Historic building window replacement presents a variety of challenges. The replacement must balance the needs and expectations of the building owner and building occupants with current code requirements, historic commission or other historic review board requirements, and the physical properties of different window systems, all while maintaining the historic building’s fabric, character, and architectural integrity.
Primary considerations in historic window replacement include:
- Desired thermal and acoustic performance
- Façade integrity
- Condition of existing window openings
- Interior building conditions
- Historic review and approval requirements
- Aesthetics
- Price
MANY PARAMETERS
Each design parameter affects the others. For example, historic requirements may mandate narrow sight lines to replicate original glazed wooden sashes. New insulating glass might impact the muntin profiles or change shadow or sight lines.
A custom finish that eliminates the need for repainting may require thermally separated aluminum framing with deep glazing pockets. Deteriorated building framing may require a custom window rather than an off-the-shelf product.
Knowledgeable glazing contractors who evaluate and replace historic windows fully understand repair techniques and the available options for restoration, conservation, and replacement to meet all of a project’s parameters successfully and efficiently.
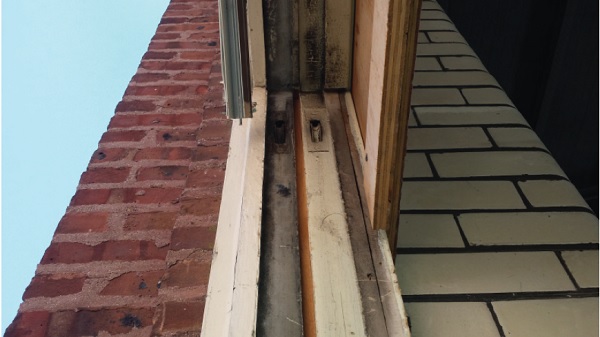
(images courtesy National Glass & Metal Co, Inc.)
THE UNKNOWN
The biggest concern with glazing replacement in an historic building of any kind is not knowing what might be uncovered during demolition. The glazing contractor’s estimating team often uses the architect’s drawings to determine a fair price; however, the field conditions may vary dramatically from the drawings.
The owner, architect, and glazier cannot know the true condition of the wall until the old windows have been removed and demo is complete. Often, the historic opening is out of square, either due to primitive early construction methods or building movement over time. The difference may be subtle or significant.
There may also be structural issues associated with deteriorated window framing or deteriorated masonry around the opening. Repair measures may affect glazing dimensions and the type of glazing system or product specified.
COMPLEXITIES
Once demo is complete and the design and construction team can assess the historic building conditions, there are many devils that influence the details. The need to retain historic building fabric – from the exterior wall material to interior finishes – may require creative solutions so that windows fit precisely into original openings.
A specified or purchased unitized or prefabricated window may not fit into an opening that is not square; instead a custom window would be required to compensate for the building’s unique condition.
Custom trim elements may also be required to cover ragged edges around the demolition site. Old caulk or paint may need to be removed prior to installing new windows; as with any instance of old surface finishes, there are concerns for asbestos or lead presence that require abatement measures.
Then there is the added complexity of ensuring the window installation is watertight, to preserve the integrity of the wall.
SPECIAL CHALLENGES
Special conditions in historic structures warrant special design attention and creativity. Matching historic windows with modern counterparts may require glazing solutions that modify the windows’ pressure walls or incorporate custom aluminum extrusion profiles.
A professional glazier understands how to create a custom die or custom break-metal shapes to match historic window profiles. The new windows can be structurally sound, match desired thermal properties, and precisely fit the out-of-square openings.
When replacing historic windows with modern counterparts, replicating the original appearance presents interesting challenges. First, the existing systems’ anchoring points must withstand the loads of the new windows.
Multiple windows within one opening typically require each window to have its own exterior panning system. Panning is used to cover the perimeter of existing openings before installing the replacement windows.
Panning protects the existing building finishes; offers a clean edge to cover anchorage points and any ragged frame details from demolition; and comes in a variety of profiles.
