First presented at GPD 2017
Abstract:
Today’s architectural demand for transparency has been developed to attain maximum daylight saturation which is aimed to improve the well-being of users and maximise interaction with the outside. However, transparency also needs to be combined with the requirements of moderating heat gains (achieving low g-value). This becomes a challenge with current available passive glass coating solutions and the increasingly strict regulatory restrictions that are aimed at limiting window sizes.
In this paper, 20 Farringdon Street, a London based project is the case study that demonstrates how a high transparency façade can be realised by utilising solar control and thermal control glass coatings in combination with optimised frit as part of a single insulated glass unit. This has been designed to increase occupant comfort in the perimeter zone of the building.
The glazing solution has the additional benefit of fulfilling the project requirement to reduce the overall energy usage of the building. A further stipulation on this façade has also been the requirement for blast resilience, which has added complexity to the façade design, and has created an additional restraint to the design process. This paper will demonstrate how it is possible to combine complex coatings with frit and containment laminates to arrive at a fully glazed building envelope that will meet today’s architectural demands.
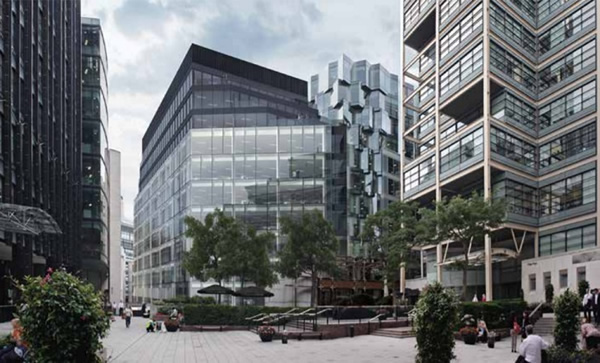
1. Introduction:
20 Farringdon Street is a new 11 storey steel frame building, which incorporates office accommodation on eleven upper floors and a Public House on the ground floor. The building is in the City of London, on the east side of Farringdon Street, approximately 500m north of the River Thames (Figure 1.1). The lead architects of the project are Denton Corker Marshall (DCM) working with Mott MacDonald as the façade consultants and Waterman Building Services (WBS). The glass suppliers for the project are Guardian Glass and Interpane.
The proposed façade is predominantly floor to ceiling curtain wall glazing that wraps around the three sides of the building, creating a light, bright desirable, contemporary office environment and appearance to the scheme (Figure 1.2 and 1.3). The ground and upper 3 floors are set back from the main façade line and benefit from the addition of terraces to east and west (Figure 1.4). The architectural intent for levels 9 – 11 to have a different visual appearance from main levels 2-8, therefore the dark grey upper floors appear chiselled from a single monolithic block.
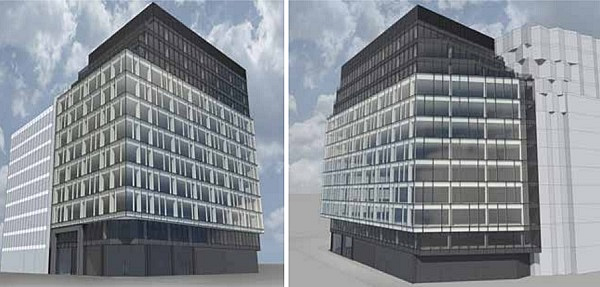
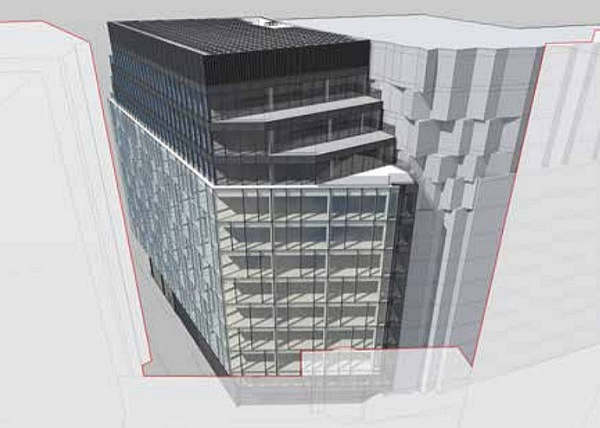
2. Glass Build-up
The proposed systems for the case study building all feature laminate glazing on at least one leaf (Figure 2.1). This option provides better blast-resistance than Anti-Shatter Film (ASF) and Bomb Blast Net Curtains (BBNC)1 , subject to suitable frame fixing into the adjacent structure (Figure 2.2).
