
Date: 19 October 2023
Such solutions are normally rolled out gradually and their implementation depends on whether only a product ID is to be produced on the profile initially or rather, data access is planned immediately.
“Basically, a laser ID can be created at any time during production,” explained Dr Thomas Rainer, head of development at HEGLA boraident, the laser application specialists. “However, to enable the full potential to be tapped at later expansion levels, the laser system should be integrated before cutting in the bar machining centre.”
In a simple basic application, a laser is used to create a logo on the surface that is permanently bonded to the profile as a proof of manufacturer. Customers can use it to quickly find their contact in the event of a service case or re-order, and a clearly detectable origin is also beneficial when it comes to projects with several suppliers. For the visible presentation of other information, the marking can be custom-tailored using text, numbers or graphics.
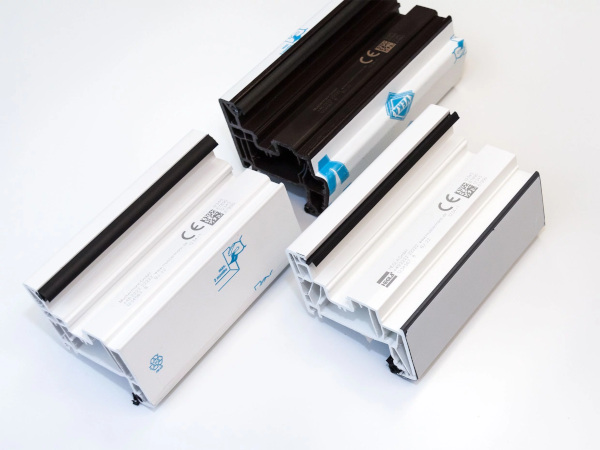
The profile is digitally linked
For digital tasks, the profile receives a unique identity via a QR or data matrix code. “Most ERP software assign an ID that is saved in the system to each production piece when inputting the order,” said Dr Thomas Rainer. “If the number is stored in a QR code, for example, the profile can be identified via scan at any time and depending on the data concept, it is possible to access the ERP information.”
Once the profile has received its personal ID with the code, other product-specific applications can be leveraged. For example, production progress can be recorded at the processing stations in real time via stationary scanners or mobile device and therefore, tracked. The production managers receive detailed information on the target/actual state of production and are supported with sound data in planning or making workflow adjustments. The more data made available by scanning and tracking over an ever longer period of time, the more in-depth information is accessible for analysing and optimizing workflows. Even years later, it is possible to track which profile was processed on which system at which point in time.
Alongside their function as pure identification, markings can be used to control active production. Via automated or manual scan and without the risk of confusion, it is possible to initiate the relevant production step directly on the line, show data to operators or write shipping documents.
Identification offers additional functions in terms of integration into value creation processes outside of classic production. Directly on the construction site, fitters can acknowledge delivery via scan, call up the installation position on their smartphone, update a complaint or have the completed work confirmed. If customers also receive custom-tailored or limited access, a fire protection certificate or service contract can be stored.
Benefits result from excellent scan quality
For all applications with laser marking as a link to saved data, the visual quality of the ID must meet strict requirements. “The digital benefits are the result of automated, reliable scan quality,” emphasised Dr Thomas Rainer. “A high-resolution marking with clear contours and high contrast ensures that marking and scanning functions consistently and with process reliability under a range of working conditions.”
As compared to conventional CO2 laser marking, the WindowMarker process from HEGLA boraident transforms the surface and removes almost no material. The identification can be applied anywhere – typically it is on the outside of a window sash or on the inside of the frame, where the marking cannot be seen when the window is closed. For long-term, excellent scan quality, the size of the machine code (QR or data matrix code) should measure at least 10 mm x 10 mm.
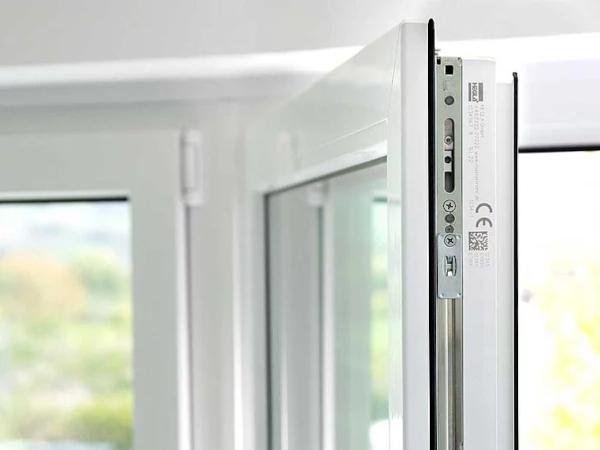

Add new comment