If the original architecture incorporated a brick molding along the masonry perimeter and not around each window, the molding cannot be integral to the panning around each window.
In these cases, either a second aluminum shape is added to the perimeter or all the windows must be preassembled within a single panning system with specially designed intermediate panning shapes to cover the mullions.
Given the unique structural conditions and architectural details on historic buildings, panning on historic window replacements is about 90 percent custom.
A glazier must often design and fabricate custom extrusions to match the original profiles; these extrusions are often never used again.
STEPS IN DESIGN
As a valued member of the design team, a glazing contractor can contribute expertise and experience to the process.
The following steps are generally undertaken in historic window replacement:
- Measure typical opening configurations and sketch section details.
- Research historic records to determine the original window designs.
- Select products with comparable internal sections, such as meeting rails, sash stiles, and lift rails.
- Design new exterior panning to replicate the existing molding and frame sections.
- Select matching applied muntin designs from manufacturer’s standards or develop a custom design to match building conditions.
- Review design load requirements to determine mullion and anchoring capacity needed.
- Determine which existing frame elements can remain and which ones must be removed or reconstructed to maintain sight lines.
- Prepare drawings to show the original window designs and sight lines in comparison with the proposed replacement.
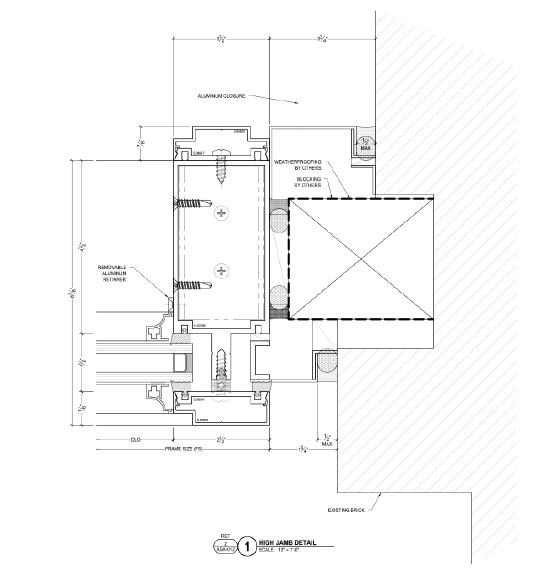
(courtesy National Glass & Metal Co., Inc.)
THE TOURAINE
At The Touraine apartment building on Rittenhouse Square, the owner wanted beautiful windows and doors to replace the 1917 originals.
Listed on the National and Philadelphia Registers of Historic Places, The Touraine needed to comply with Philadelphia Historical Commission requirements.
The window replacement goals included warm, comfortable, and quiet interior spaces; maintenance-free exteriors; and windows and doors that would last for another century.
The window replacement also had to preserve the historic sight line requirements in order to gain Historic Commission approval.
Graboyes Commercial Window Co. installed 870 energy-efficient insulated, low-e glass aluminum windows and 61 French doors, designed to match the historic originals.
Frames were finished with a painted wood interior trim, while 144 leaded glass panels were restored into new wood windows.
Graboyes worked directly with manufacturer Skyline Windows and the owner to identify and select a product that could be adapted to the project’s specific requirements.
The collaborative effort achieved both code requirements and historic guidelines in the replacement solution. The terrace door openings introduced a unique structural issue.
The intermediate mullions had to be completely removed and recreated with new structural elements in order to preserve sight lines and still meet the considerable design pressures for the large openings. They also had to carry and support railings to meet fall protection loads.
