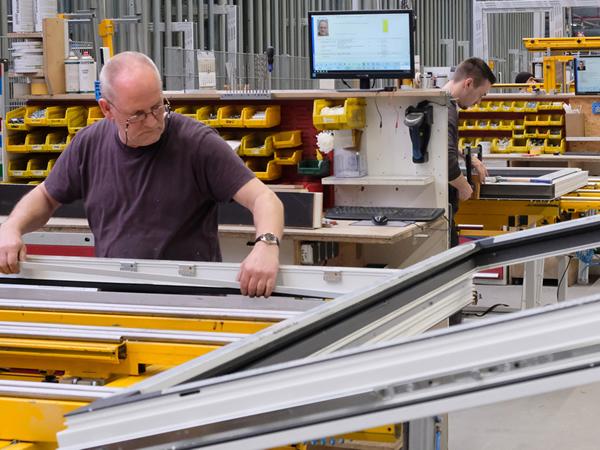
Date: 19 August 2019
Good ideas are a great thing. However, life gets really exciting when they are implemented constantly and consistently. This implementation is at the core of window builder Siems’ success in Wiefelstede, Germany.
With the experience of three generations of owners, leading technology partners, intelligent software, and a creative team, downtime is a foreign concept at Siems. Things are lively and bustling in Wiefelstede, where people are developing intelligent products. Under the management of the brothers Karl-Wilhelm, Uwe, and Betram Siems, the result has been constant innovation and expansion in recent years, as well as new paths to market.
The production area has expanded constantly since 2006. In 2017, this window maker in the Ammerland took a kind of quantum leap and doubled its production area from 10,000 to 20,000 square meters. Prior to that, a unique light-flooded administration building was built, a place where everybody, from trainees to upper management, works together in a pleasant, peaceful, and transparent atmosphere.
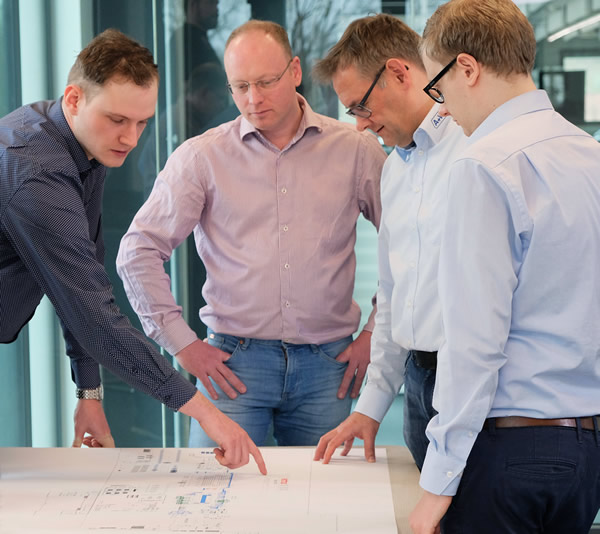
Automatic line production
Many good ideas can be implemented in 20,000 square meters. In the innovation network with the machine manufacturers Rotox and Lemuth and software partner A+W, a 220 meter-long completely automated production line was created, one that is unique in European window production. All workers work on the machines and manual workstations from the outside.
This was Siems' basic requirement, one that originated from positive experiences in other industries. With this concept and the new system technology, Siems produces significantly more windows and doors with fewer employees per shift. Machines are synchronized with transport sections and buffers, shuttles feed frames, sashes, and lites into the buffer and steer them out at the right time in the right sequence for assembly, special construction, and glazing.
An especially intelligent solution was implemented in glazing, where software is used to control which elements and lites are provided in alternation on a transport section in the glazing sequence. Here there is no more searching and carrying insulated glass units back and forth. The units are fed in and glazed professionally, quickly, and in cycles.
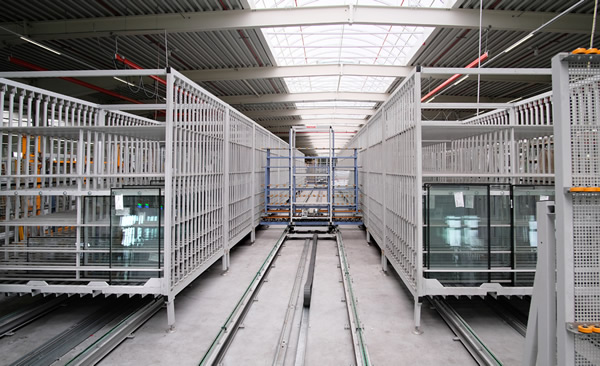
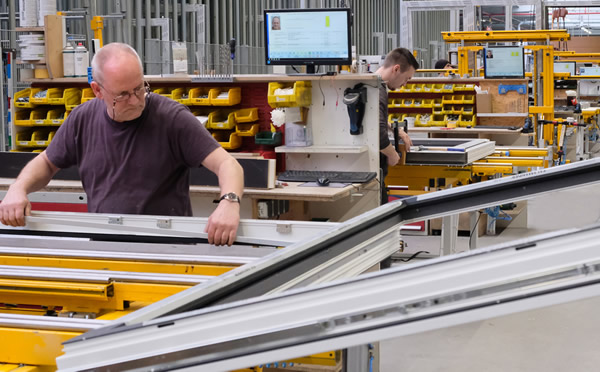
The 1-minute cycle
One of Siems' requirements was the implementation of the 1-minute production cycle - each workstation up to glazing requires approx. one minute of processing for a single sash tilt and turn window. This was a significant demand could only be fulfilled successfully thanks to the intelligent planning approach and high degree of automation implemented by Siems and their software partner A+W. The batch size is 1.5 on average meaning nearly every product is unique. This output is achieved with just eight to ten employees per shift, making this quite an accomplishment!
