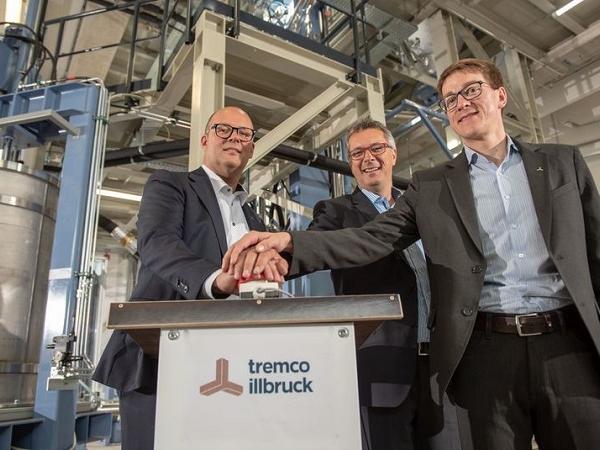
Date: 23 April 2018
It is the most cutting-edge facility of its kind and has been designed and made specifically for this plant. With a high degree of automation, it will double production and provide even higher, even more consistent quality. And tremco illbruck customers can customise their products with the specialists in application technology.
With the investment of 6.5 million euros – the largest single investment by RPM in Europe – tremco illbruck concludes the second phase in the expansion of its German sites. It was only in December that a new facility for impregnated sealing tapes went online at the Bodenwöhr site in the Upper Palatinate.
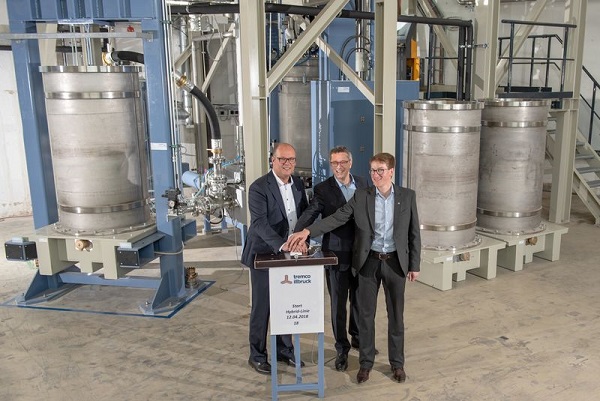
tremco illbruck is a leading manufacturer of adhesives and sealants using ground-breaking hybrid technology. The company launched the first product back in 2008. Now, a large proportion of its product range, which consists of adhesives and sealants, is based on this technology.
It allows products to be manufactured for the construction sector without using any isocyanates or solvents, meaning they no longer pose a health risk. Added to which, the technology also opens up the possibility of a vast number of completely new applications. These include powerful adhesive bonding which will make screw connections redundant and zero-emission, flexible sealing.
‘The increasing demand for our system solutions and our ambitious objectives as a company require our plants to be continuously modernised and new capacities to be developed’ said Reiner Eisenhut, CEO & Managing Director of tremco illbruck Group GmbH, in reference to the company’s substantial investments.
‘By expanding our German production sites in the “Bavarian chemicals triangle”, we are creating the ideal conditions for the growth we are striving for in the next few years.’
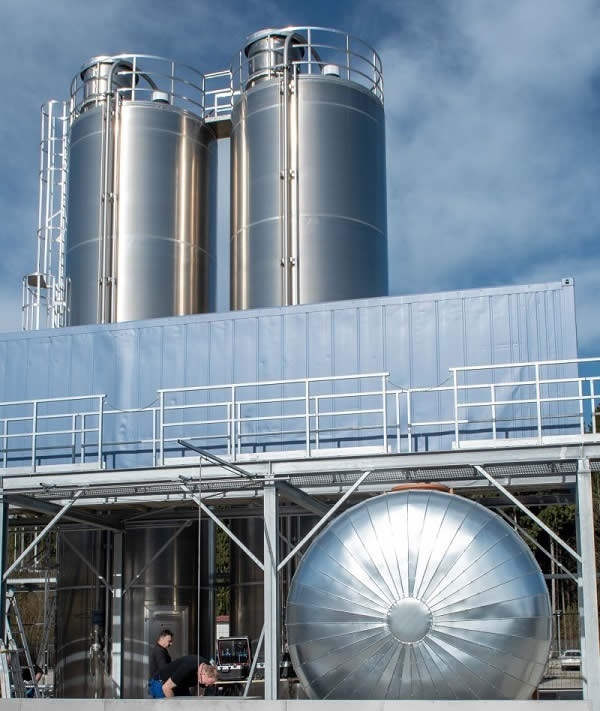
Faster, better, more flexible
Up until this point, there were four mixing plants in operation at the technological centre for adhesives and sealants in Traunreut. The investment in the new facility marks the transition to further improved quality, faster production and greater product diversity.