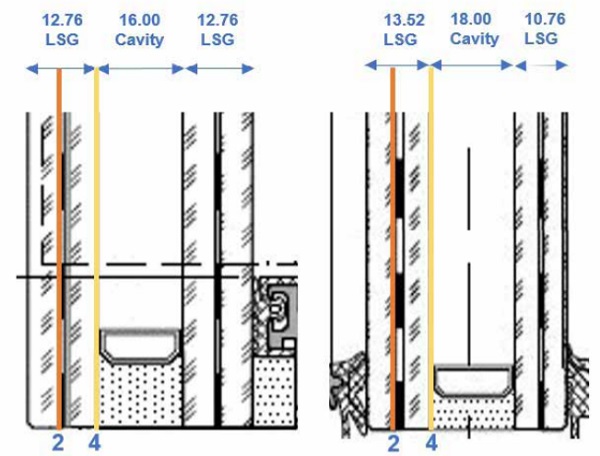
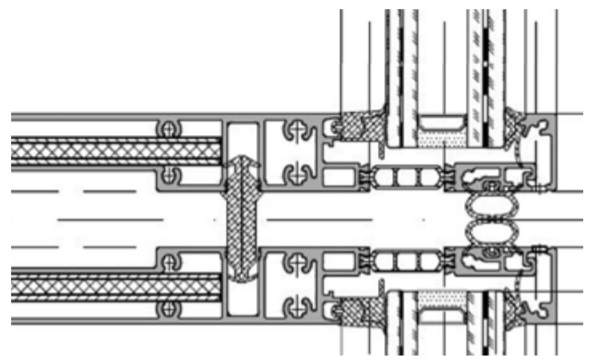
3. Solar Performance Requirements
High quality daylight levels are required for contemporary office accommodation in order to create a pleasant visual environment leading to a feeling of wellbeing. However, the visible light transmission must be balanced against solar heat gain.
A façade that has a high percentage of glazing requires careful consideration to achieve the correct balance regarding glass performance.
Control of the solar heat gain and daylight glare control need to be strongly considered. The project required g-value for the façade was determined by the building services engineer, this was in line with British Council for Offices (BCO) specification 2014 . BCO requirements for daylighting stipulate a daylight factor (DF) between 2% and 5%.
The stipulated façade g-value (Table 3.1) was 0.15. For levels 02-08 which are fully glazed without a spandrel, the resultant g-value of the glass is 0.15 also. Levels 09-11 include an insulated spandrel panel; therefore, the resultant g-value of the glass is 0.20.
It is needed to select glass that achieves the required g-value and still provide a sufficient level of light through the façade (light transmission – VLT). This is known as a ‘high selectivity glass (VLT/g-value). The graph below (Figure 3.1) shows the relationship between g-value and light transmittance of the glass types currently available on the market (colour dots). When the glass g-value is lowered, the amount of visible light transmitted is also lowered. It can be seen that for a certain g-value, several glasses may be available with varying light transmissions and vice versa.
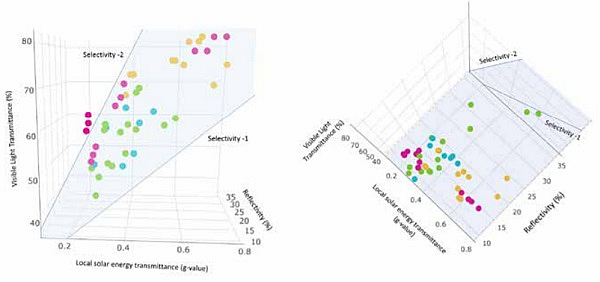
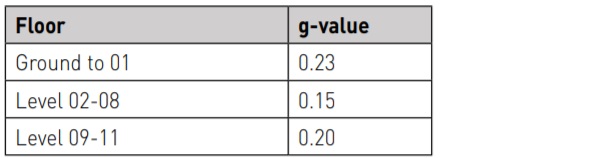
High Selectivity Glass (VLT/g-value).
