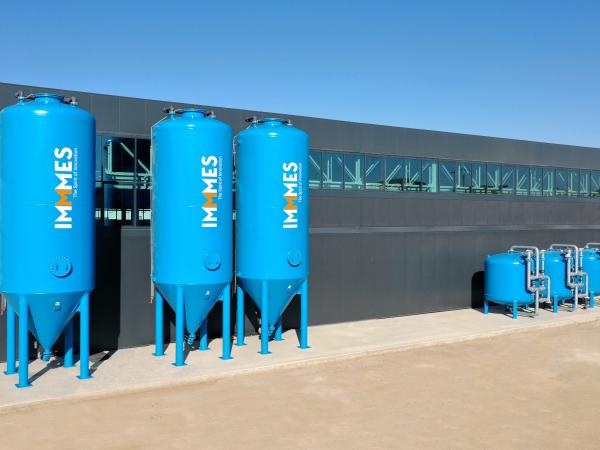
Date: 13 December 2022
The working process
The plants that we are talking about in this section are dedicated to the typical production processes of the glass factory.
A feature of this environment is the use of a great amount of water, which is necessary in order to cool the grinding machines. After the glass treatment the water results contaminated, whether it is contained in the tanks under the machines or in one central tank.
These particles normally measure an average which goes from 5 to 85 microns (obviously with exception to bigger residual parts which are stopped by former filters) and their concentration can reach 8/900 mg/lt (we rarely found plants which used to reuse water with particles bigger than 1000 mg/lt). These particles give water the typical coloration “milk” which is not suitable to the cooling process.
In absence of a suitable plant for the elimination of particles, it normally happens that chemical additives are used in order to aggregate the single particles and make them heavier. They can then easily sediment on the bottom of the tank and leave on the top clear water for the following reuse.
The presence in water of cooling oils (which is actually not very widespread) is a consequence of the use of water with a high density of particles, which force the use of cooling oils to overcome the functional lacks of the dirty water.
Risk of sediment and work with dirty water
The particles of glass normally thicken and sediment even if they are submerged in water.
They sediment and thicken along the pipes, in the tanks, injectors and in the structure of the machines, creating a real crust like cement which is expensive and hard to remove and requires the use of pneumatic drills and many working hours.
The partial obstruction of the pipes can lead to the waste of the water necessary in the working process and for the correct operation of the machines.
The most important problems are the ones caused by dirty water in the glass working process. The micro particles will eventually remain attached on the glass surface creating defectiveness in the final result. Today, thanks to the diffusion of quality controls made by scanner machines, these defectiveness can easily be found and it can bring to the waste of entire batches of glass.
Finally, the presence of chemical additives in water, in addition to their expensive cost, highly damages the equipment because of the water acidity and the consequent corrosion of several parts of the working machines.
Problems with glass particles disposal
The topic of the disposal of contaminated water or sludge with glass particles is one of the most important points in the working process, due to its expensive costs and the environmental risk that it involves.
Even in this case the behavior of the company changes according to their cleaning water plant.
In absence of a real plant, the cooling water which cannot be reused anymore is stored for the disposal that will then be made by specialized companies with apposite cistern trucks.
In this case, the presence in the fabrics of CNC machines which requires clean water to be operative complicates the process. The solution can be to supply them with water coming from the public net, which though leads to the increase of the circulation of contaminated water and the consequent difficulty with its disposal.
Different purification plants also exist. They keep the water of the working processes clean or even limpid and manage to extract the glass particles from the water, dehydrate them, compact them and store them in big-bags where they will directly be collected by normal trucks in a cheaper way and for bigger amounts.
These systems normally create closed circuits of water where they can operate with a purification capacity higher than the total pollution capacity of all working machines.
In this way they can provide limpid water to every machine, included the CNC, so that every possible need of new water is avoided (except the restoration due to evaporation).
WATER TREATMENT SYSTEMS AVAILABLE IN THE MARKET
The need to keep the cooling water as clean as possible, so as the need to keep building, machines, tanks and pipes clean and efficient represents one of the constant objectives of the entrepreneurs and an important task in the research and development of new technologies for specialized companies of this branch.
