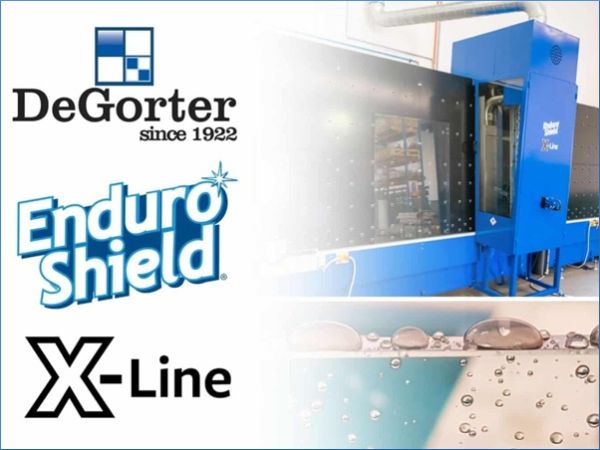
Date: 9 September 2024
This collaboration enhances precision, efficiency, and profitability, providing glass fabricators with industry-leading solutions for streamlined production.
DeGorter Inc. is a fourth-generation, family-owned business that has been at the forefront of glass processing for nearly a century. Specializing in providing advanced equipment and supplies, DeGorter plays a crucial role in supporting glass fabricators with reliable and innovative solutions.
Founded in 1922 by Daniel De Gorter, the company has been a trusted US installation, parts, and service partner for EnduroShield since 2002. DeGorter is also the exclusive glass edging solutions partner in the United States for Italy-based Schiatti Angelo. In addition to representing cutting lines from Macotec and washing solutions by Malnati, both from Italy, DeGorter has also gained a reputation for claveless lamination solutions and a range of decorative and architectural interlayers with partner Hornos Pujol out of Barcelona.
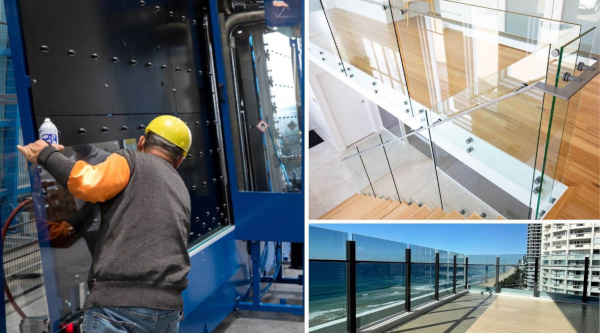
George Rufra
A graduate with a Computer Science Degree specializing in Computer-Aided Design (CAD), George is the quintessence of problem-solving – a trait frequently lauded by his wife and one that dovetails seamlessly with his professional life.
President of Equipment Acquisition Solutions, George’s passion lies in providing support to clients with their glass fabrication and processing requirements. George is committed to creating innovative solutions that not only minimize labor but also elevate productivity and throughput, culminating in greater profitability for his clients.
George started his glass career in 2008 at HMI Glass Solutions, formally Cardinal Shower Doors, as Second Shift Supervisor and quickly worked his way up to Tempering Operations Manager. George grew to oversee three shifts and 200+ employees while shaping the company’s strategic planning. “Due to my background in glass fabrication and processing, I was involved in many different expansion projects in Louisville and assisted in the design of a brand-new plant in Reno,” says George. “We were the largest shower door manufacturer in the US and I researched all things tempering. Every equipment supplier wanted their machinery in our factory. I spoke with everyone to determine what would and would not work. I traveled the world to see all of these different glass processing solutions in action. That allowed me to become a sponge and learn as much as possible while growing my network around the world.”
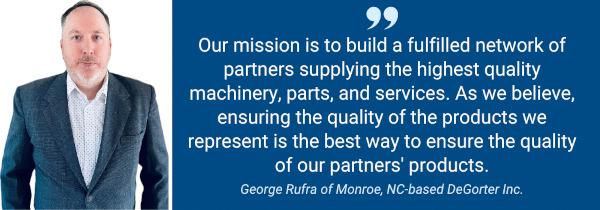
Family Focused
“DeGorter is different to me than other companies,” explains George. “It is a family focused company that values relationships with its employees and its partners. As a previous long-term customer in the glass processing industry, I was able to see how the company operated from the other side. DeGorter was always there to help me, no matter what. I can’t tell you how many times I would reach out for assistance from DeGorter in the middle of the night or on a weekend and it didn’t matter, they were there.”
“Danny and Pete DeGorter are the definition of integrity and hard work,” says George. “Both understand that we might be a smaller company but that doesn’t slow us down. We all do what it takes to ensure that we provide better service than most of the companies ten times larger than us. We understand that as we grow, we are going to experience bandwidth challenges. That’s just the nature of the game with any growing business, especially in the glass processing sector.”
“Our partners are searching for ways to gain efficiency, reduce waste, provide a safer environment for their people all while trying to reduce their reliance on human capital in a labor market that has been challenging over the last decade,” says Pete DeGorter, Vice President of DeGorter, Inc. “Many believe that means bringing in robots to replace people. However, that has not always proved to be the best solution. We’ve seen our partners in glass processing who’ve built a certain type of culture within their organization are not facing the same magnitude of challenges with labor as other, less than optimal company cultures. We’ve seen a mixture of adding more efficient and productive equipment when paired with a focus of building the company culture is providing the greatest results.”