To achieve such a low g-value whilst still allowing a relatively large percentage of VLT, high selectivity glasses were considered. It is clear that achieveing g-value of 0.15 with just the glass coating/tint would result in a light transmission of approximately 25% or lower (Figure 3.1).
This is considered too dark for an office environment and would greatly reduce the occupants connection with the outside.
An approach was to select a high selectivity glass that allowed approximately 50% VLT. With a selectivity of at least 2, this would result in a g-value of appro 0.25. The addition of a ceramic frit to the glass would be investigated to lower the g-value to 0.15, and, although anticipated frit density would be high, its position on the glass could be controlled to allow the vison area of the glass to remain frit free and so still achieve clear views and relatively high VLT.
4. Glass Coatings
High performing double/triple silver glass coatings were investigated from several of the major glass suppliers in the UK. The three glass coatings further investigated were: Guardian SNx 50/233, Interpane Ipasol 50/274 and Pilkington Suncool 50/255 (Table 4.1).
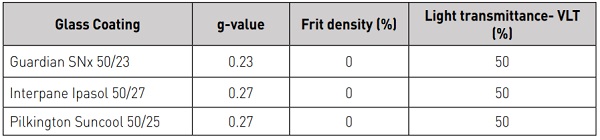
Ceramic Frit
Ceramic frit is a relatively simple and economic solution to lowering the g-value, it has the advantage that the density can be varied throughout a panel so that vision areas can remain relatively clear.
Frit colour concerns both architecture and performance. A white frit becomes a much more noticeable feature of the façade and can define the architecture. Whereas a grey frit is a more subtle addition but can also dull the appearance of a glazed façade.
From a performance perspective, a grey frit has increased performance over a white frit in regards to reducing the solar heat gain as the darker frit absorbs a higher proportion of the heat and radiates it outward.
The surface position of the frit within the IGU also affects both aesthetic and performance; for the fritting to be most effective in reducing solar gains, it should be located on the outer leaf of the double-glazed unit.
The table below (Table 4.2) shows the density of white frit and grey frit required to achieve the required g-value of 0.15 from the three glass suppliers.
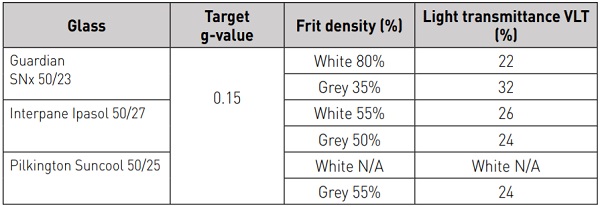
5. Manufacturer’s Limitations
Achieving U-value
With the application of 35% ceramic frit to the Guardian glass, the 0.15 g-value requirement can be achieved. The Interpane and Pilkington glass have much larger frit requirement at 50% to achieve the 0.15 g-value but they do not meet the light transmittance requirement of minimum 32%.
Coating Position
The fritting and solar control coating are most effective on the outer leaf. Pilkington and Interpane can produce monolithic glass with both the frit and solar control coating on the same surface (surface #2). However, Guardian do not recommend applying frit to the same surface as their SNx 50/23 coating; they would require a laminated construction to the outer leaf with the fritting on surface #2 and their triple silver solar coating on surface #4.
Aesthetic Limitations
The architect required grey silicone in levels 02- 08 which would have given a more monolithic appearance but Guardian Glass could not manufacture grey silicone bonding due to manufacture restrictions.
