First presented at GPD 2019
On the other hand, we saw the increasing introduction of double and multiple-layer façades including a return to natural ventilation in the 90’s and the new millennium. Today we see the Closed-Cavity-Façade (CCF) as a promising and innovative way to develop new possibilities especially for high-rise buildings which may come to the same rank within the next years.
The following report will provide an overview over the existing systems und it will point out the challenges and the chances of this advanced new façade system. Furthermore, there will be presented several reference projects of the past years, both completed and under construction.
The report shows the way to a functional proper design and it illustrates the most important issues of a good quality assurance management.
1 Façade Technology in Changing Times
Continuous improvements of the available high-performance glazing’s and framing in the past 30 years led to much greater energy efficiency. Another milestone was the development of the Double-Skin-Façade Structures in the 90’s, which were used mainly in commercial and high-rise buildings. In addition, the decentralization of HVC elements (e.g. cooling ceilings, thermally activated concrete slabs and decentralized ventilation systems) showed a lot of hybrid possibilities with natural window ventilation.
Natural ventilation through windows with manual operability – in opposition to central mechanical ventilation systems with only central control systems – should provide both an improved energy balance as well as a high user acceptance. Especially in high-rise buildings, which are exposed to strong winds, the protection of sunscreens with a second skin or at least a local pane of glass deflecting the wind influence increased the usability and lowered cooling needs considerably.
Often, however, there were doubts regarding the higher necessary investment and higher costs for maintenance and cleaning connected to Double-Skin-Façades. This led often to solutions that were still constructed as a single skin for the windows, neglecting the increasingly needed sun protection caused by the heat up of our atmosphere.
The idea of openable windows in a skyscraper was implemented in conjunction with a less expensive single skin facade by the newly developed „Parallelausstellflügel” (parallel swinging wing) which is motor-driven. This enabled a dynamic wind deflector shield if finely metered for a continuous supply of fresh air independent of wind influences. Buildings as the Main Tower Frankfurt show that this idea even was taken for investment projects.
One of the most prominent recent examples of projects for the equipment of a tall building with single-skin façade and openable windows was certainly planned by Drees & Sommer Fassadentechnik for the renewal of the twin towers of the Deutsche Bank at Frankfurt.
But the single skin façade technology continues to have a significant flaw: rather dark sun protection glazing and compared to the Double-Skin-Façade significantly higher energy input with less daylight in the building are the common consequences. A solution for extremely demanding building envelopes with best properties for insulation and sun protection was however still missing. This incorporates the wish for a novel appearance of landmarks with high recognition value. So, we ask:
Is the Double-Skin-Façade not more but the best of all bad solutions?
2. From Double-Skin-Façade to Closed-Cavity-Façade
A number of positive examples of DoubleSkin-Façade buildings have been reported. In case an open competition for the erection took place, prices were often more moderate than expected. Books were published at the turn of the millennium, how engineering of façade and ventilation may be optimised. Nevertheless, the examples with limited function, heat-up or short circuiting from exhaust to supply air exist in large numbers as well. Especially if openings to the outside or distances between inner and outer skin are reduced to much, such faults appeared.
Therefore, all Double-Skin-Façade projects of Drees & Sommer façade technology have been developed from scratch with a clear message to the owner: the unavoidable excess temperatures in the façade corridor require the provision of a mechanical minimum ventilation of those spaces that are located behind a Double-Skin-Façade.
An improvement of this situation can be achieved, if designed with care, by an efficient flow through the facade corridor to maintain these excess temperatures as low as possible. Well-designed corridor façades show a typical heat-up of the exhaust air of 4 – 6 Kelvin under full insolation and with active sunblind in the corridor. Not so well-designed corridor façades often show 10 – 15 Kelvin under the same conditions. This will make a real difference in usability of the natural ventilation of the rooms behind.
This is however determined by the geometry and exposure of the corridor and by the shape and size of the ventilation openings and does need aerodynamic expert’s advice. Therefore, the often-cited energy efficiency of DoubleSkin-Façades is only true for a good design of their ventilation.
