This paper was first presented at GPD 2023.
Link to the full GPD 2023 conference book: https://www.gpd.fi/GPD2023_proceedings_book/
Authors
- Antti Aronen, Jukka Immonen, Tuomo Nuottimäki, Mikko Rantala - Glaston Oyj Abp, Finland
Abstract
The complexity of the automotive windshields and sunroofs has increased during the last years with complex shapes and increased sizes as also with new coatings and increased screen-printed areas. These features have had challenges in uniformly heating the glass with radiation. With increased forced convection the local heat transfer differences can be smooth and the heating better controlled. In this study, the profound reasons behind the main benefits of glass preheating by increased convection in automotive windshields (WS)/ sunroof (SR) production are opened. The goal of the article is to present the reasons why glass convection preheating is important for heating control and with examples present its benefits. The study describes the main parts of the heat transfer and material behavior phenomena that take place during this process stage. At the end of the article will be the sum-up of the key results and takeaways.
Introduction
The optical quality and shape accuracy demand for bent automotive glasses has increased. New advanced driver-assistance systems (ADAS) bring more camera solutions to windscreens which need better optical quality, especially in locations where cameras are installed. Also, modified shapes and cut-outs bring new challenges to the bending process. On top of this the use of coatings and large screen-printed areas, combined with glass transparency changes increase the complexity of the windshield (WS) and sunroof (SR) heating in the bending process.
Automotive WS and SR bending process is a complex process where the control and accuracy of the heating and cooling parts of the process are playing a key role in the quality of the final product. The typical bending process can be divided into four parts:
Preheating phase, where glass is heated fast to around 500 °C.
Bending phase, where glass is heated in a controlled manner to bending temperature, and same time glass is bending naturally and/ or forced to the right shape. This can include the press.
Annealing cooling phase, where glass is slowly cooled to around 400 °C to obtain wanted edge compression and inner tension.
Forced cooling phase, where glass is cooled fast close to handling temperature.
The target in WS and SR bending processes is to produce glasses with good end quality and a good production rate. Good end quality contains e.g., the right shape, good visual quality, and the right stress level. Good end quality and good production rate are contradictory targets because the higher production rate brings bigger challenges in the optical and shape quality of the glass. Recently also the demand for energy-efficient products has increased and this has brought challenges to make changes in the process to avoid heat losses.
The main part of the process for bending results is the bending phase where glass is heated from 500 °C to about 600 °C – 650 °C to allow the time-dependent bending to happen and for glass to get in the right shape. For the bending, the viscosity needs to be low enough to allow the glass to creep. The creeping speed is temperature depended. In the bending phase the glass is bent by controlling the local glass temperature with radiative heaters and the glass is supported by the bending tool frame which helps to get the right shape.
In this study, the focus is on the preheating phase where glass is prepared for the bending phase. The target in preheating is to heat the glass to around 500 °C as fast and uniformly as possible. At 500 °C glass viscosity is still so high that time-dependent bending in a short time scale does not happen. However, the limitation for heating speed is coming from the temperature uniformity. If the temperature differences around the glass are getting too high, that can cause unwanted deformations in the glass or glass breaks due to the high stresses or thermal shock, especially around the edge area. All these unwanted problems need to be avoided and temperature uniformity over the glass area needs to be controlled. The challenges in the windscreen and sunroof bending are not only the shape and optical quality requirements, but also the coatings, enamels, and different transparencies in different areas of the glass as shown in Fig. 1.
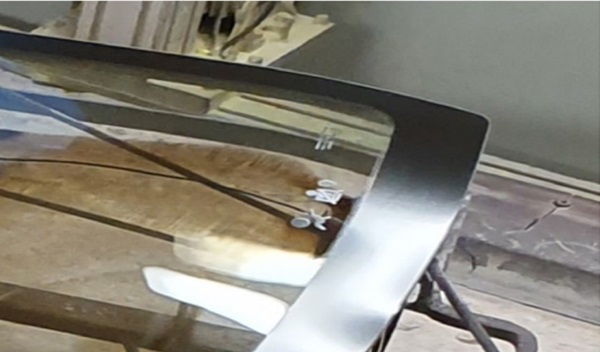
To better control the process in the bending phase, the heating in preheating phase should be uniform to avoid different areas being heated unevenly. This is important until the glass temperature is around 500 °C. After that, the heating needs to be controlled in the bending furnace to focus heat in certain areas to help the bending. The more uniform the glass temperature is before the bending chamber, the easier it is to control bending with heating, and the temperature differences in the bending furnace due to radiation are decreased.
This study is focused on comparing the radiation and convection heating in automotive WS and SR production. The following text will first present the possible quality problems due to problems in preheating. Then discussed the pros and cons of radiation and convection for heating. In the end, theoretical examples are shown the advantages of convective heating in a preheating furnace.