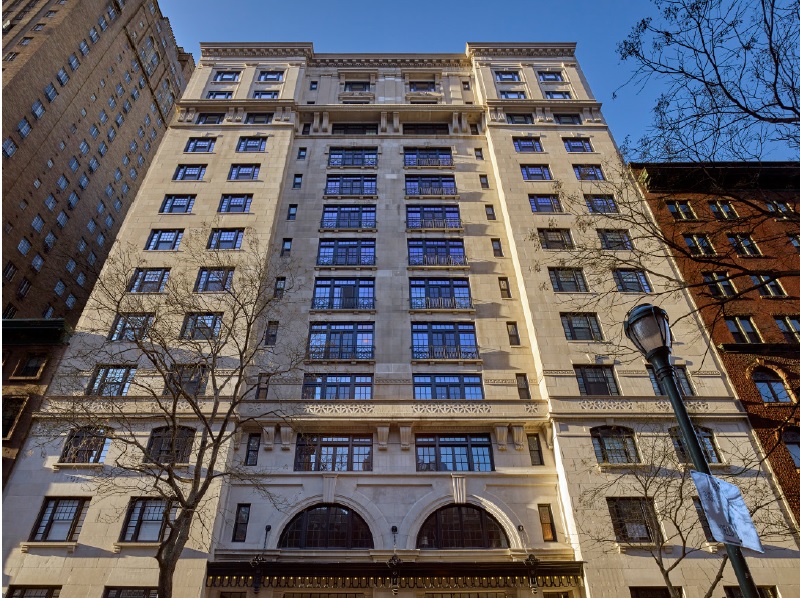
J&J MUSEUM
At the Johnson & Johnson Museum in New Brunswick, N.J., National Glass & Metal Co. Inc. replaced very large wood windows from the mid-1800s. The client and designers at Jacobs/Wyper Architects desired replication with new aluminum windows.
In order to preserve the historic character of the building, the architectural integrity of the brick wall, and the original interior wall tile finish, the glazing team from National created new aluminum extrusion profiles to match the original windows. The custom extrusions were painted and used to fabricate the new windows.
As a result of the customization, the new windows fit snugly into somewhat out-ofsquare openings, are weather tight, and achieve the desired thermal properties.
Although a glazier may never have a use for the same extrusion profile, it is a component that can gladly be customized to meet design intent in an historic window replacement project.
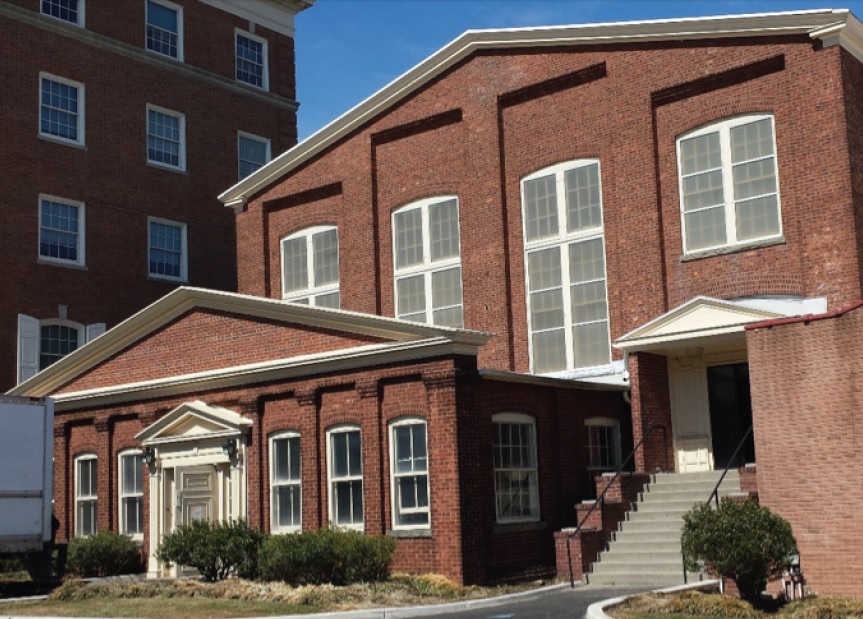
(images courtesy National Glass & Metal Co., Inc.)