Among the best-known examples of projects in Germany is seen the Post Tower at Bonn as an excellent example of natural ventilation and daylighting / sun shading with a DoubleSkin-Façade. This high-rise of 166 m by architects Murphy Jahn, Chicago, was awarded the Emporis Skyscraper Award in silver after its completion in 2002. The façade planning was executed by Drees & Sommer façade technology, aerodynamic consultancy and measurements by I.F.I. Institute for Industrial Aerodynamics.
This insight created a new idea for a DoubleSkin-Façade-Type called Closed-Cavity-Façade or abbreviated „CCF“. The combination of the advantages of a single-skin façade with those of a Double-Skin-Façade led to a nonventilated double-skin with very good heat insulation to the inside and a larger depth to the outside.
3. The advanced façade technology CCF
The façade-type Closed-Cavity-Façade (CCF) avoids the polution of its inside surfaces as it is not exposed to ventilation. Condensation is suppressed with the supply of dried air to the inside, but the amount is very low, as the unit is constructed to be almost air tight. The good sound insulation and sun shading properties of a double-skin are maintained. If one needs a possibility for natural ventilation an openable flap can be combined with the CCF element that under normal circumstances will not be openable.
The supply of dry air is controlled with its dew point temperature to outside and surface temperatures. The larger is chosen the socalled dew point distance to the critical surface temperature (for example, the inside of the outer single-glazing), the safer the design is prepared against impairment of the view by condensation. A fact that bothers with many not so well-designed ventilated Double-SkinFaçades. Two fundamentally different systems are available on the market today. One system produces the dried air in local units, the other with central units. Some air tight tubes to the façade elements are hence necessary, but of only small diameters.
In the decentralized dry air conditioning (Figure 1 / Type C) drying boxes are used, which are positioned in close proximity to the façade elements. They can be installed either in the cavity below or in the ceiling void above the elements. Important in any case is the permanent accessibility of the corresponding access panels in order to maintain the units and to replace the desiccant cartridges employed before saturation.
Another possibility is the use of distributed conditioning units called “AHC units”, that perform the regeneration process within the device, thus no replacement of any drying agent is necessary. Such a system was implemented for the first time in the new corporate headquarters of Energie AG Upper Austria at Linz. The local façade is made of a triple insulating glass with krypton filling on the inside. Sun-shading in the cavity and a single pane of glass to the outside. Even some openable CCF devices were realized on one façade of this interesting project.
Quite different paths were taken with a compressed air-fed CCF version (Fig. 1 / D type). The dry air is produced in a central unit and controlled for all connected elements. This allows a very efficient way of drying this air (for example, via adsorption) and is easy to maintain. Furthermore, the elements are readjusted individually with regard to their supply needs of this dried and compressed air. The air supply network is made of steel or stainless-steel pipes to cover the higher pressures employed for the distribution in small diameter tubes.
The planning of the air lines and the central compressed air plant is usually handled by the HVAC planning team, but incorporates some important interfaces to the façade planning and production. Final definition of the design parameters such as dimensions of the compressed air lines are made however by the executing façade contractor. This is especially important, to define and ensure clear interfaces for responsibility and liability regarding the correct operation of the entire system at the end.
A written system warranty with a term of at least ten years is usually required in the contracts for CCF façades.
The CCF design is attractive as it costs little or no additional investment compared to a conventional Double-Skin-Façade. This is mainly due to the fact that the relatively modest additional investment for the air lines and the central compressed air is compensated by avoiding the opening and cleaning as found on Double-Skin-Façades. In addition, the annual maintenance cost for the window sash in a conventional Double-SkinFaçade are roughly equivalent or even higher than the maintenance costs of the dry-airsystem of a CCF.