First of all, the basic forms of purification resort to natural physical-dynamic processes. The sludge and every kind of heavy material sediment on the bottom due to the force of gravity and leave in the top part of the tanks clean water. This water is resent to the working machines through specific pumps.
This principle and this process represent the starting point in the cleaning water sector. Beside this, technology has been applied and the limits of volume and quality can be easily imagined.
The natural sedimentation process which typically happen in one or more tanks connected with each other with overflowing can be accelerated adding to the contaminated water some chemical additions – we want to specify that we DO NOT use this technique in any of the plants of IMMMES – even if we described the caused cons above. (you can see an example scheme in the image nr.1)
The evolution of these basic systems is represented by the application of equipment, which can be more or less automatic, for the extraction of the sludge which is expelled from the bottom of the machines. This equipment is normally composed of hollow plates with filter function in which the contaminated water is inserted under high pressure. They are called FILTER PRESS (see our Line DGS). They accelerate the extraction of glass residuals and leave therefore cleaner water in the tanks.
It is interesting at this point how it is possible to have a reserve of clean water which can be used to power the CNC machines. In fact, the water which comes from the pressing process of the sludge in the filter press results particularly clean and with few solid particles.
This clean water, which is stored in a specific tank, can feed the CNC machines avoiding the entry of new water from the public net in the system.
In image nr. 2 you can see an example of the evolution of a mini-plant.
One must say that the plants dedicated to the extraction of sludge can be applied also to a single working machine, creating a kind of mini-recirculation. Normally they are available in many different sizes, according to the necessity of the fabric for what concerns the volume of treated water and the purification capacity (see our Line ID).
A qualitative leap is obtained leaving these schemes and finding out the world of real high tech plants. Research and lab tests, innovative technologies, international licenses, combination of many working elements, energy save and eco friendly, water parameters constantly under control, these are the words which govern the most advanced projects.
It becomes then redundant (even if it is actually not) to mention the result of water in terms of quality. Extra limpid water, so as the bottle water, particles with a dimension under 10 microns, residuals quantity 10-12 mg/lt and no volume limits, from 10 up to 250 liters/hour. These are the innovations reached up until now.
We started from the result in order to present our most important product, the DTP , already present in many Italian and international companies.
There are no more first and second class waters, no more water volumes differentiated between pumps capacity and filter capacity, everything enters in the system and exit clean.
In the image nr. 3 you can see the synthetic scheme of what is the best in terms of technology and results.
For a complete and correct information of what you can obtain with this kind of plants it is necessary to make a list, as we are used to do with the features of a new car model. You can find all information, details and technical schemes inside the product DTP.
We thank you for reading and we invite you to open the specific sections of our products, which include the reverse OSMOSIS plants and DEMINERALIZATION through the use of cationic and anionic resins; these plants are destined to the washing mashines.
In order to complete our offer we also want to present a special machine which cleans water contaminated by paints, which are normally used in the silk-screen printing: it is called ANTAEONE.
Everything is rigorously 100% Made in IMMMES.
It is not bad, if we consider where we started and the evolution that this sector had, thanks to the growing environmental awareness, for the improvement of the working environment, for the economical competitiveness of the companies and for the quality in the glass production.
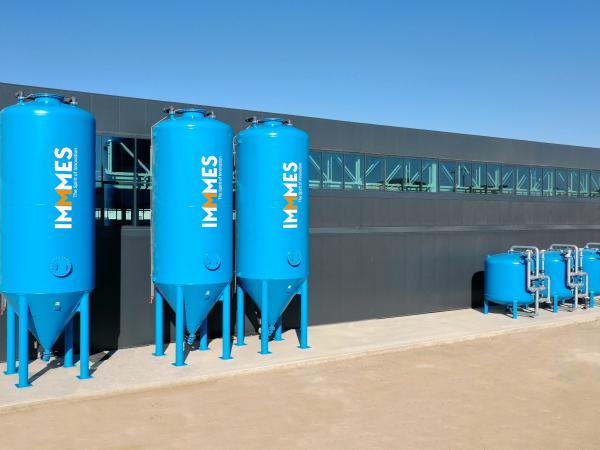

Add new comment