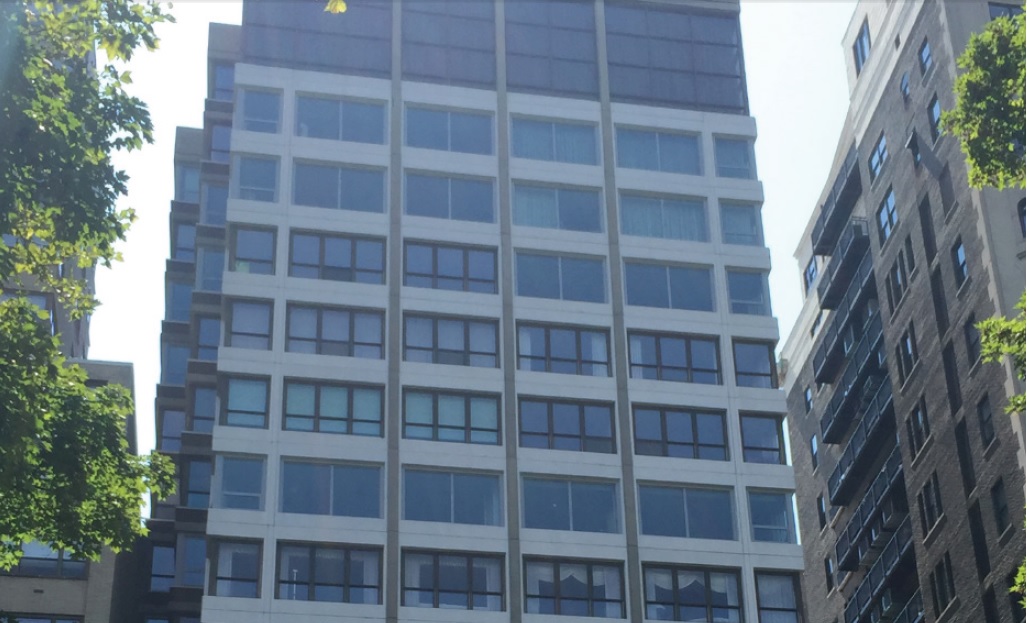
(image courtesy GMI Contractors, Inc.)
1820 RITTENHOUSE SQUARE
In most historic window replacements, a review board or historic commission mandates retaining existing sight lines, meeting rails, and window profiles.
However, there are exceptions. 1820 Rittenhouse Square was built in 1971 with double-hung windows. When it came time to replace the windows in the 19-story building, the owners collectively resisted replacement in kind.
They argued for a different type of window that would maintain the architectural integrity but also optimize their views of Rittenhouse Square.
GMI Contractors, Inc., and architect Martin J. Rosenblum & Associates, AIA, worked with the owners and property manager to investigate and identify an appropriate solution that would win Philadelphia Historic Commission approval.
The solution had to meet code, be structurally sound within the existing openings, preserve sight lines while capturing improved views, and offer ventilation. After exploring many options – 46 different design iterations overall – an awning window system was selected.
The Wausau awning windows include a solid top lite above an operable vent. The glazing design team was charged with making the meeting rail as low as possible. This required balancing the weight of the top lite while retaining structural stability for the vent to operate.
If the glass is too heavy, the large framework precludes the vent from opening; supporting steel isn’t an option because of the hardware position to meet ADA compliance. The final scheme put the meeting rail 26.5 inches from the rough opening.
Two awning windows per bay replaced the original configuration of three double-hung windows. Shim sizes, hardware, and other details were adjusted after demo to accommodate the existing conditions.
The team worked with the historic commission and the owners to find a mutually agreeable replacement. GMI admits it was a learning experience; teamwork among all of the design professionals ensured a creative solution and successful outcome.
Comments
Windows replacement would be beneficial for every house and building, especially the from the old buildings, where we have found traditional old window designs. In different cities, we have found people are taking beneficial steps to replace their old traditional looking windows into a new modern window. We can get best professional window replacement service from different sources in different regions with affordable cost. So, to get a perfect look for our home exterior, we need to replace the old windows.