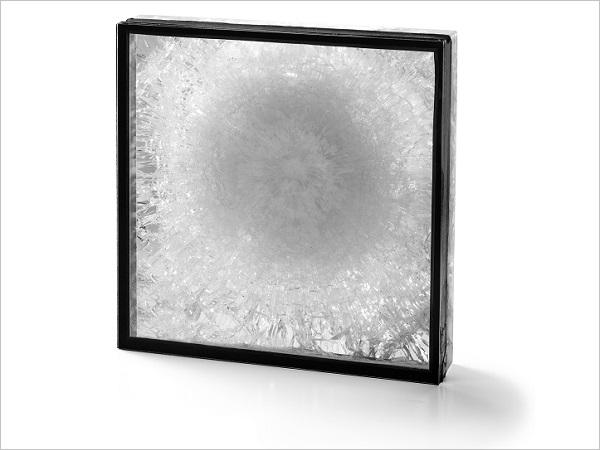
Date: 27 June 2022
The topic “blast resistance” is not new but is becoming from particular interest since many years. Terrorist attacks, for example, are not only increasing over the last years within the European Union (EU) but also worldwide. The consequences of an explosion are severe. For that building envelopes must be designed to withstand such attacks. Curtain walls are a major part of the building envelope. Therefore they must withstand not only typical, structural loads, such as wind or barrier loads but also blast loads.
An adequate and reliable design of the structure is today more than necessary. As Louis Dellieu, Perrine Leybros and Julien Jeanfils have shown in their paper “Are Laminated Security Glazing Standards Still Adapted to the Current Demand ?” that the current standards and regulations do no address the current design requirements. The modern architecture is requesting larger glazing elements which must fulfill multiple properties and functions. Current standards, such as EN 13541, do not address these development. As the glazing blast response is very dependent on its size, it is very important to verify the real size of glazing within a project. Another important fact is that the intensity and load duration of the current EN 13541 is not representative any more.
EN 1279-5, the product standard for insulating glass units, describes extension rules for explosion resistant glazings. But these rules must be handled with great care. It seems that applying these extension rules may lead to an over- estimation of the IGU performances. But looking in more detail to the possible extension rules and depending if the security component of the IGU is on the exterior or interior side, the two panes could touch each other which may lead to glass breakage as well.
Another aspect which is addressed differently in the available standards, is the intensity of a blast and the duration of it. This could lead also to a different behavior of the glazing element. The result could be on one hand an overestimation of the glass thickness or on the other hand a too thin glass pane.
As the assessment of the glazing element due to a bomb blast load is dependent on different parameters, such as size of the glass panes, the type of the explosion, its intensity and duration, and due to the fact that with the current standards not all parameters are addressed, it is sometimes necessary to make a blast simulation instead of a physical test. It is also important to consider the glazing response. This means if the glass is not breaking or if there is a high hazard.
According EN 13541:2012 it is mentioned that “The classification is only valid for the tested glass size. Based on theoretical considerations and/ or experimental work, the results can be used for the estimating the explosion pressure resistance of other glass sizes”.
This means that a simulation could help to evaluate the appropriate glass make-up and physical test could sometimes avoided. With the help of simulations together with already verified and tested glass make- ups time and money can be saved. Also new developments and products could be verified before doing a physical tests. As mentioned above for certain projects it is possible to extrapolate existing, tested, glass make- ups.
The engineers of AGC can help to evaluate the appropriate glass configuration based on the above mentioned parameters. With the knowledge about products and one of the largest product portfolios of a global glass company the engineering service could help you for a successful project.
More information: tas@agc.com
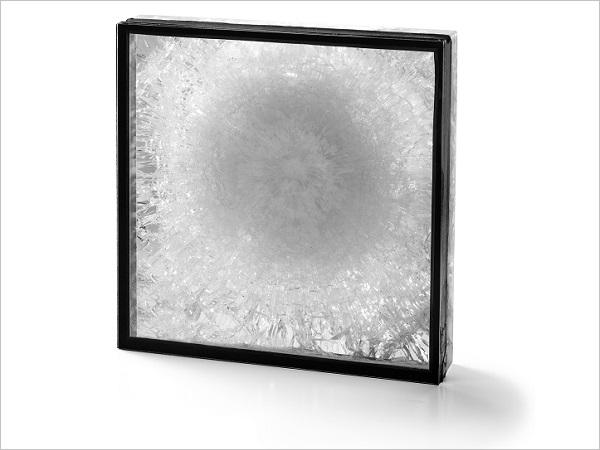

Add new comment