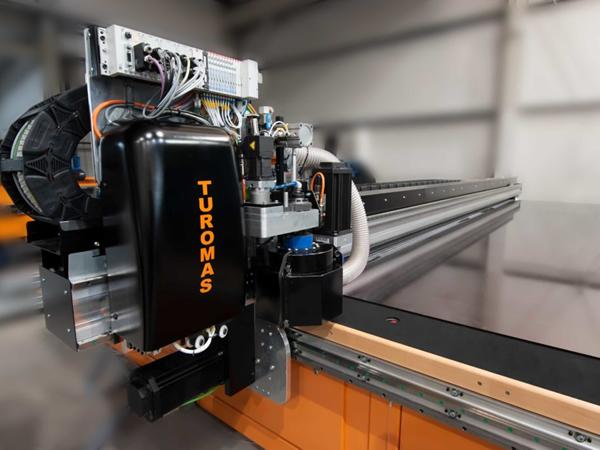
Date: 12 May 2021
The RUBI 406VA innovative design meets the loading, cutting and automatic unloading needs of the most demanding customers, ensuring maximum productivity and automation in the smallest possible space.
Since the first automatic glass loading system was launched in the 1980s, TUROMAS has continued to work on the improvement and development of this technology. Knowledge and experience that have made it possible for TUROMAS to be pioneers today in launching the solution for loading 6m glass from the cutting table itself.
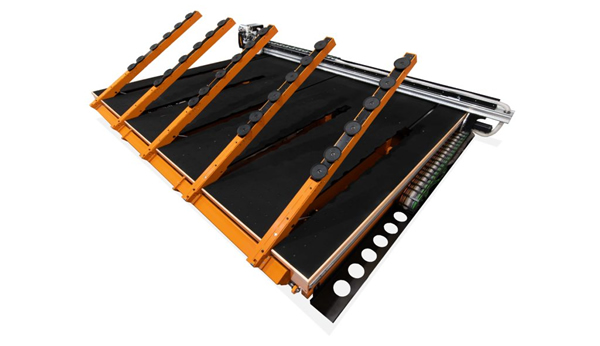
Absolute return with minimum investment.
The lack of sufficient infrastructure is a handicap for medium-sized glass processors, which is why it is essential to make the best possible use of resources, achieving the greatest possible coordination and efficiency in the plant.
In the new RUBI 406VA model, the automatic loader is integrated into the structure of the cutting table itself, optimising the loading, positioning, cutting and unloading or cutting processes in just 35 m2.
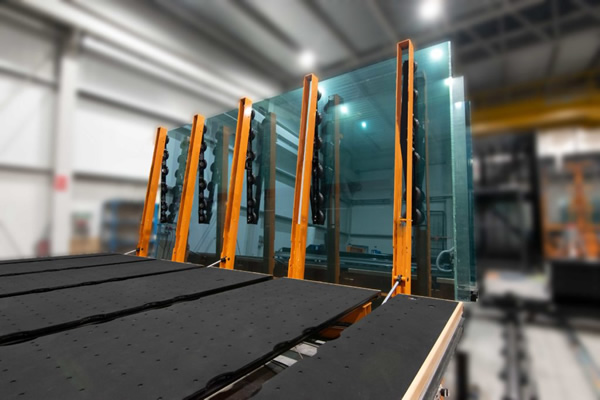
Solving the four processes in the same space means extensive economic and logistical benefits for the customer. On the one hand, economic savings by not having to assume the cost of purchasing and installing an automatic loader. And, on the other hand, optimisation of the space in the plant by dispensing with the need for additional equipment to load the glass.
New loading system: robustness, safety and speed.
The loading arms have been redesigned and upgraded to incorporate a new instantaneous separation system that puts an end to the problems associated with the glass sheet separation process.
With this new design, the speed and loading time are significantly improved, reducing loading time to a minimum without compromising safety in any way. The entire feeding cycle is carried out in a progressive and smooth manner, eliminating breakage due to collisions and the possibility of accidents.
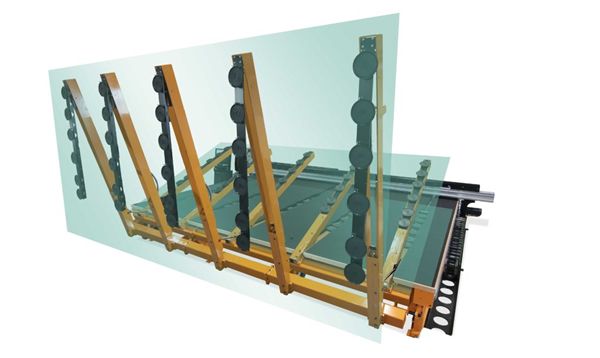
In addition to the revolutionary loading system, the design of the RUBI 406VA has been specially reinforced to make it possible to cut glass of any thickness, to strip Low-E, TPF and EASYPRO® glass and to label every single piece, guaranteeing high performance and cutting quality.