Quality problems in automotive WS/ SR due to problems in preheating
Several quality issues may occur in automotive windscreens or sunroofs due to problems in preheating. Some of these quality issues can come also in the bending phase, but if the problem is in preheating phase, then those cannot always fix in the bending phase. The two most common quality issues which can come after problems in preheating are issues in the shape of the glass or optical distortions. These both are due to too-hot areas in the glass where bending deformations are formed at the wrong time of the process or for too long. Glass bending happens when glass is hot due to the creeping behaviour of the glass.
The creeping or time-dependent deformation speed is sensitive to the glass temperature. Examples of shape and optical distortion issues are shown in Fig. 2.
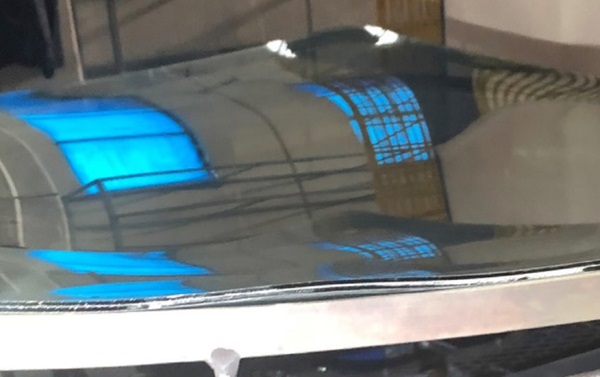
When the glass temperature increases above 500 °C the viscosity of the glass decreases to a level where the creeping deformation happens. Fig. 3 presents the relative bending speed of glass due to creeping [2]. Relative bending speed w' is the factor that presents how fast bending w is relative to elastic deflection we of the plate w'=w/we. Relative speed is related to the viscosity of the material. Then the total bending due to creeping wc is the bending speed integrated over the time

Notable is that creeping speed is increasing exponentially with temperature and this causes problems to control the bending of the glass when glass temperature is increasing. As an example, the tip of the cantilever beam which is bent 1 mm due to its weight bends about 10 mm in 1 second at 620 °C.
Because the glass creeping speed increases at around 550 °C the preheating is done until about 500 °C. Then in preheating creeping should not happen. After preheating glass is moved to the bending phase where the process will be easier to control by adjusting the heating at different areas and with local temperatures to control the local bending. Bending is easier the more uniform the glass temperature is at the beginning of the bending phase.
The third quality issue where preheating has an effect is the burn line. The burn line is the phenomenon where distortions or a dim white line is formed close to the borderline of screenprinted and clear or coated glass areas on the clear/coated glass side. This issue is coming due to too high-temperature differences between screen-printed and clear glass during the preheating. The fourth issue is glass breakage which can happen during preheating. The reason for glass breakage is the high thermal stresses due to large temperature differences especially close to the edge region. The solution to avoid these four problems is uniform heating over the glass area.
Comparison of convection vs radiation heat transfer in glass preheating furnace
Using electric heaters is an effective way to heat the glass in a furnace. Typically, in electrical heaters, the resistance of the heater material converts electrical energy into heat with high efficiency. This process is called Joule heating [1]. Heat is transferred to surrounding air and material by different heat transfer methods: radiation, convection, or conduction. The main heat transfer method for electrical heaters is radiation where the heating coil is at a high temperature, and it emits heat to the surrounding. The amount of heat transfer depends on the temperature and emissivity of the heater and surrounding material. In the furnace, natural convection is also involved, and it influences convective heat transfer. This kind of furnace where radiation is in the key role of heat transfer is called a radiation furnace.
Another furnace type is called a convection furnace. Typically, in this kind of furnace, the base is the radiation furnace with electrical heaters, but the amount of convection from total heat transfer is increased with circulating forced convection [3]. Quite often the heaters have also been installed behind the cover to reduce the radiation heat transfer from electrical heaters to glass. In that case, the cover is first heated and then the cover radiates heat to the glass, but then the cover temperature can be lower than the temperature of the heating element and the emissivity of the cover surface can be changed to reduce the radiation. Besides convection air is circulated with a blower over the electrical heaters to heat the convection air.
This increases the convection air temperature and at the same time, the heating effect increases. The convection preheating furnace is beneficial to use in the automotive WS/SR process. In a convection preheating furnace the heating elements are inside the convection boxes. Then the heating elements do not radiate straight to glass, but heating elements heat the convection box and convection air which goes through the box. In the end, the heat from heating elements is transferred to the glass with convection and with radiation from the convection box surface. However, the radiation temperature for a convection box is lower and more uniform than if the heat is radiated straight from the heating elements. The illustrative image of a preheating furnace with forced convection is shown in Fig. 4.
