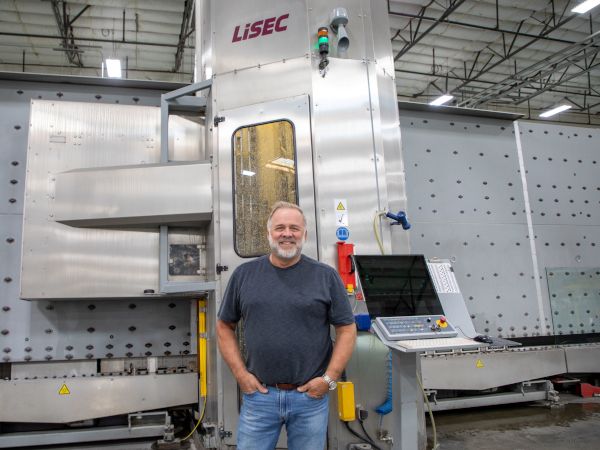
Date: 20 November 2024
Thermalsun, located in Santa Rosa, California and founded in 1988, has built a reputation for high-quality products and has a loyal customer base in California. An important factor in Thermalsun's success is the reliability in the equipment they use, which consists of mostly LiSEC products.
A closer look at Thermalsun
Thermalsun, with its team of 50 dedicated employees and a plant size spanning roughly 6700 sqm specializes in high-end glass products. The product range is diverse, including products such as annealed glass, tempered glass, laminated glass, heavy glass, spandrel and their main product, insulating glass. The company primarily serves the San Francisco, Bay Area and Sacramento Valley, focusing on the replacement market, heavy glass and commercial projects. Despite the challenges posed by fires and high living costs in California, Thermalsun has managed to thrive, emphasizing quality over cost and producing reliable products with on-time service. Additionally, sustainability is at the core of Thermalsun’s operations, with strategies in place to optimize glass usage, minimize waste, and reduce fuel consumption through efficient delivery schedules and routes.
Thermalsun’s journey with LiSEC: From a single cutting table to a full production line
The partnership between Thermalsun and LiSEC spans more than two decades. It began with the purchase of a cutting table in 1998 and has since expanded to include various other machinery and software for glass processing. “We had a really good experience with LiSEC when we bought our first cutting table. One year later I visited another glass processing company which had a LiSEC insulating glass line in use. Seeing the line running convinced me to buy a LiSEC insulating glass line for Thermalsun,” says CEO Jeff Kloes. This has proven to be the right choice as the insulating glass line has been operating since 2000 with a downtime of 3 days so far. The machines require minimal downtime, allowing the Californian flat glass processor to meet its commitment to on-time service. The company’s success and growth can be attributed in part to the efficiency and reliability of LiSEC’s machinery. “When people come here to look at our equipment I tell them that we can’t afford to be down and that you may pay a premium for a LiSEC product, but rest assured it will run day in and day out.“
Thermalsun values LiSEC’s reliable and easy-to-use equipment, which has significantly increased productivity while maintaining consistent product quality. LiSEC’s equipment has become an integral part of Thermalsun’s production process.
About the usability CEO Jeff Kloes says: “It’s just push the button and go. From an operators standpoint, once you learn the equipment, it’s easy to run.”
To have perfectly trained operators Thermalsun made use of LiSEC’s in house training in Austria. A long term employee of Thermalsun was trained on the LiSEC machines. The knowledge he brought back to the states allows the company to train new employees on the equipment.
In the industry LiSEC stands out because of their excellent service, according to Jeff Kloes: According to Jeff Kloes, “LiSEC goes the extra mile when it comes service. The experienced maintenance crew is well versed in the equipment. They know what they are doing from the start of the phone call all the way to the end, allowing us to be back up and running as quickly as possible.”
LiSEC equipment at Thermalsun
Thermalsun has two LiSEC cutting tables in use, a GFB to cut laminated glass and an ESL-RS for cutting at high speed with semi-automatic breakout. Both cutting tables are fed by a LiSEC logistics system consisting of a PKL and SBL. To process flat glass Thermalsun uses several LiSEC machines such as a KSR, KSV and a VHW washer. The KSR is a vertical compact grinding machine that can seam all four sides of the glass sheets. Complementing it is the KSV, which seamlessly handles the bottom edge seaming, enhancing the cycle times. The process is further refined by the VHW washer, ensuring each glass pane is clean before undergoing further processing.
The LiSEC insulating glass line has been a cornerstone in Thermalsun's production of high-quality insulating glass (IG) units for over two decades. The longevity of the machinery is a testament to LiSEC's commitment to durability and quality. Through the LiSEC LONGLiFE programme, Thermalsun has been able to keep its machinery up to date with systematic upgrades, such as PC updates, which extend the life of the entire system.
In addition to that Thermalsun also uses stand-alone-machines from LiSEC such as LiSEC butyl extruders for the insulating glass production. The LBH-25V is a butyl extruder for rigid spacer frames, designed for precise butyl application across all common spacer widths. It features frame guidance, integrated width detection, and electropneumatic pressure control. The machine highlights include optimum coating of even circular curved spacer frames, shortest butyl refill times because of the swivel-out butyl cylinder with a 14-liter filling capacity, and the ability to adjust the working height. Thermalsun also uses a LiSEC ARL-45F desiccant filler which is suitable for filling thin-walled stainless steel profiles as well as plastic profiles can also be used for special shapes.
More information about LiSEC products: https://www.lisec.com/solutions/individual-machines
A brief look into the future
Looking ahead, Thermalsun plans to stay competitive by adding another IG line to accommodate larger glass sizes. The company also aims to keep abreast of industry trends, such as the rise of heavy glass.
Despite the impact of the COVID pandemic and economic factors, Thermalsun remains optimistic about its future, ready to face new challenges and seize new opportunities.
Tip: LiSEC offers in-house training for operators and maintenance personnel. This not only facilitates knowledge transfer to other workers but also saves time, by reducing the duration of on-site training.
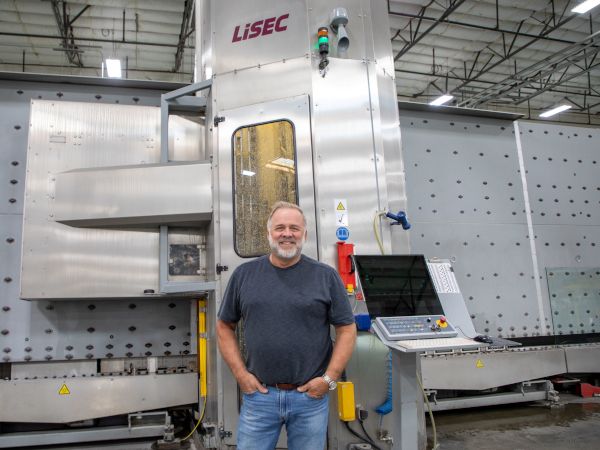

Add new comment