Main features
Among the main features that set it apart is the 4tool cutting head system that guarantees a perfect cut for any thickness, including 25 millimetre thickness. This system incorporates four individual, automatically selectable cutting tools, each with its own cutting wheel, independent lubrication system and pressure cylinder specifically dimensioned for its cutting range.
The first tool is intended for cutting glass from 1.8 millimetres to 2 millimetres thick. The second and third tools are used for glass from 2 millimetres to 12 millimetres, which are the most common thicknesses. The fourth tool uses a larger diameter wheel to cut glass from 12 millimetres, 15 millimetres, 19 millimetres and 25 millimetres.
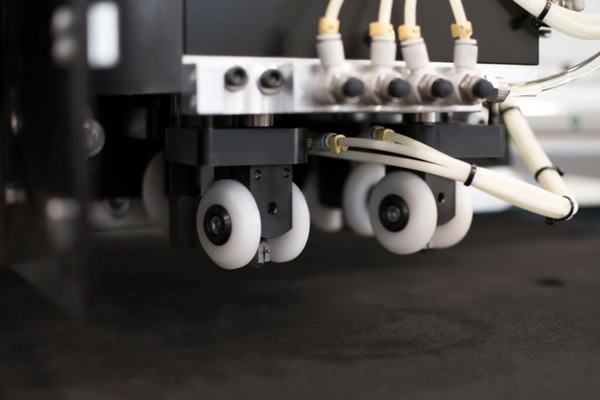
Another aspect that guarantees reliability and precision in each of its movements is the gantry transmission system. The RUBI406VA model has two motors, one on each side of the cutting bridge. These are connected directly to the pinion and the pinion to the rack, providing greater power and facilitating the movement of the bridge along the side guides.
In addition, it uses an oversized, self-lubricating, trapezoidal double-guided transmission system that prevents contact losses, withstands stress better and increases precision and resistance to inertia.
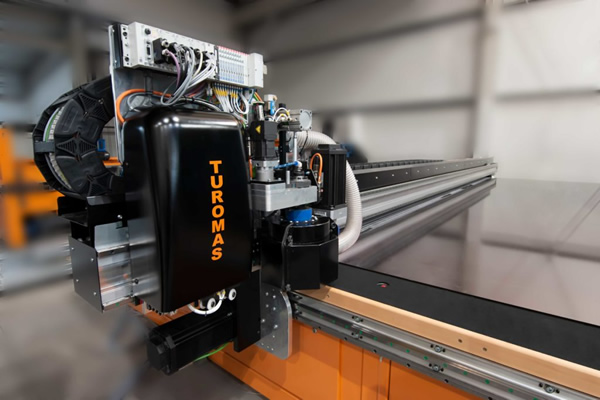
The cutting bridge has been specially designed by the Turomas engineering team and made from extruded aluminium, a lightweight material that allows greater speed and acceleration to be achieved. All its components, from the profile through the guides to the slides, are oversized to increase the useful life and support the weight of the tool, as well as the accelerations and inertias derived from the movement.
It has a two parallel guideways system with a linear accuracy of hundredths of a degree that promotes smooth movement, reduces noise, increases durability and enables the motors to move larger loads.
Optional Features
As an option, the RUBI 406VA model incorporates an innovative, high-performance, self-calibrating stripping system for Low-E glass, Low-E glass with plastic protective coating (TPF) and EASYPRO®.
This system is able to remove the protective coating from the glass in a single pass, improving cycle time and reducing grinding wheel wear. In addition, the new development incorporates an advanced vacuum technique that eliminates any residue resulting from the decoating process.