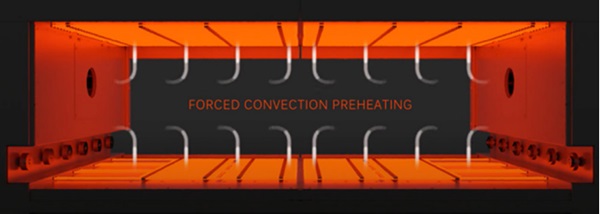
To compare the radiation furnace and convection furnace it is important to compare the total heat flow. The total heat flow to glass is the combination of the radiation and convection as shown in Eq. (1).
The radiation depends on the combined emissivity ε of the heating surface and the glass, Stefan-Boltzmann coefficient σ (5.67·10⁻⁸ W/m²K⁴), glass area A, and the temperatures of the surroundings Ts and glass Tg in fourth power. In calculations of radiation, the temperature must deal with absolute temperature [K]. Convection depends on average convective heat transfer coefficient h, glass area A, and the temperature difference between ambient Ta and glass Tg. In a convection furnace, the radiation surrounding temperature Ts and ambient temperature for convection Ta are close to each other.
The major differences in emissivity over the glass area bring challenges in radiative heating. The coatings, enamels/paintings, and glass transparency differences change the radiative heating over the glass surface compared to the heating of the clear sodalime glass. Also, the bending frame absorbs radiative heat differently compared to glass and causes different heating effects around the edge area of the glass. Typical emissivity for glass is 0.83, for coating 0.1, and for enamel 0.9.
The reduction of the radiation in preheating the glass helps to heat the glass more uniformly when emissivity changes over the glass area. At the same time, the forced convection is increased to increase the heating rate and uniformity. The advance in forced convection is that the heating effect in different materials is more uniform than the heating effect with radiation.
Convection heating also has benefits in heating control. To increase the heat flow in the radiative heating, the temperature of the radiation heater needs to be increased. Because of the different emissivity of the coatings and enamels the heating effect differences with radiation increase with higher radiation temperature. In the end, this causes more problems in process control.
The differences in heating effect with convection are smaller than with radiation. There are some local differences in forced convection, but if the nozzles are far from the glass surface, then the convection is more uniform. With convection, the heating rate can be increased by increasing the temperature of the convection air and the flow speed, which increases the convective heat transfer coefficient. With a convection furnace, the heating rate can be increased by 50% compared to only a radiation furnace. With forced convection with circulating air, the energy consumption of the preheating process can be decreased compared to only radiation. Two points help to reduce the energy consumption in the windscreen preheating process with forced convection.
The first point is that glass can be heated at a lower preheating furnace temperature and thereby reduce the heat loss from the process. The second point is that radiation shields are not needed in the process. Radiation shields increase the thermal mass in the process. All extra thermal mass in the process increases energy consumption because all the material in the process needs to be heated at the process temperature. One extra point to mention is that hot air circulation is an energy-efficient way to increase heat transfer with convection. This closed-air circulation loop avoids unnecessary heat loss with hot air and all the energy used for heating the air is transferred with hot air to the glass.
Temperature differences in the glass during preheating
In the following theoretical results, the effect of forced convection on heating time and the temperature differences in glass with different coatings has been presented. The calculations have been done in the onedimensional calculation for a 2.1 mm + 2.1 mm thick windscreen glass pair. The emissivity of the radiative surface is 0.9 and the convective heat transfer coefficient is 30 W/m²K for cases with forced convection and 3 W/m²K for cases without forced convection. The heating is done in three preheating phases and furnace temperatures are 250 °C, 375 °C, and 500 °C unless otherwise mentioned.
The heating curve for clear glass has been presented in Fig. 5. In these results it is shown that forced convection increases the heating rate compared to case without forced convection. In the results, it can also be seen that if the glass is heated without forced convection, it needs over 50 % longer heating time to reach the same temperature.
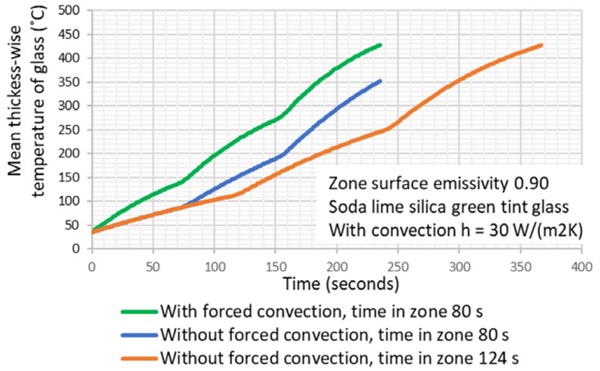
The heating curves for Low-E coated and enameled (black screen-printed) glass are shown in Fig. 6. In these cases, the emissivity for Low-E coated glass is 0.09, and for enameled glass 0.94. The temperature differences between Low-E coated and enameled glasses for the same three cases (with forced convection, without forced convection with longer heating time and without forced convection, but higher furnace temperature) are shown in Fig. 7. In the results in Figs 6 and 7, the heating rate of enameled glass is higher than Low-E coated glass.