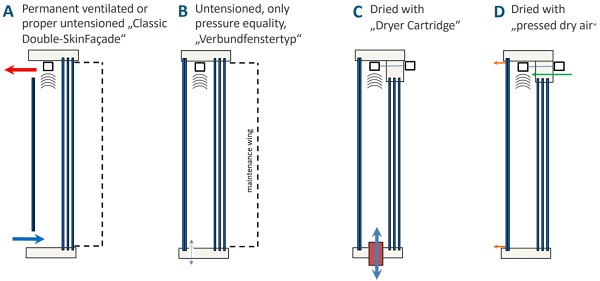
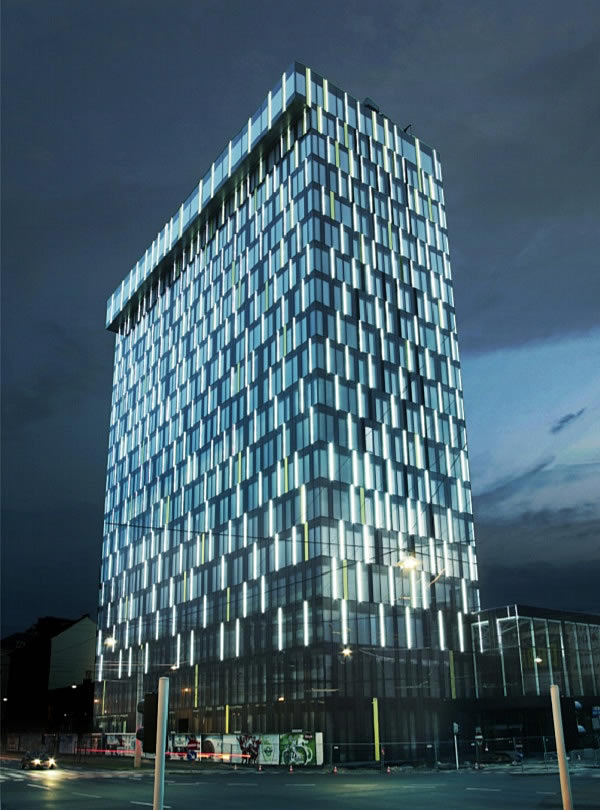
4. Opportunities and challenges of the CCF technique
In addition to the above mentioned technical advantages of a CCF for maintenance and upkeep we see some architectural and design advantages for this type of façade. Due to the elimination of inside cleaning the profiles of the frame are significantly slimmer. Furthermore, considerably larger glass sizes are possible compared to Double-Skin-Façades with wings on the inside.
High visual quality at the prospect of interior and exterior façade make the CCF extremely interesting for architects and building owners (see Figure 3 and 4).
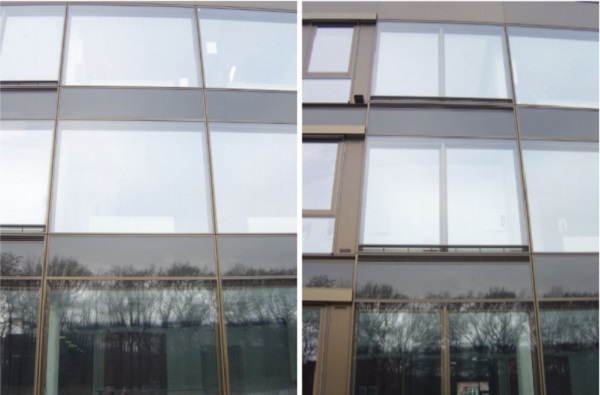
In addition, new possibilities for the use of directing light with sun protection systems are created. The material choice for the sunblinds is broadened as there is no wind or rain exposure in the CCF and materials need only be stable to temperature and sun exposure. As heat is not transported mainly by convection but through radiation the direction of the blinds’ rotation axis is not so important.
The heat insulation on cold winter days is excellent with possible Ucw values of about 0.6 to 0.9 W/m² K for CCF elements with interior triple glazing. Depending on the ratio between windows and opaque elements in a façade even very high thermal insulation requirements may be met.