6. Façade solution options
Due to manufacturing limitations in achieving the required g-value, additional design solutions (Figure 6.1) were explored to lower the percentage of frit on the façade by adding a spandrel into the external pane configuration (Option C and D, Figure 6.1). The study of a spandrel addition (Figure 6.2) showed that, as the solar radiation is no longer being transmitted through the spandrel area, the glass itself did not have to perform to the same level. Therefore, g-value of the façade could be relaxed from 0.15 to 0.20, as the proposed glass is now 80% rather than 100%. As shown in Figure 6.2 by including 20% of spandrel, the white frit could be reduced to a more sensible level and the light transmittance can be increased.
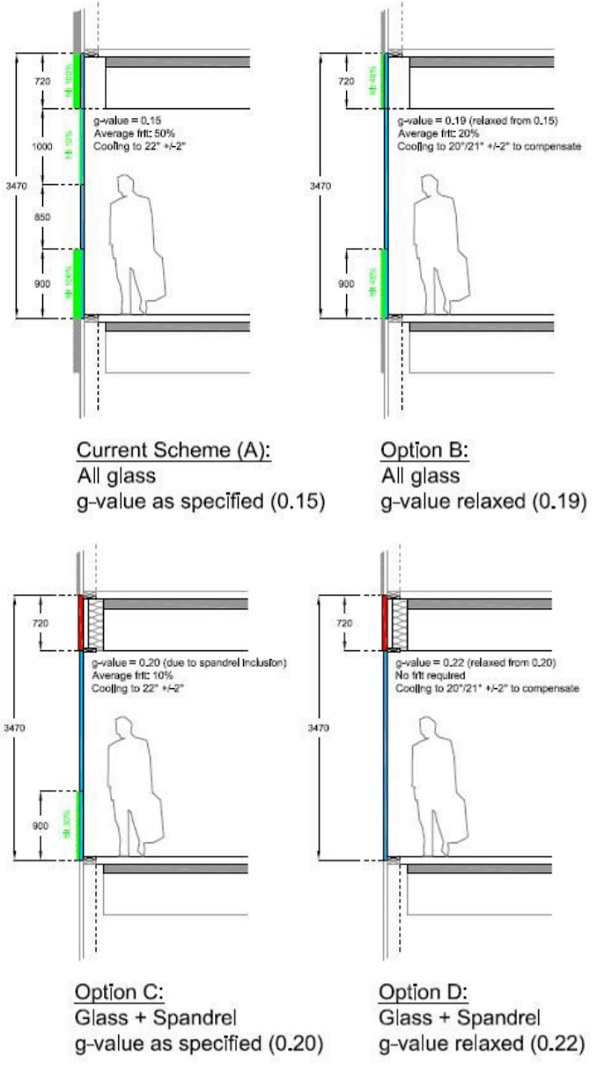
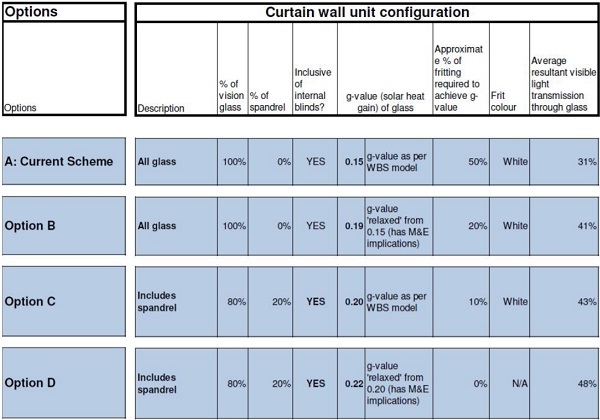
As can be seen below in Figure 6.3, the pane options including spandrel have a better thermal performance to Part-L requirement, contribute to the targeted BREEAM Excellent rating and improve the base acoustics performance scheme.
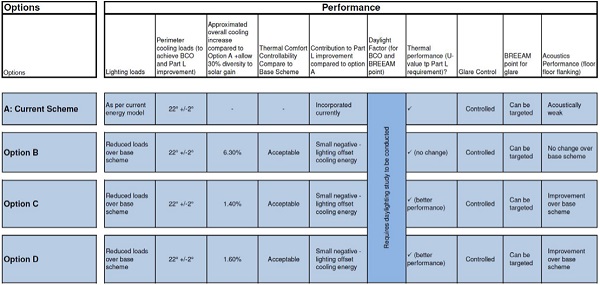
7. Conclusion / Glass Performance Summary
The decision to include spandrels rather than 100% glass offers better performance on various fronts. Two glass types were selected (Table 7.1) due to their best performance against manufacture limitations. A sensible level of frit was impossible to achieve without the inclusion of a spandrel which lowered the overall g-value target. Guardian’s glass was selected for the black frit area of the façade only due to its low g-value. The white frit area of the façade was appointed to Interpane.
