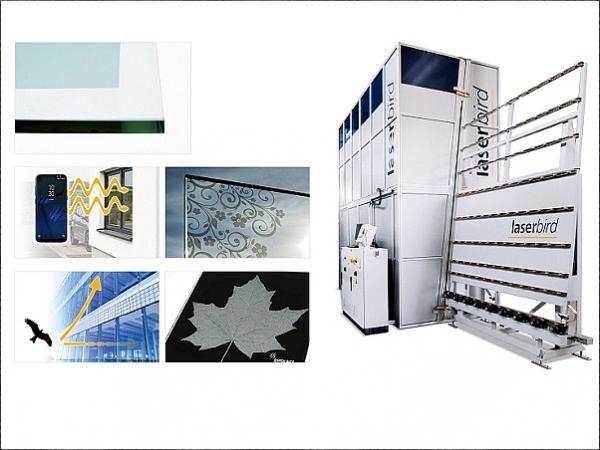
Date: 30 January 2019
The trend towards new applications in this segment has not been driven exclusively by technological progress. In fact, the development has far more to do with changes in customer demand and the more general feasibility of options for generating greater added value.
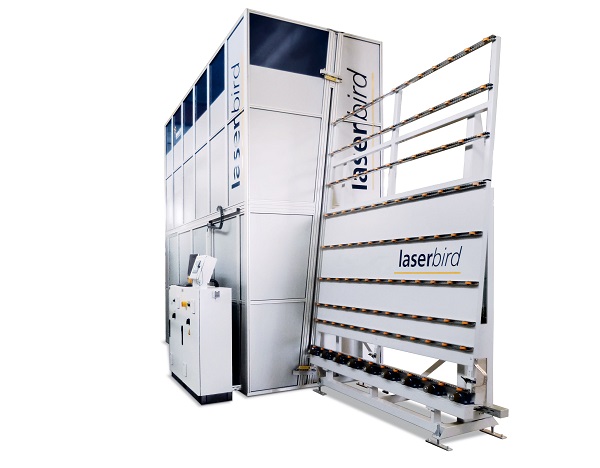
Laser processing of custom glass products
Until recently, laser-assisted finishing in the glass processing industry was seen primarily as an aesthetic tool for fulfilling custom glass designs. The laser printing process is used to apply a wafer-thin, scratch-resistant pattern to the glass that matches the specified template. When working with coated glass, the physical properties of the coating can also be used to turn it into a sample or another motif through careful application of the laser.
“What makes these two processes special is that they don’t require any tooling or set-up time – and that applies to the production of both one-off pieces and larger-volume series,” explains Dr Thomas Rainer, Head of Development and authorised signatory for HEGLA boraident in Halle/Saale, Germany.
Among the company’s many proprietary development is the Laserbird, a system that can be used for finishing on single-glazed panes, laminated glass and insulated glass units (IGUs).

Laser decoating for a crystal-clear surface with no scratches
The increasingly strict demands with regard to the quality of structural glazing and edge decoating in general are making the laser a more popular tool for these types of applications, too.
“Decoating using laser technology is gentle, highly precise and causes zero damage to the surface,” emphasises Dr Thomas Rainer. “We have customers who use laser decoating for controls on their machines or to create lighting effects behind mirrors, for example.”
Dr Rainer promises crystal-clear results with no scratches, which also makes this technology suitable for later viewing areas, such as facades.