However, the new façade-type CCF also brings some challenges for facade planners and constructors. Elements installed in the closed cavity are hardly to exchange or to be maintained. Therefore, new ways of motorizing and controlling elements may be useful with activators outside the closed cavity. All active or passive elements in the cavity need to survive high temperatures (of up to about 80 °C – 90 °C) and long life without maintenance. The framework of the cavity needs to keep air tight under those high inner temperatures and may be exposed to high temperature gradients in respect to the surrounding building elements.
The heat insulation of the interior (triple) glazing of a CCF element is not only needed for invernal insulation but mostly for the reduction of so-called secondary heat transmittance under full insolation in summer. Instantly after signing the contract it is very important that real life test of those components be carried out by the contractor before he is allowed to produce the façade in large amounts. Following this rule it has been done at on one of the first high-rises to incorporate the CCF facade in large scale, the new Roche Building 1, a 178 m high-rise in the heart of Basel, Switzerland.
5. CCF – Implemented Innovation
In the past decade the CCF façade type has been successfully realized on a number of projects. One of these projects is the Power Tower in Linz.
For the Roche building department, a comparison was prepared between features of a conventional Double-Skin-Façade vs. those of a Closed-Cavity-Façade. The results were so convincing that the new high-rise headquarter for Roche Diagnostics at Rotkreuz, near to the “Zuger-See”, was built with the same CCF technology and completed in 2010 in advance to the Roche Tower at Basel. Until this date there were no or only a few practical experiences on which the owner would rethink his decision for the main headquarters.
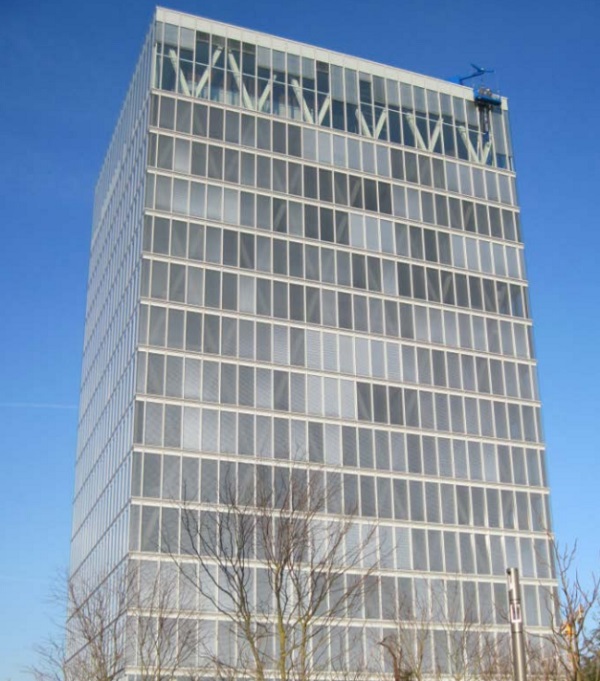
Another CCF project was carried out on the premises of Roche at Kaiseraugst for a new laboratory building.
Now the new Roche Building 1 at Basel is completed and currently the highest skyscraper of Switzerland. The clearly white monumental appearance in the early morning hours results from the absolute clean white surface of the sun-protecting lamellas , that is both a unique building view und CCF-resulted design advantages.
