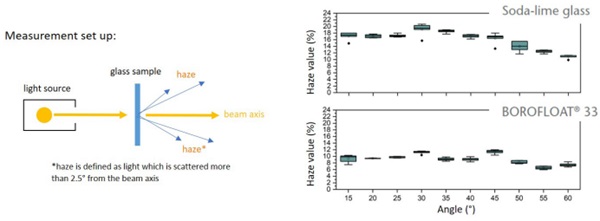
Conclusion of the mechanical properties
In comparison to soda-lime glass, BOROFLOAT® 33:
- shows a much higher sharp impact resistance and crack initiation load
- is more resistant in the basalt grit impact test leading to less haze
- shows a much higher scratch resistance and is particularly abrasion resistant
Thermal properties
One important difference between soda-lime glass and traditional borosilicate glass is the coefficient of linear thermal expansion (CTE). BOROFLOAT® 33 has a low coefficient of thermal expansion, Figure 10, which leads to a high resistance to thermal shock as well as to thermal gradients. A typical device, which relies on the thermal performance of the glass is in the oven door, in a pyrolytic oven. An oven with a pyrolysis function uses very high temperatures (up to 500°C) during the cleaning process in order to burn off any leftover food. All that remains after that process is ashes, which can be removed easily using a brush or a cloth.
Chemical properties
The chemical durability of borosilicate glass is close to that of pure silica glass due to the special structure of the glass. Compared to soda-lime glass, BOROFLOAT® 33 has a significantly higher hydrolytic resistance. The reason for that is mainly that the number of sodium ions in the glass network is significantly lower and the sodium ions present are bound stronger in the glass structure, see Figure 11.
BOROFLOAT® 33 is used to protect priceless historic documents, like the Papyrus Ebers, Figure 12 left, which is an unique cultural document. Medical recipes were written down on Papyrus in Egypt, approximately 3500 years ago. The scroll is in total 19 m long and divided into 29 individual parts. Therefore, the chemical properties of any protective glass will have a large impact on the historic documents. Standard soda-lime glass was used in the past as protection. This unfortunately led to glass corrosion and damage of the historic assets. The glass corrosion forms a white film, see Figure 12 right (*), which impairs the legibility of small traces of the writing and damages the document. Studies by Graf et al [5] proved that the traditional borosilicate glass BOROFLOAT® 33 prevents the adverse formation of salt crystals because of its chemical stability. As well as the chemical properties, the optical performance of the glass is of great importance here as well. The clarity of the glass and the absence of a colour shift is very important to enable the digitization of this historic document.
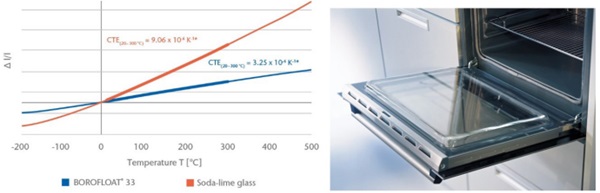
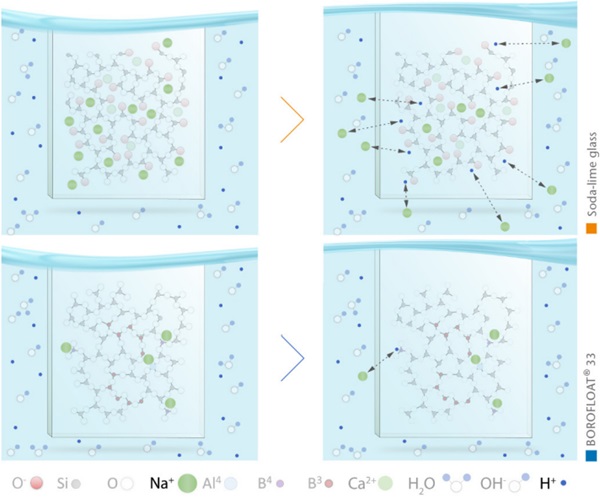
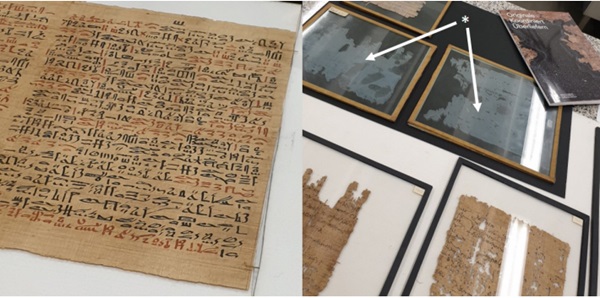
References:
[1] www.hvg-dgg.de/fileadmin/dateien/verein/Standardglass_IIa.pdf
[2] www.us.schott.com/borofloat/english/production/index.html?us-origin=en-US
[3] Boffy et al., High thermal neutron flux effects on structural and macroscopic properties of alkali-borosilicate glasses used as neutron guide substrate, Nuclear Instruments and Methods in Physics Research B, 2015
[4] Manghnani et al., Raman, Brillouin, and nuclear magnetic resonance spectroscopic studies on shocked borosilicate glass, American Institute of Physics, 2011
[5] Graf et al., Composition and source of white precipitations on the inner side of papyrus glazing, Restaurator 39/4, De Gruyter, 2018
CV
Since 2018, Dr. Eng. Juliane Brandt-Slowik has been working in Product Management at SCHOTT Technical Glass Solutions (TGS) GmbH in Jena, while this February she took over the position Manager Sales & Business Development. Born in 1987, she is married and mother of five. The title of her PhD thesis (2020) is “Structure, solubility and crystallization behavior of bioactive borosilicate glasses”. From 2015 to 2018, she was working as scientific employee at Otto Schott Institute of Materials Research and beforehand she studied materials science at Friedrich Schiller University. She has volunteered as a mentor for doctoral students and in the management of a social institution.
Comments
Soda-lime glass and borosilicate glass have distinct structural differences that influence their properties. Soda-lime glass has a more rigid network due to its high ionic bond share and dense atomic packing, resulting in a high elastic modulus. In contrast, borosilicate glass features a highly connected but less densely packed network with predominantly covalent bonds, leading to greater kapitalanlage immobilien elasticity and a lower elastic modulus. The presence of BO₄ and BO₃ clusters in borosilicate glass further contributes to its unique structural flexibility, making it more resistant to thermal shock compared to soda-lime glass.