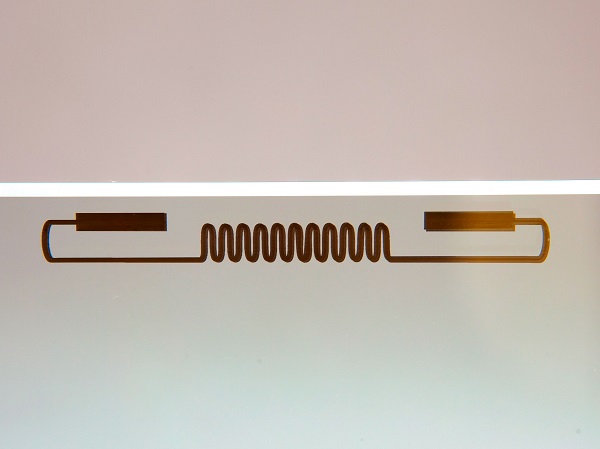
High-functionality smart glass
In addition to finishes of high aesthetic quality, the added functionality of smart glass is another area with potential for the future. Glass products that can now be produced using laser techniques include glass with increased permeability to mobile communication radio waves – perfect for use in areas such as conference rooms and offices.
The technology can also be used to finish bird protection glass, apply site-specific sun protection or increase radar dampening in areas close to airports. There is also the option of using laser prints or coating conversion to turn glass panes into conductors, which can then be used for technical applications.
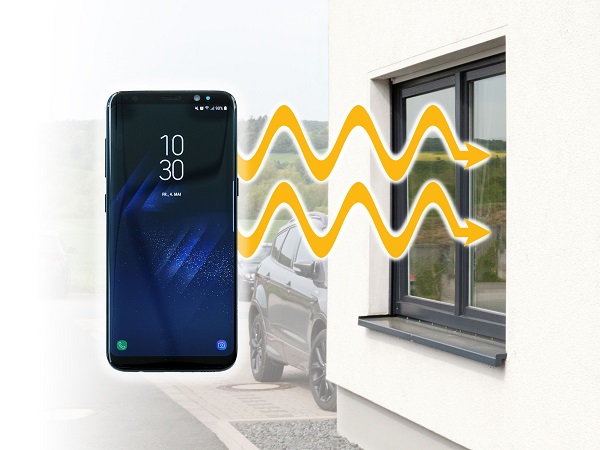
Clear markings for traceable glass and product identification
The laser-assisted design and functionalisation of glass panes is used primarily for finished products that are designed to provide added value. However, as the Internet of Things grows and production processes become increasingly automated and digitalised, laser technology is becoming more important for use in identification processes.
In order to facilitate production management and product traceability, the panes are marked with a unique, machine-readable QR or data matrix code (and often a logo) before being cut to size. Marking the glass using the UniColor laser printing process, for example, leaves the surface undamaged and permanently bonds the marking to the pane without scratching it.
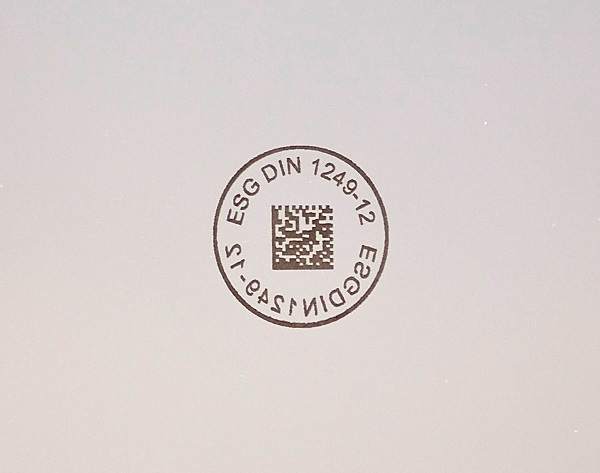
This individual marking allows the entire production process to be monitored in real time and optimised using special software. Depending on backup procedures and the data available, it is possible to track down the production company that made the IGU and the company that installed it for the end customer years later, as well as the stations and machines used in the production process.