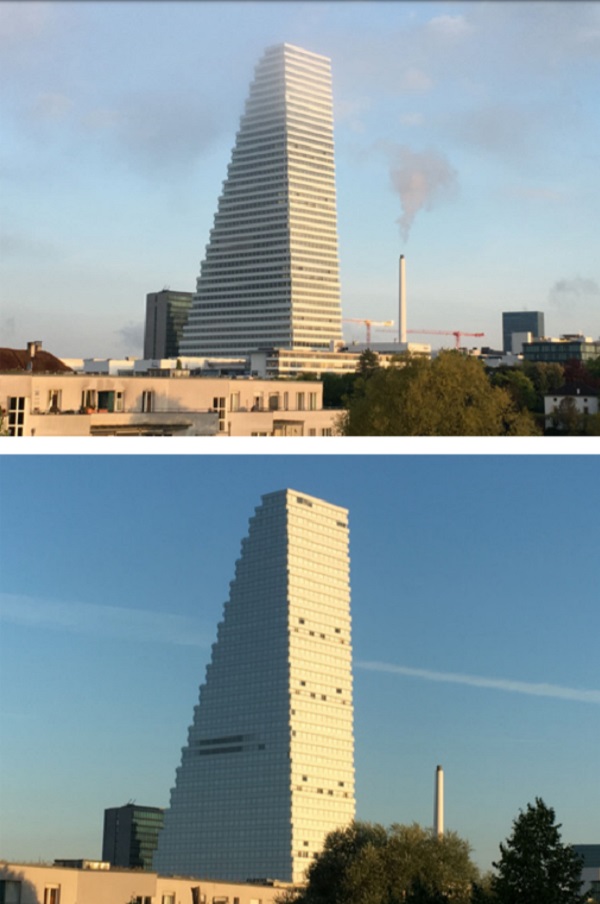
In order to evaluate as much performance factors as possible of the CCF-elements, two independent test-companies were ordered with CCF-Mock-Up’s and elements in a two-step procedure to verify the properties of this façade type for Roche.
In addition, a test-office was equipped with the CCF-elements and the interaction with users and HVAC plants was tested as well.
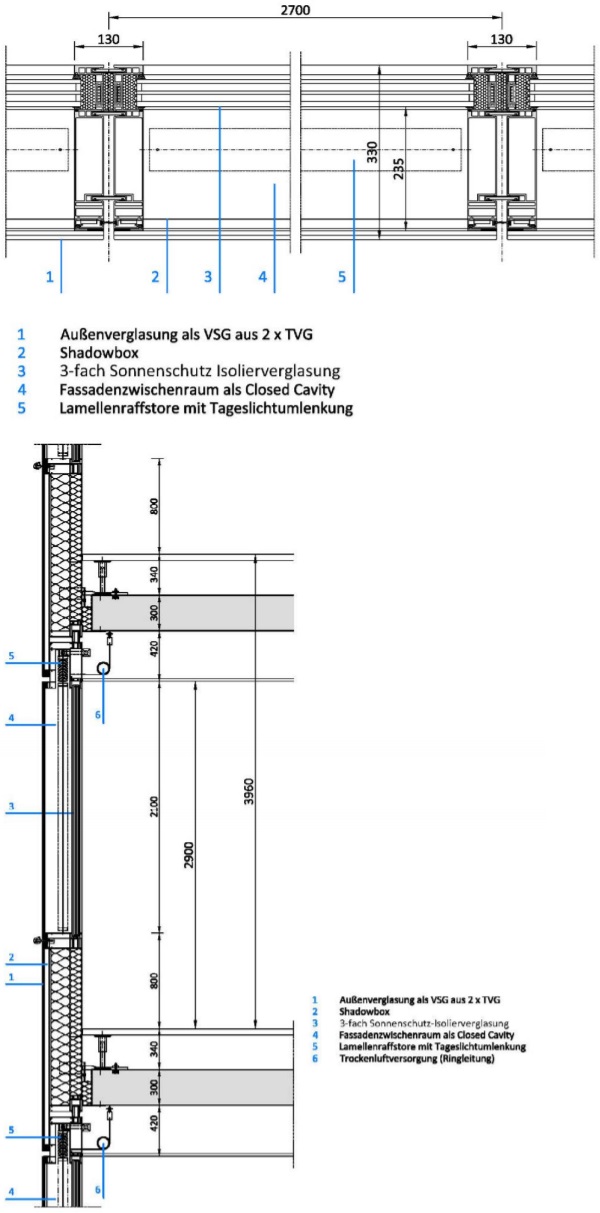
6. The Sun-Protecting lamelles as a key element
In addition to the effect of different SunProtecting lamelles on the daylight situation in an office this test office was used for longterm tests of the sun protection efficiency. Calorimetric testing was also carried out to ensure sustaining g-values.
