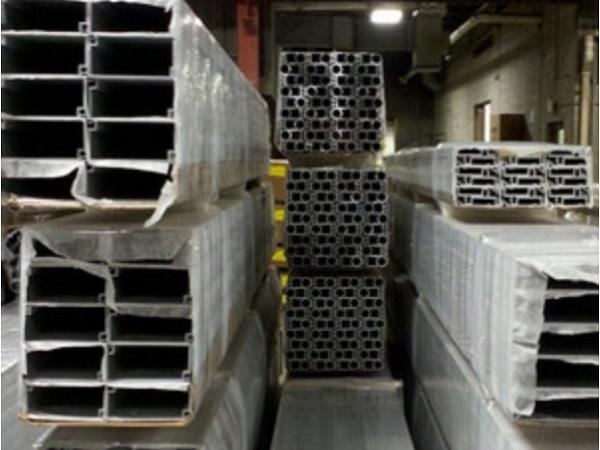
Date: 7 July 2017
Work on these topics and more will continue this October during the 2017 National Fall Conference in Greenville, SC.
Planning for the Future
With LEED, green building programs, and sustainability foremost among member concerns, the mission statement of the Aluminum Material Council and objectives for an AMC-focused strategic plan were reviewed.
Council Second Vice President Scott Condreay (SAPA Extrusions) presented the short term strategic objectives (1-5 years) as follows:
- Updating white paper content, drawings and pictures to promote the attributes of aluminum for sustainability, energy efficiency, finish options, strength, recyclability, etc.
- Adding reports from the Aluminum Association (AA) and Aluminum Extruders Council (AEC) as standing meeting agenda items.
- Inviting AMC web page viewers to participate in Council meetings.
- Presenting aluminum-focused updates on AAMA market research reports at conferences.
Long term strategic objectives (5-7 years) include growing the recruitment of aluminum manufacturers and extruders, and monitoring energy and code requirements specific to aluminum.
A conference call will be scheduled to finalize modifications to the council mission relative to inclusion of end users, with the intent to seek final approval at the end of that meeting.
Revisions to Aluminum Finishes Standards
The AMC Finishes Committee (Chair: Carl Troiano [Trojan Powder Coating]) has been revising the film adhesion tests in AAMA 2603, 2604 and 2605.
Per the ballot document, the current language in AAMA 2603, 2604, and 2605 would be removed and replaced with only a reference to ASTM D3359, which includes different procedures for varying coating thicknesses that were previously omitted, rather than re-stating the ASTM procedure within the AAMA documents.
Language was also added to clarify that all tests shall be performed sequentially as shown in the specification, and on the same test sample using the same set of cuts for each test.
In other words, the test sample will be scribed and then tested for dry adhesion, boiling water adhesion and wet adhesion. Additionally, the criterion for a passing test has been changed from level 5 to level 4b, and the order of testing was changed to dry adhesion, boiling water adhesion and wet adhesion.
In an earlier version of the proposed language, only performance criteria for products tested to Method B was included. ASTM D3359 specifies two methods for testing: Method A should be used for film thickness greater than 5 mils (125 μm). Method B should be used for film thicknesses up to 5 mils (125 μm). Proposed language was added to indicate performance criteria for samples tested to Method A.
Of the 105 ballot responses, two were disapprovals with comment. The disapprovals centered on the wet adhesion section, with commenters objecting to the 24-hour immersion test as impractical in a finish applicator plant environment.
Voters instead felt it should be included in Verified Component Program testing at an outside accredited lab. The group consensus was that while this test may not be applicable to quality control in an applicator’s facility, a 24-hour submersion test is necessary for new product qualification and inclusion on the Verified Component List (VCL).
To clarify the concern, a new task group, the AMC/FMC In-Process Finish Applicator Quality Control Task Group (co-chaired by Manny Mayer [Axalta Coating Systems] and Ivan Zuniga [YKK AP America]) was commissioned to develop a guidance document for in-process quality control for compliance to AAMA 2603, 2604, 2605, 611, 612, 623, 624 and 625.
The Laminating on Finished Aluminum Profiles Task Group (Chair: Bruce Carriere [Akzo Nobel]) has been working to determine if existing requirements for laminating on profiles made of vinyl and other substrates can or should be adapted for aluminum profiles. At the recent Summer Conference, the proposed language adopting the language for vinyl profiles was finalized.