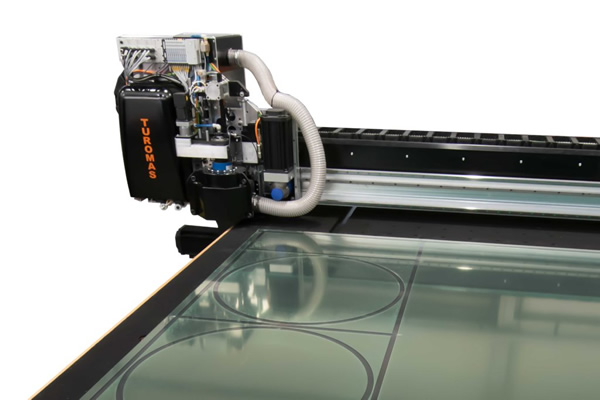
In addition to the advanced decoating system, TUROMAS complements the RUBI 406VA line with an automatic labelling system of both glass parts and scraps. It is integrated into the cutting bridge and moves with the tool, resulting in high printing and application speeds.
The labelling system is extremely robust, making it immune to inertia caused by machine movement and acceleration. The labelling process can be carried out by contact or by blowing, so that coconut dust is completely removed and the adhesion of the label is improved.
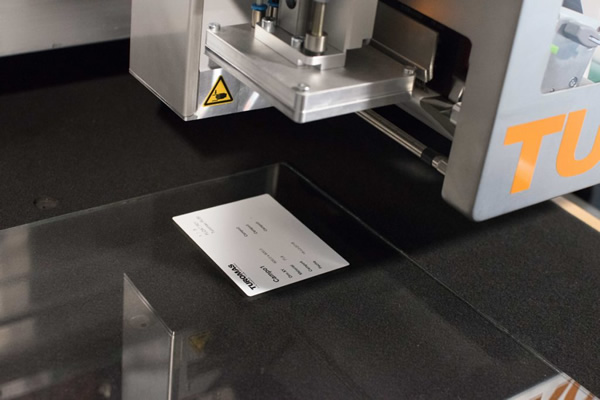
RUBI 406VA in combination with SR - Rack Shuttle Warehouses
The new model in combination with the Rack-Shuttle SR storage systems forms a production system capable of meeting the needs of the most demanding processor and, at the same time, adapting to virtually any space and type of glass.
This type of machinery has established itself on the market as the new intelligent storage system thanks to its flexibility, modularity and production rate.
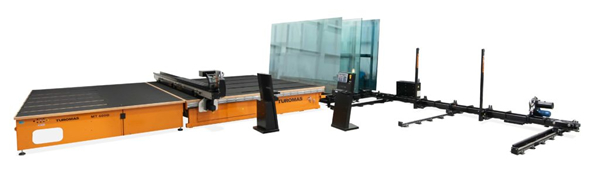
The RUBI 406VA, on the other hand, loads the glass sheets directly from the warehouse rack, optimising space and allowing the area not used by the automatic loader to be used to increase the storage capacity of the system.
The combination of the two machines offers a simple and cost-effective alternative for autonomously storing, loading and cutting glass with up to 300% higher throughput.
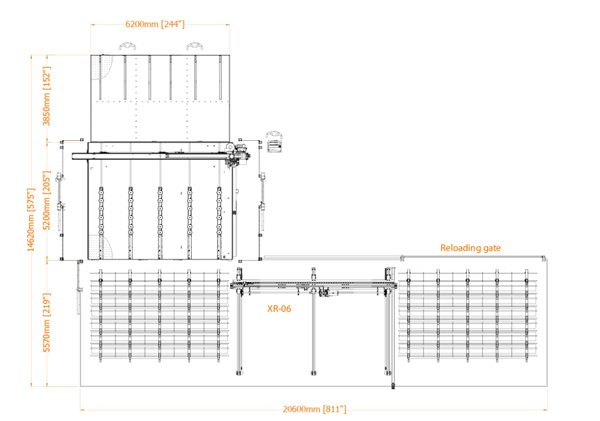
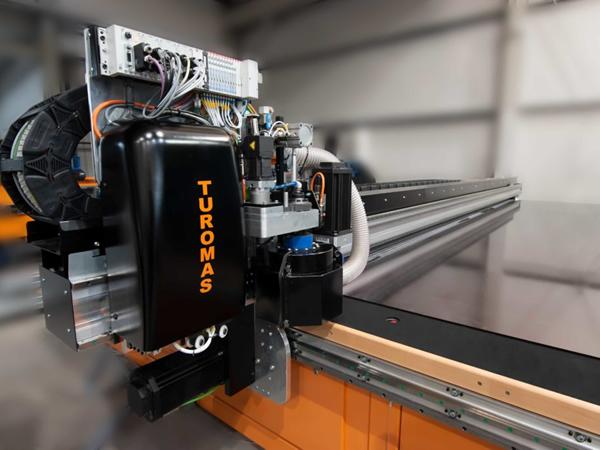

Add new comment