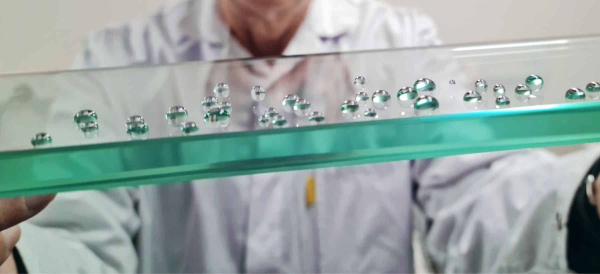
EnduroShield X-Line
“My experience with the EnduroShield’s X-line has been pretty dynamic,” says George. “While at HMI/Cardinal Shower, we tried many different hydrophobic coatings. After using EnduroShield for some time and then meeting Adrian and his team, we quickly realized that it was the coating for us and the ideal solution for our glass processing needs.”
“In the shower and architectural glass business, you basically have three options; no hydrophobic coating, a bonded product, or a hydrophobic coating like EnduroShield,” explains George. “I’m of the mindset that as glass facades and custom showers are bigger and more prominent, easy clean coatings just makes cleaning easier. I personally prefer the EnduroShield technology.”
“When I saw the first X-Line prototype, I gave Adrian honest feedback that the original frame design might not last in a high-volume manufacturing environment. That didn’t scare them at all. They went back, redesigned it, and made it very robust.”
The X-Line double-sided model presents an optimal solution for glass processors needing to accommodate medium to high volume production efficiently. Its on-demand operation is swift, allowing users to 1) load the glass, 2) observe as the X-Line processes both sides of the glass in approximately 10 seconds, and 3) unload it. This streamlined process is ideal for glass companies looking for speed without sacrificing quality.
The X-Line’s precision means it dispenses just the right amount of the EnduroShield coating, activating nozzles based on each piece’s height and length to ensure accurate application. There’s no longer a concern about over-application, even for rush orders. The process ensures that each piece is uniformly and correctly coated, eliminating any waiting time and ensuring immediate readiness for further glass processing.
“Nothing is square these days however the X-Line knows the height of each lite and which nozzles to turn off, so it is only using the necessary volume product needed to coat the glass. The operator doesn’t have to decide or wait for a batch. Every lite has just the right amount of material, ensuring efficient and precise glass processing.”
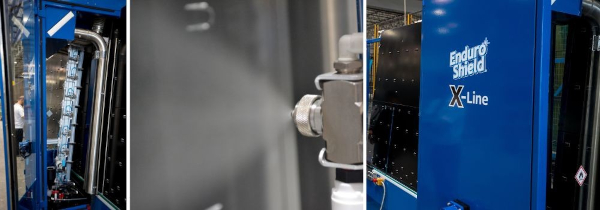
Elevate Your Operations
DeGorter Inc. proudly stands as a testament to family values, reliability, and technological advancement within the glass industry. For over a century, this family-owned business has been at the forefront of providing innovative equipment and solutions, earning trust and respect from clients and partners alike.
From the seamless integration of EnduroShield’s X-Line machines, enhancing efficiency and precision in glass processing, to their unwavering support during off-hours, DeGorter’s commitment to excellence remains unmatched. Their appreciation and understanding of the importance of company culture and employee well-being resonate deeply within their approach to business––a blend of high-tech solutions with a personalized touch.
Join the ranks of satisfied clients who benefit with the DeGorter advantage. Experience how the EnduroShield X-Line with DeGorter can revolutionize your glass processing with added revenue, speed, and efficiency.
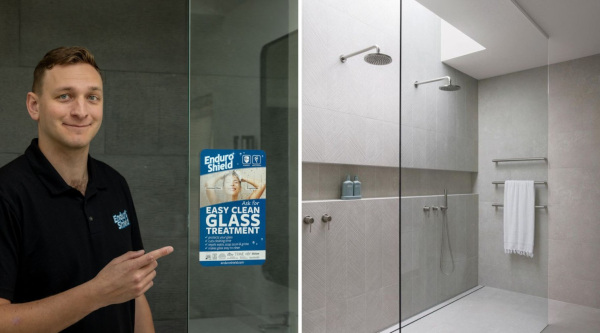
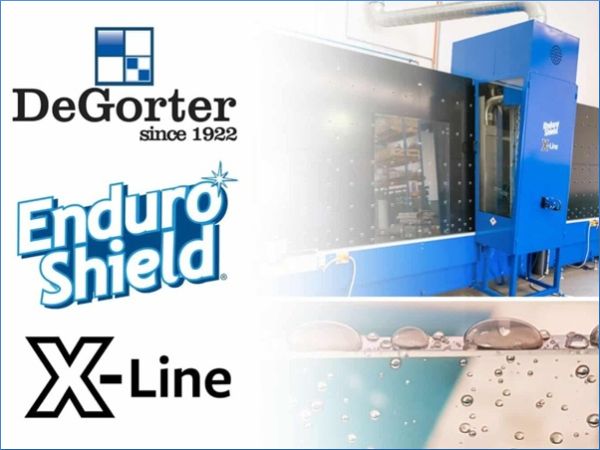

Add new comment