With these final measures adopted, the task group voted to release the full third-party lamination certification document to the appropriate finishes committees for ballot. Its work thereby being completed, the task group formally disbanded.
Common Weathering Ground Sought with Fiberglass Finish Standards
The Accelerated Weathering Task Group (chair: Scott Zimmerman [Atlas Material Testing]) has been reviewing accelerated weathering options for AAMA 2603, 2604, 2605, 611 and 612 (aluminum organic and anodize finishes) to determine if the protocol established by the Fiberglass Material Council for AAMA 623, 624 and 625 (fiberglass finishes) is appropriate for the aluminum finish standards.
Presentations have been delivered to the task group on a variety of accelerated weathering test methods and equipment. Testing will be conducted on panels contributed by members to determine which accelerated weathering requirements best correlate with outdoor weathering. The Chair will provide a draft of the panel request to AAMA staff, who will then distribute it to the task group via email.
Weathering Test Preference Continues to Await Outcome
The Pre-Treatment Task Group (Chair: Ben Mitchell [Akzo Nobel]) has been conducting testing to evaluate alternatives for the use of salt spray fog to accurately quantify corrosion.
The results of the testing are considered essential to developing pass/fail criteria, pursuant to the possible replacement of the B117 test with the G85 method in AAMA 2603 and 2604, as has already been done in AAMA 2605.
Work has been completed regarding AAMA 2605 requirements, involving 2,000 hours of exposure per ASTM G85, Annex A5. The current testing is on AAMA 2603 and 2604 panels to establish the number of hours correlating to outdoor weathering.
AAMA 2603 and 2604 interim test results for ASTM G85 Annex A5 vs. Battelle outdoor weathering were reviewed. Panels will remain in place for continued exposure for at least an additional 12 months, with data provided by Battelle about 10 days prior to each AAMA national conference.
Given that it is too early to run correlation analysis, additional time is still needed to complete the requisite three years of exposure. However, it was noted that data appears to be tracking similar to results from 2605 testing.
Correlation analysis of the current test results will be completed and sent to the task group members or presented at the Fall Conference. The expectation is that correlations will be complete and depending on results a decision may be able to be made by the 2018 Annual Conference.
Decoding Corrosive Environment Performance
Related to the Pre-Treatment Task Group’s work, the Corrosive Environment Coating Task Group (Chair: Bruce Carriere [Akzo Nobel]) is seeking to develop a stand-alone, higher performing specification for corrosion that applies to all three existing aluminum coating specifications (AAMA 2603, 2604 and 2605).
This is in response to architects’ expressed desire for recommendations on corrosion resistance testing and performance levels that will stand up well in highly corrosive environments.
The group remains dormant until full outdoor weathering test results and data become available from the Pre-Treatment Task Group.
Visual Assessment Study Finds Hunter Color Space Acceptable
The Color Space (Hunter/CIELAB) Task Group (Chair: Sean Fowler [Q-Lab]) announced that, per the results of the visual assessment study conducted at the 2016 Fall Conference, members agreed to recommend that Hunter (vs. CIELAB) should remain the color space used in AAMA finish standards and the parameters within that color space should remain at the discretion of the Material Councils.
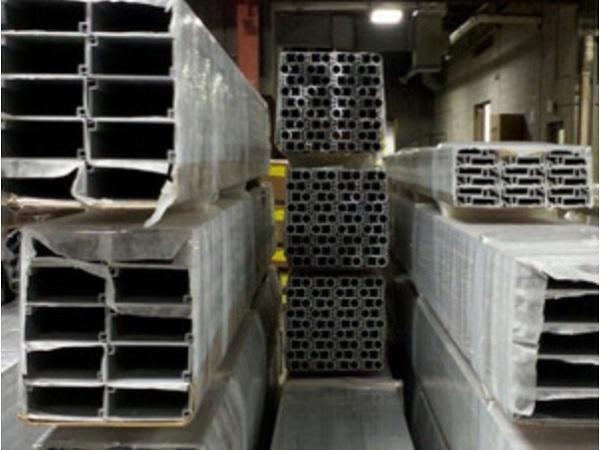

Add new comment