In the long-term test also, possible influences on the mechanics and the operating characteristics of the sunblinds were tested, following the rules of the ift Directive VE 07 for such tests.
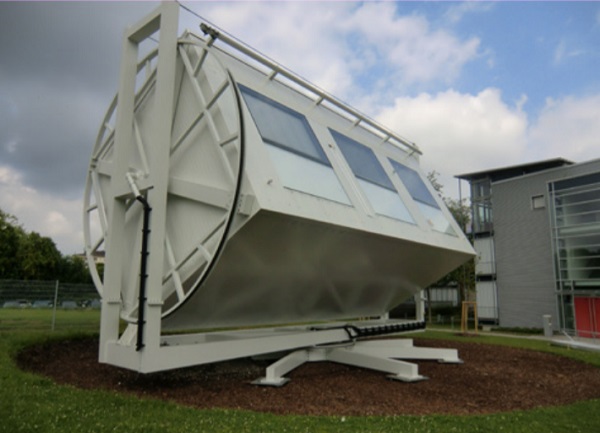
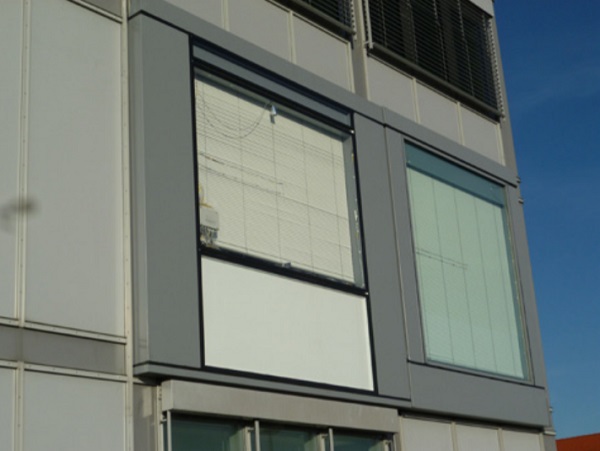
A novel test method for light guiding blinds was reviewed in different positions with respect to their angular accuracy and reproducibility of the test specimen.
This check was made possible by a digitally controlled, photometric device. Figure 13 shows a facade element with built-in side scan window and markers.
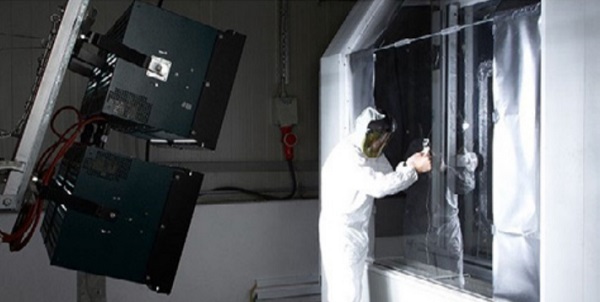
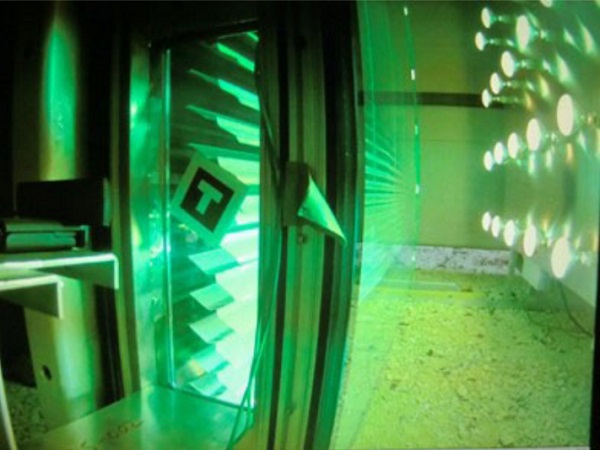
This marker was recorded with a digital camera and analyzed in a computer program, as well as in a graphic translated (Fig. 14, y-axis=angle value, abscissa=time value).