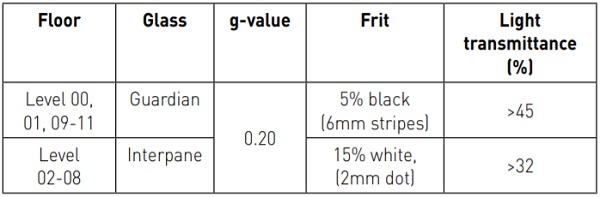
Final Frit pattern selection
Various studies were undertaken by the Architect and these were tested to understand which were considered the most lettable. The final selection for frit pattern on Level 00, 01, 09-11 was Black, 6mm vertical stripes with 6mm spacing at low level with 5% coverage (Figure 7.1). On Levels 02-08 white 2mm dots frit with 15% coverage was selected as the most appropriate (Figure 7.2).
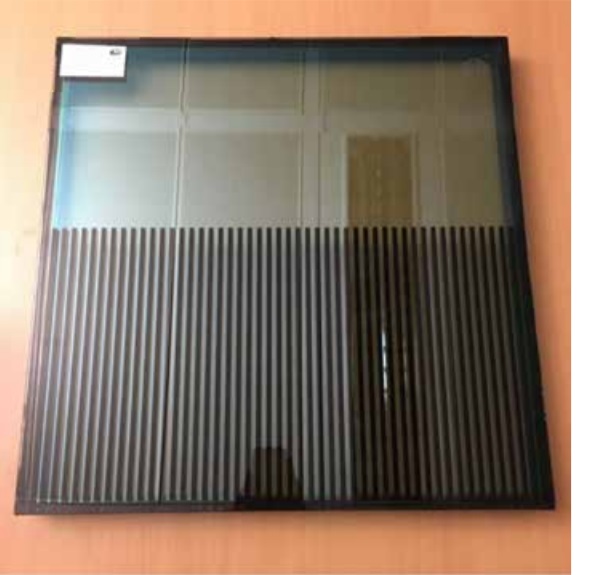
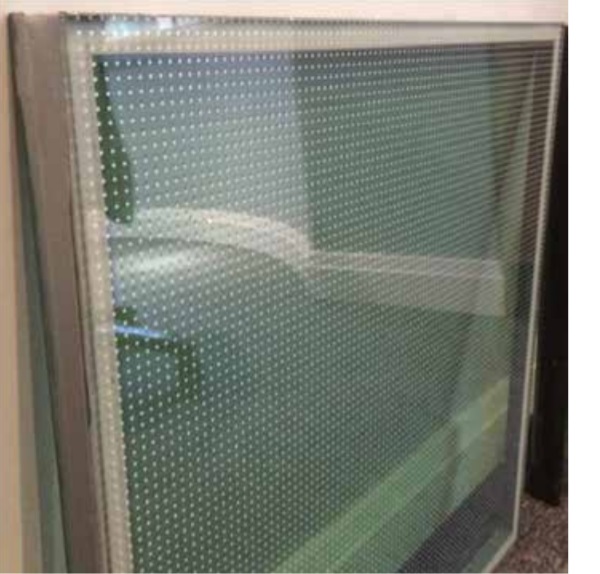
Acknowledgements:
Special thanks to Clive Atkinson for his and support in writing this paper and to the architects for their collaboration.
References:
[1] CPNI
[2] BCO Guide to Specification 2014
[3] Guardian Glass, Sunguard Extra Selective SNX 50/23 Datsheet
[4] Interpane, Ipasol 50/27 Datasheet
[5] Pilkington, Suncool 50/25 Datasheet