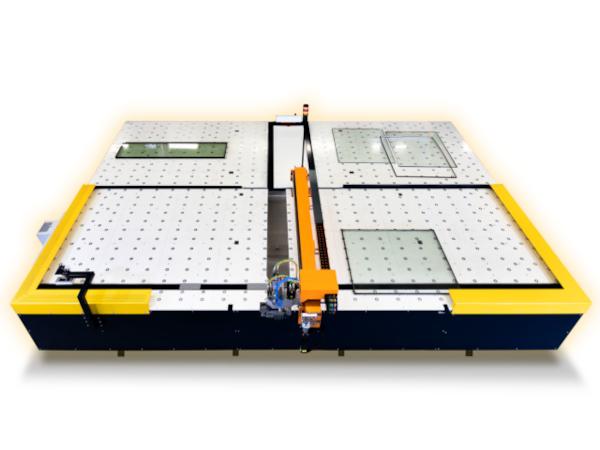
Date: 25 June 2024
The legal objectives have been defined: the EU aims to be climate-neutral by 2050, Germany by 2045. With IG2Pieces, HEGLA is presenting a system solution at Glasstec that can contribute to the required CO2 reduction in the flat glass processing industry. While many climate protection measures are otherwise associated with high costs and time expenditure, the system for separating insulated glass not only saves valuable resources, but also generates financial added value for customers.
Added value by type
The recycling of glass is a success story that is based on the high quality of the raw material: with the right purity, glass can be reused almost indefinitely. While quotas of up to 90 percent have already been achieved for container glass in some countries, there is still further potential for flat glass. However, the quality requirements for the material to be melted down are significantly higher and often mean processing for recycling is not economically feasible. While mixed-glass containers with partially unseparated insulated glass were previously the common solution for disposal, the provision of the individual raw materials by type offers economic advantages. “With the IG2Pieces separation solution, it was therefore our qualitative goal to separate the units cleanly and safely and to preserve the components undamaged,” explains HEGLA Managing Director Dr Heinrich Ostendarp. “To maximise efficiency and productivity, the focus was on short cycle times with maximum process reliability.”
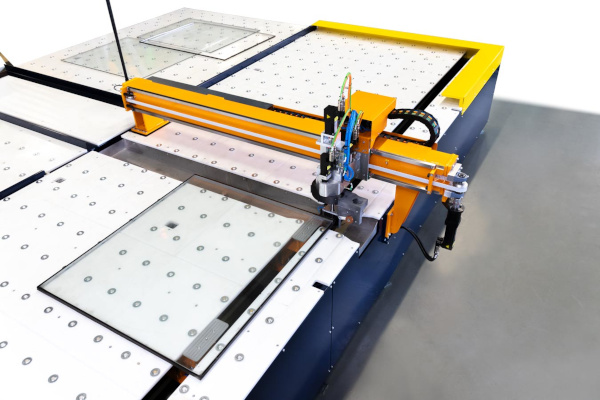
Automatic processes for separation
As the basis for fully automatic separation, the insulated glass is measured in a horizontal position by the system and the structure analysed. In the meantime, the operator can place the next pane and prepare it for separation. “With the new separation process, we have created a technical solution that automatically separates insulated glass into its components and leaves very little sealing compound on the glass,” explains Dr Heinrich Ostendarp. The panes remain undamaged, as does the spacer with its desiccant.
Separate recycling promises quick financial success
Once the individual components have been separated, there are various options for utilising or recycling the obtained raw materials. The data from the measurement of the insulated glass can be used for this purpose. In addition to the length, width and thickness of the panes, this also includes the possible presence of a coating or composite safety glass. “The suggestions and wishes of many customers have been incorporated in the development. And various applications have emerged in the process,” explains Dr Ostendarp. In economic terms, separate recycling of the individual types of glass promises the fastest financial success. If the panes are separated accordingly, the purchase prices from the disposal company are higher. This practice has a positive effect on the visual quality of the subsequent end products, which can be produced unmixed and without impairment. The recycling circuit is closed and the glass finds a new use in the float tank. The environment is a further beneficiary of this recycling process: for every kilogram of float glass produced from recycled glass, CO2 emissions are reduced by around 0.3 kg and can have a positive effect on CO2 certification.
Reusing glass saves even more energy and glass
Reusing glass is another option, especially for large-format, expensive or special panes. “Rare coatings, glass types or optics are always an issue when it comes to new glazing or repairing existing fronts,” says the HEGLA Managing Director. In these cases, IG2Pieces makes it possible to separate an IG unit and then remanufacture it for reuse. The intervention in the building is not recognisable and the architect’s original facade remains intact. If the pane is not immediately required in its original size, it can also be used for cutting into smaller formats. This saves material and can be a pertinent environmental factor for certification, especially in public tenders. “The practice of reusing rare or large panes has been around for a long time,” emphasises Dr Ostendarp, “but this manual process was economically dependent on the speed and dexterity of the respective specialist.” In addition, the use of glass for less demanding applications, such as shelves, can also be an attractive option.
Repair during ongoing operation
Time and again, IG units become damaged only during production. This is all the more annoying when panes are bought in or are expensive. The system technology offers the option of separating the finished insulating unit and replacing the defective component, particularly in the case of supplied panes with corresponding delivery times.
The first systems are about to be delivered and are being used by customers for a wide variety of purposes. “IG2Pieces enables the reuse of raw materials through automation and process reliability, and contributes to CO2 reduction and the sustainable use of glass and energy, in terms of a circular economy,” emphasises Dr Ostendarp.
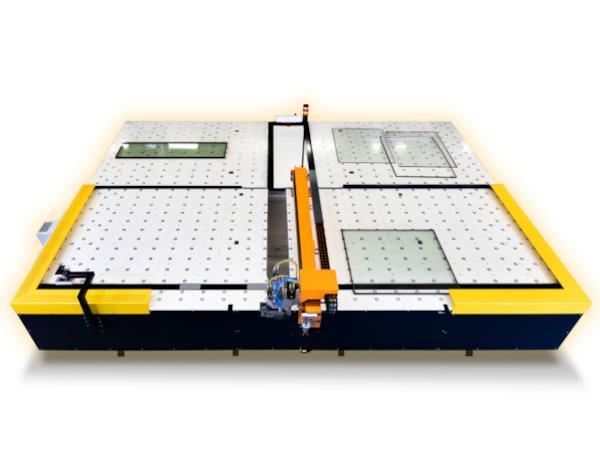

Add new comment