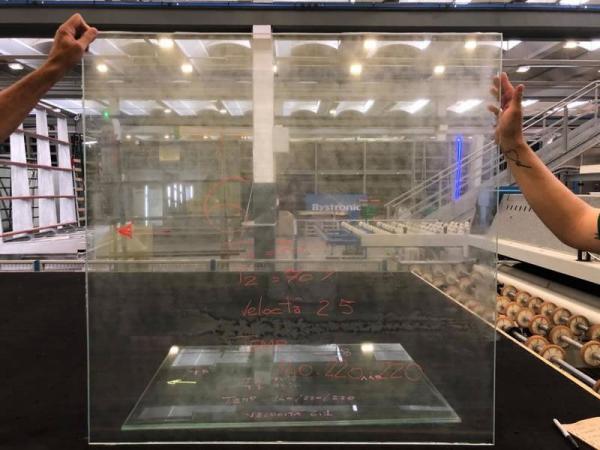
Date: 10 July 2020
Suddenly and unexpectedly, supply chains, business workflows and production processes around the world were interrupted by the coronavirus lockdown. Naturally, Kuraray's customers were also affected. For one customer in the glass industry the lockdown threatened to interrupt production plans because the pandemic meant it was no longer possible to hold important on-site training sessions. To avoid that, the Trosifol team quickly switched to a flexible online training concept and remote support. The process was successful and is now being fine-tuned for future use.
Kuraray always helps customers with the installation and start-up of new production lines by providing on-site training and practical support. However, the Covid-19 pandemic abruptly interrupted this tried-and-tested process: overnight, on-site visits became impossible. That confronted one of Kuraray's customers with a fundamental problem. The glass producer in Bologna, Italy, had recently invested in a new production line to broaden its range of architectural glass to include laminated safety glass with PVB and SentryGlas® ionoplast interlayers from Trosifol. “The production line was installed and ready to go. Normally, we would have gone along to help the customer with the initial lamination tests and train the production operatives. However, the lockdown changed all that,” explains Alejandro de la Muela, Senior Consultant Technical Services at Kuraray. It looked as though the customer would not be able to start production on the new line.
Online training meant production could be ramped up quickly
Customer satisfaction has very high priority for Kuraray. Alejandro de la Muela and his team therefore considered how they could provide support despite social distancing and lockdown restrictions. Within a very short time, they produced an online training program. To enhance learning, the team at Technical Services spread the complex content over three online sessions.They also provided a list of glass samples and tools to guide the production workers step by step through the lamination tests.
In collaboration with the customer’s engineers, the team came up with quick fixes for the hardware needed for the online training and for remote support during the test runs. “In our offices at Kuraray, we had computers with two screens so we could display both the presentation being shown to the customer and additional comments and information,” explains de la Muela. “We also used a sketchbook with a mobile phone fixed over it so we could share notes and information in real time.” Thanks to this rudimentary set-up, ideas could be shared effectively.
All customized parameters on the production line were entered in a shared Excel spreadsheet. The file also contained an image of the pre-laminate so this completely new document for test runs can be used to deal with questions in the future. (To produce the pre-laminate, air is pressed out of the glass/interlayer composite before the final laminate is produced in the autoclave.)
Kuraray's customer in Italy used iPads for the training sessions so employees could move around freely and show the Trosifol technicians the various stages in the test runs. A laptop in the laminating room ensured smooth communication and transmission of the images. The set-up also included a temperature sensor and a UV lamp for validation of the SentryGlas®.
Remote support to be extended
“Nothing beats meeting up personally,” says Alejandro de la Muela. Nevertheless, the flexible hands-on approach meant that his team could provide quick and uncomplicated support for this customer in Italy. Thanks to the resourceful switch to online training, the whole process from the start of training to the first complete production run and the official production start took just two weeks. As a result, it has been decided to establish this remote concept for future use. Additional requirements such as special audio-visual hardware and other equipment have already been defined to drive forward and optimize the concept for online support in the future. By combining online and on-site training and support, Trosifol can lift service for production to a new level both for this Italian glass manufacturer and for other customers around the world.
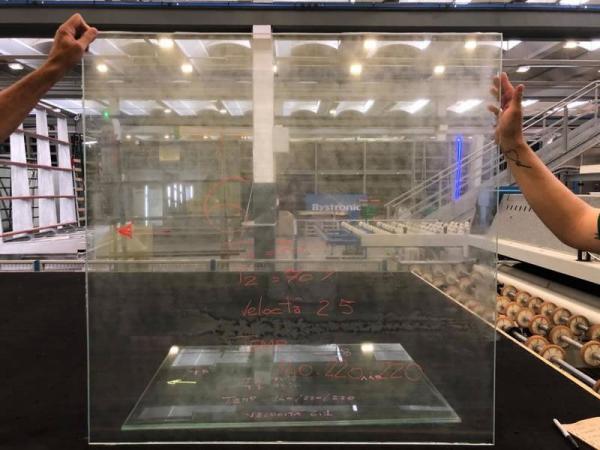

Add new comment