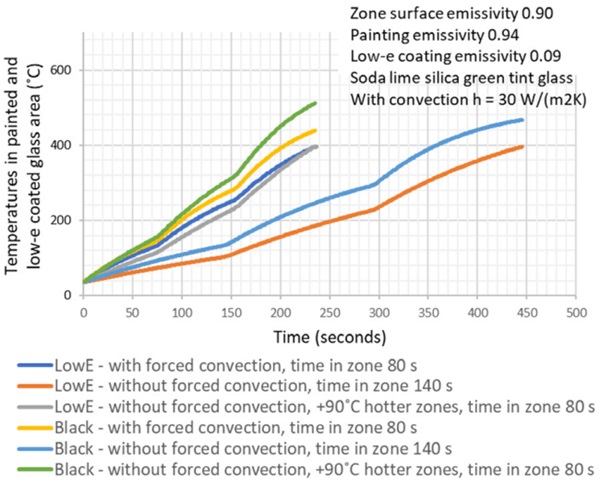
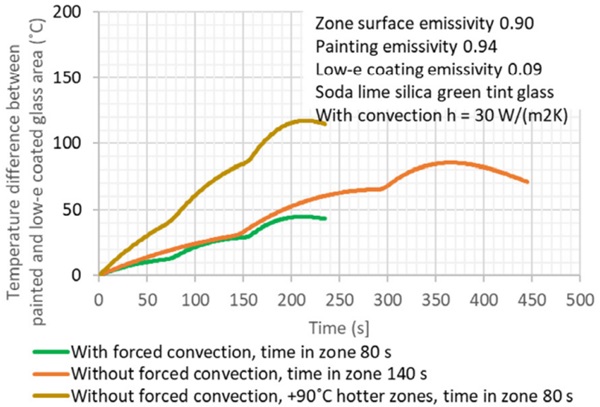
However, the temperature difference between enameled glass and Low-E coated glass is smaller if forced convection is used. To get the heating rate of low-E coated glass to the same level with and without forced convection, if the forced convection has not been used the furnace temperature needs to be increased by 90 °C in these cases. In that case, also the heating rate of enameled glass increases, and it gets easily overheated, if low-E coated glass is reached to right temperature level. The temperature difference between low-E coated glass and enameled glass can get close to 100 °C if the glass is heated too fast with only radiation.
From results in Figs 5 and 6, temperatures of clear glass are between Low-E coated and enameled glasses when the same furnace settings are used. For this reason, the comparison in Fig. 7 shows the largest possible temperature differences between these three different glass types.
Summary
The target of preheating is to heat the glass close to glass bending temperature as uniformly as possible, but at the same time as fast as possible. The bending of glass due to creeping slowly starts around 550 °C so preheating is done until the glass is about 500 °C and then the glass is moved to the bending section where glass is heated mainly with radiation. In the bending section, the local glass temperature and bending are controlled with a dense heater matrix. The good glass temperature uniformity before the bending section gives a longer time window for shaping.
To better control the uniformity of the glass in preheating, forced convection is used to balance the heat transfer in glass areas with different emissivity. In the case of only a radiation furnace, the temperature differences between enameled and coated areas can come high and cause problems in the glass bending especially at the edge areas where enamel has been used. With a furnace with forced convection, the issues of bending shape and optical quality can be decreased or avoided. Also, the risk for burn lines and glass breakages is smaller with uniform heating due to forced convection.
In the preheating furnace with forced convection, the heating time can also be decreased compared to only a radiation furnace. This is due to the extra heat transfer with high convection and heating time can be 30 % shorter than with a radiation-only furnace. With shorter preheating time it is possible to make the bending line shorter.
References
[1] Cleveland, C.J., Morris, C., Dictionary of Energy, 2nd Ed., Elsevier,2015, doi.org/10.1016/B978-0-08-096811-7.50010-X.
[2] Aronen, A., Modelling of Deformations and Stresses in Glass Tempering, Tampere University of Technology, PhD Thesis, Tampere, 2012, URN: ISBN:978-952-15-2816-3
[3] Rantala, M., Heat Transfer Phenomena in Float Glass Heat Treatment Processes, Tampere University of Technology, PhD Thesis, Tampere, 2015, URN: ISBN:978-952-15-3692-2