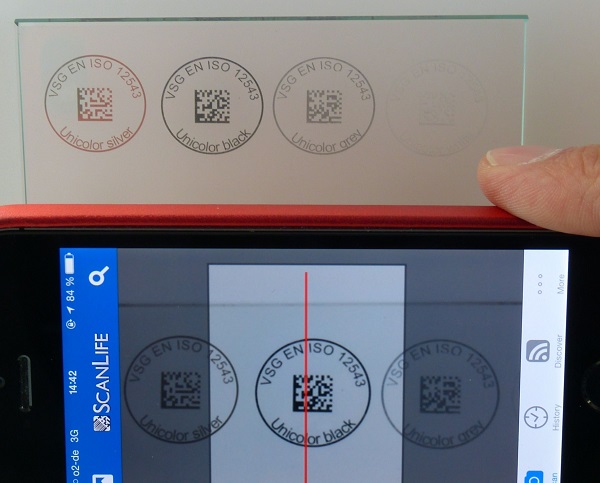
“It’s always good to be able to clearly identify a pane of glass in case of returns – especially in construction projects with multiple pane suppliers,” HEGLA boraident’s authorised signatory insists. Data collection and storage also provides everyone involved with a wealth of experience to draw on. “All this information enables us to evaluate the individual production steps in even greater depth and work with the software providers and machinery manufacturers to optimise our processes, for example,” says Dr Rainer.
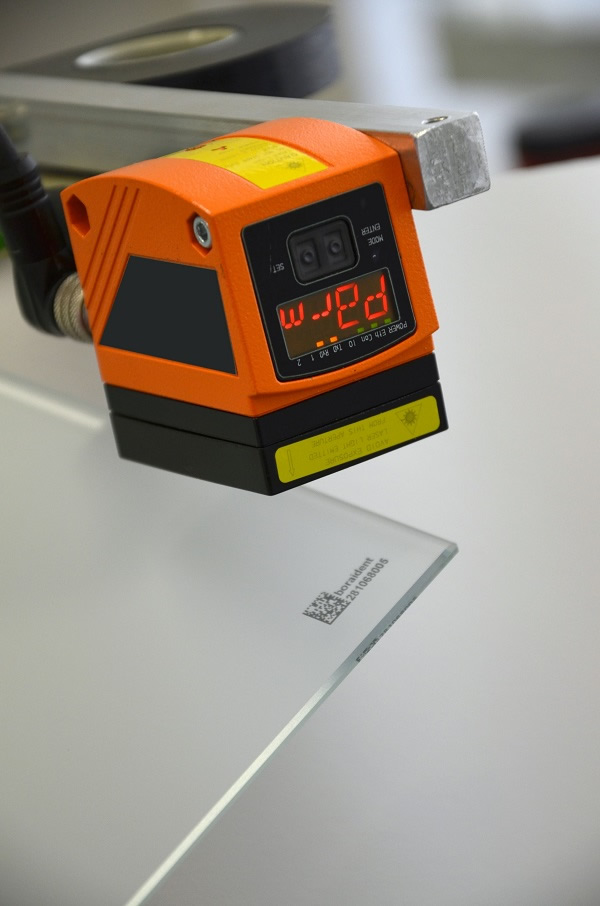
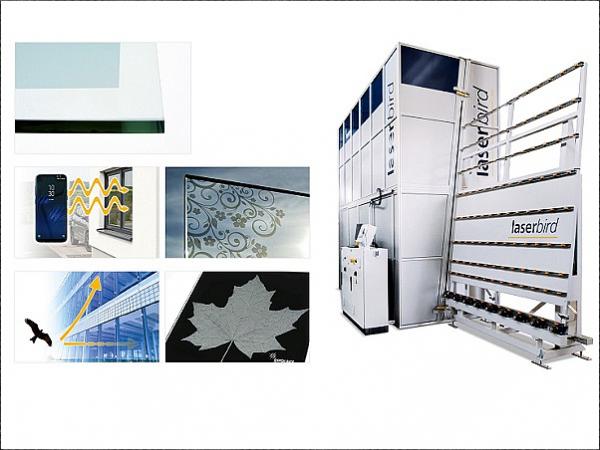

Add new comment