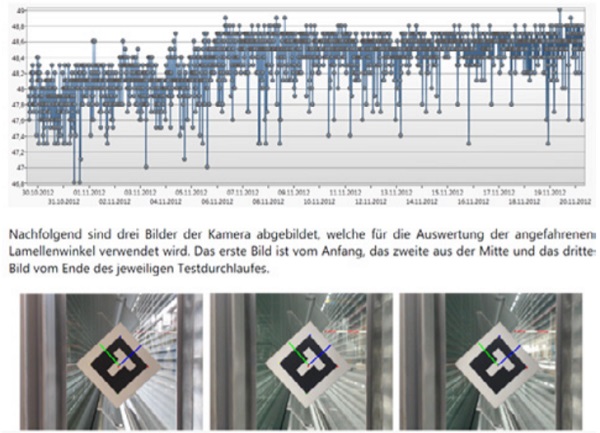
Through these tests important insights for further optimization of the overall system could be made. These were not just about technical improvements to the hanging equipment, but also to explanation in the sun protection control software.
7. Looking to the Future
A return to super-insulated, Closed-FaçadeSystems without manual window ventilation options, but with controlled ventilation and heat recovery features already off and also the reduction of the transparent parts of the façade is the Future a possible way to implement building envelope energy-efficient and yet visually appealing.
Against the background of increasingly scarce energy resources, it is now more important than ever to advance new and promising technologies. The façade type and layout of the new façade of the completed building 1, the currently designed building 2 and the new pRed Center of Roche in Basel, here are good examples of far-sighted and forward-looking buildings.
Much potential lies technically in the use of ever more powerful sun protection types with improved light control properties or creatively in the use of completely new sun protection solutions such as quality sun protection curtains with highly individual look.
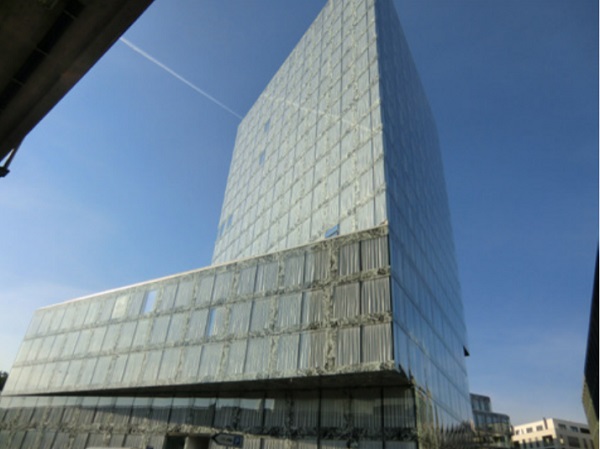
The new and innovative type of façade CCF is in our estimation a step in the right direction and without a doubt, a new key technology in designing Double-Skin-Façades in the 21 Century.
Signboard
Roche Bau 1
Client: F. Hoffmann La-Roche AG / CH-Basel
Architect: Herzog & de Meuron / CH-Basel
Façade Planning: Drees & Sommer / CH-Basel
Façade builder: Gartner / D-Gundelfingen
Roche Rotkreuz
Client: Roche Diagnostics AG / CH-Rotkreuz
Architect: Burkhardt + Partner AG / CH-Basel
Façade builder: Gartner / D-Gundelfingen
Power Tower Linz
Client: Energie AG Upper Austria / A-Linz
Architect Planning Design: Weber & Hofer AG / CH-Zurich
Architect Design: Prof. Kaufmann & Partner / A-Linz
Façade builder: GIG GmbH / A-Puchheim
Richti area Wallisellenstrasse
Client: Allreal Group
Architect Design: Wiel Arets Architects / Maastricht – Amsterdam – Zurich
Façade builder: Gartner / D-Gundelfingen