More windows for more customers
The increased production capacities allowed Siems to spend more time on customer acquisition and to deliver orders on-time. Siems has customers across northern Germany and works only with trade partners from small customers who order one window per year to large customers with hun-dreds of windows a year.
The company has consciously avoided developing its own project busi-ness/sales force. Siems does not advertise actively nor does it have its own sales force. However, the dealers are supported and trained extensively making this endeavor a successful one for Siems. Each year, the company organizes a dealer information day. The Siems team was pleased to wel-come more than four hundred participants to its last event.
Electronic order, paperless processes
Thanks to the A+W Cantor IT system, all administration processes are paperless. There haven't been any customer files that go along with the process for a long time. Seventy to eighty percent of Siems' trade partners order electronically using the A+W Cantor dealer software. There are advantages to this for both sides, the dealer configures and orders using a professional entry system. Because the system always has the current Siems master data and conditions, it can provide customers with a reliable, professional quotation very quickly.
The A+W Cantor dealer software subjects the order to all necessary restriction checks. All the orders that arrive at Siems can actually be built - the Siems order processors only have to check the order briefly, so there are no more time-consuming telephone consultations, etc. This way, each order can be transferred to production quickly. Siems rewards customers for this, explains Karl-Wilhelm Siems: "The customer who orders via EDP saves us a lot of entry and management work and, therefore, receives a price break."
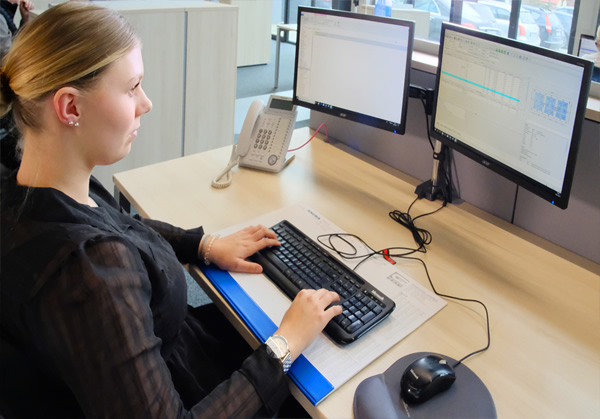
Software-controlled production
The highly automated production is controlled by A+W Cantor with a comprehensive barcode-supported software system in production and shipping. Here, "paperless production" is just one aspect meaning no employee searches for anything, the elements are only transported automatically. Each action creates value.
This is only possible if machine technology, the buffer and transport system, and the controlling EDP systems, work hand-in-hand and are optimally attuned to one another. Siems, the machine manufacturers ROTOX and Lemuth, and the software partner A+W Cantor have proven that they can cooperate closely from the beginning planning stages.
The highly complex software control defines whether the ROTOX transport systems send the windows to the quick or standard line or to the manual workstations. "The IT system," explains Jens Hulshof, Area Sales Manager for ROTOX, "ensures that workstations where employees with a lot of experience work are fed more complex elements, while a new employee receives the simpler elements with standard processing to work on."
Monitors and scanners replace stacks of paper and folders; elements are identified, registered, and reported ready via barcode reading. The precise information needed is displayed on A+W Cantor CIM screens at manual workstations meaning that the production flow is constant and smooth.
Of course, A+W Cantor CIM works seamlessly with A+W Cantor Enterprise, the commercial-administrative part of this comprehensive information technical solution. Here, information, such as control instructions for the CNC machines, production, and status reports for the order system, are exchanged in real time.
Thanks to this completely networked system, Siems provides its customers with an information system they can use to check the status of an order in process or an item by themselves at any time. "A+W Cantor is a system with an open database," explains Karl-Wilhelm Siems. "This enables our IT team to make modifications and develop additional functions that are important to us. For a company that actively controls its processes, there is no better system in administration and production. We have been working with A+W Cantor for fourteen years and we have never regretted it for a second."
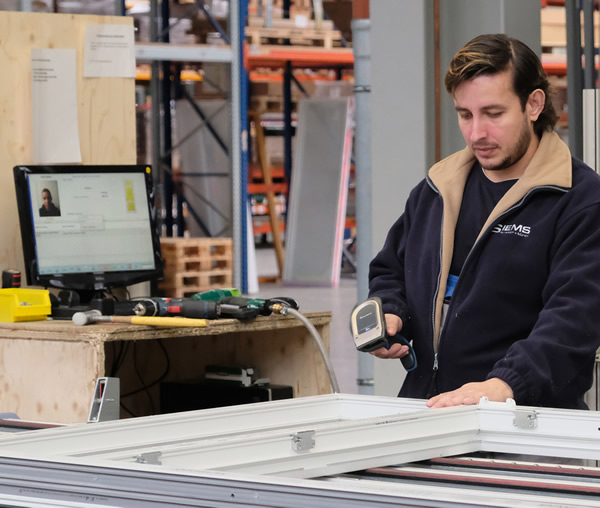

Constant innovation
At Siems, everything is always on the move, but the innovations are implemented quietly and with a sense of the right proportion. "Recognizing market opportunities, designing high-quality products, and using new technologies throughout" – that's our credo, explains Uwe Siems.
A constant willingness to change has been this company's recipe for success for three generations. That also includes a pleasant portion of Ammerland stubbornness: once you've undertaken something, you don't quit. You take a deep breath and persuade others. And with considerable success, as you can see.


Add new comment