The production process is fundamentally different here. Instead of having to charge the plant from scratch every time, the new facility now automatically produces a variety of different basic recipes. These are then given their final properties using catalysts and pigments.
This means it is also possible to modify the recipes precisely for specific client requirements. There are no fewer than 22 employees doing research into the future of sealants and adhesives in the development department at Traunreut.
The new system requires considerably less time for a complete production cycle than the 180 to 240 minutes that used to be the norm. That means production can be doubled. Incidentally, the mixing plant only needs to be fully cleaned once a year; that saves a great deal of time and protects the environment.
Reiner Eisenhut goes on: ‘By taking this step, we are proving once again that we are synonymous with innovative and powerful technology and solution-based and service-orientated product development and system solutions.’
Automated operation ensures perfect products
‘You can think of producing sealants and adhesives as a bit like baking a cake,’ explains Sebastian Patzig, a doctor of chemistry and technical lead and head of quality assurance in Traunreut. And just as with a freshly baked cake, the secret to excellent results lies in the recipe and in how it is made.
In other words, you need to mix the finest ingredients in exactly the right proportions, at the right time, at the right temperature, with the right amount of moisture and at the right speed. ‘The most important thing is to make sure that no moisture from the air finds its way into the paste,’ Patzig stresses.
This is the only way to prevent undesirable reactions such as premature curing beginning. All the media is supplied completely automatically: electricity, compressed air, nitrogen, coolant. As a result, production is independent and consistently high quality of the products and punctual delivery to the customer are both guaranteed.
Exceptionally well positioned for the future
One existing warehouse was completely converted for the new mixing facility. The ground was upgraded in situ and the roof was raised by four metres to a height of 12 m. In the area outside, foundations were laid for up to five large silos and four tanks. Until now there have been two containers standing there, each holding 90 m³, and a 40-m³ tank.
The warehouse, which is around 800 m² in size, is also only about half full with the new facility. tremco illbruck is optimistic about the future: ‘We currently have approval for the production of 10,000 tonnes of adhesives and sealants per year,’ explains Bernd Schürmann, Operations Manager at the Traunreut branch.
‘This expansion means we can double our production volumes. Work is already under way on a design to achieve further optimisations. Step by step, we will use this to move other product groups over to one of the most cutting-edge installation and production facilities.’
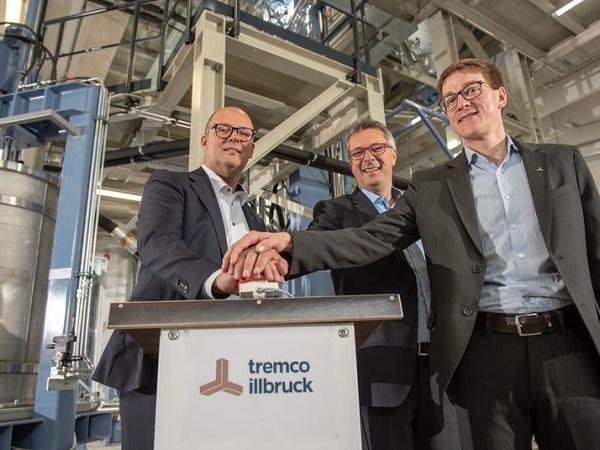

Add new comment