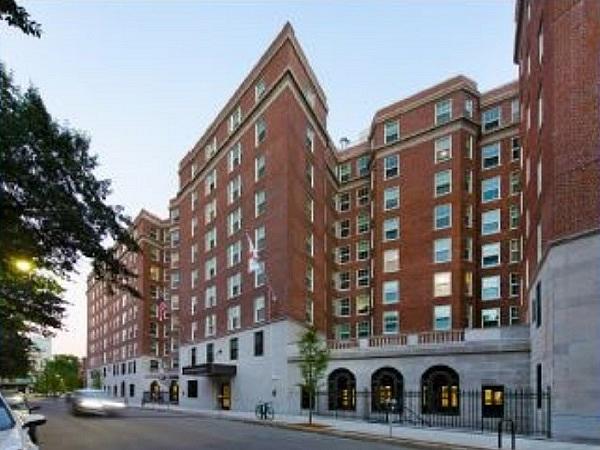
Date: 15 May 2019
NACC Certified Glazier
A&A Window Products, Inc.
Malden, MA
Team
Owners: Lee and Christine Sullivan
Vice President of Operations: Paul Giggey
Vice President of Sales and Estimating: Ian Cable
Vice President / Senior Project Manager: Matt Johnson
Engineering Manager: Harrison Morse
About A&A Window Products, Inc.
A&A Window Products has served New England for over 40 years. What began as a family-owned business focusing on Venetian blinds and window repairs has evolved into a trusted glazing vendor serving all of New England. A&A provides full-scale window replacements and repairs, curtain wall, storefront, architectural panels, interior glass, and specialty glazing. A&A attained NACC certification in February 2016 and was recertified in July 2018.
Introduction
Lee Sullivan took over A&A Window Products, Inc. in 2006, stretching his family’s 40+ year business legacy to a third generation. As President, Sullivan has fostered a culture of safety, quality, and service that extends from A&A’s employees to its customers. These core values have helped the company become one of the most trusted glazing contractors serving New England. Attaining North American Contractor Certification (NACC) reinforces those core values, strengthening the company and structuring its continuing growth.
About NACC
The North American Contractor Certification Program provides architectural glass and metal contractors with certification recognition through a professionally administered, third-party assessment, as a means of creating a baseline for competency and adherence to industry-accepted guidelines.
Teamwork
Sullivan enlisted the help of Vice President of Operations Paul Giggey to shepherd the company through the NACC program and support long-term growth objectives. Giggey came to A&A from a large window manufacturer, where he had been responsible for ISO9000 certification. Giggey understood the requirements of a third-party audit and what would be necessary to earn the NACC credential. He also knew the process would help A&A to grow and professionalize.
“I knew it was more of a resource issue,” Giggey explained. “We had processes in place, but they weren’t well documented or controlled.” For example, A&A had a safety manual, but not a quality manual. NACC helped Sullivan and Giggey improve documentation and establish a structure of procedures and policies. As a result of certification and the related process improvements, A&A also updated its technology, adding Oracle project planning, touch screen laptops for field use, and iPads with Procore and remote time entry for foremen.
Geared to Our Industry
Giggey and Sullivan liked that NACC was geared to the glazing industry. According to Giggey, “ISO certification was fairly generic and application was sometimes difficult. NACC was geared specifically to our needs.” Both felt they could immediately see the benefits.
Internal Value: Improved Revenue
“We changed from a family business to a structured corporation,” said Giggey. “Because we have policies, procedures, and control documents, we can increase volume while maintaining customer service.” He anticipates NACC will help the company double its revenues. For a certification that took just over six months to attain, the value is clear to A&A and its customers.
External Value: Myles Standish Hall
Part of the NACC program involves field visits to active projects. For A&A, field certification took place at Myles Standish Hall on the campus of Boston University. The historic 1926 student residence underwent extensive renovation, including replacement of 80 percent of the building envelope with new brick and stone to replicate the original.
In addition to installing nearly 800 new historically appropriate windows, A&A installed exterior doors, storefront glass, curtain wall, interior glass partitions and doors, aluminum composite panels, and a glass canopy. LEED Gold certification is anticipated for the 203,000-sf project, which serves as a gateway to Boston University’s East Campus.
Giggey acknowledged the lessons learned through NACC helped the A&A team better collaborate with architect Miller Dyer Spears (MDS) and facade consultant Simpson Gumpertz & Heger.
Procedures put into place also contributed to overcoming a tight urban site with limited material lay-down space, phasing and coordination for working within an occupied building, and meeting the rigorous schedule and document requirements of the project and its CM, Shawmut Design and Construction, who delivered the project with MDS in a design-build partnership.
“The CM was very professional and expected a high level of documents and procedures. We had both as a result of certification,” Giggey explained. Certification ensured A&A met all requirements for the high-profile project and exceeded expectations of the architect, CM, and Boston University.
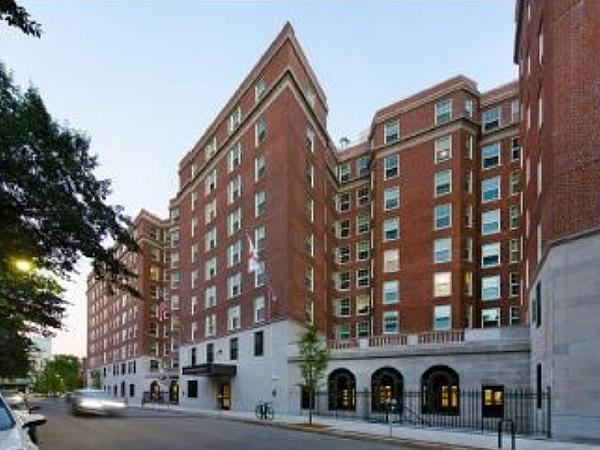

Add new comment