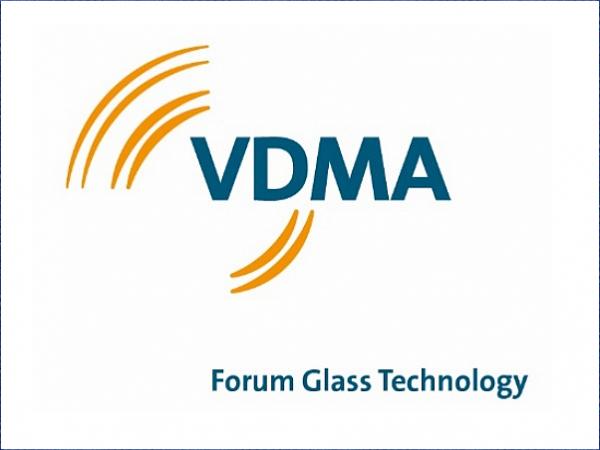
Date: 20 April 2020
Multifunctional glass has a fascinating range of uses, yet is challenging to produce. Modern architecture and some industrial sectors today are unimaginable without it. Coatings and textures allow the glass to fulfil multiple functions simultaneously, but these demand additional steps in production. New technologies are helping to shorten processes and increase productivity.
The core challenge in producing thermal insulation coatings is the size of the substrate to be processed, combined with the need to maximise the system service life and reduce maintenance times. Grenzebach Maschinenbau GmbH has now opened a coatings laboratory to develop solutions for the panes, which can be up to 3.4 m in width.
Coatings can be applied for high-end products, from dielectrics such as silicon nitride and titanium dioxide to ultra-thin metal and blocker layers like silver and nickel chromium, and even transparent conductive layers for use in the display and solar industries. Tests in this laboratory can answer a variety of questions, such as how to apply silver layers to thermal insulation glass while also extending the service life of the system.
In order to minimise shutdown and maintenance times, digital solutions support the production process. The IIoT platform SERICY developed by Grenzebach controls all the processes of coaters and peripherals in production, the warehouse and shipping. The data collected can be used to derive continuous analyses and adaptations, which further optimise performance and thus economy. App-supported assistance systems help in this task.
The aim of all this is to offer almost fully automated PVD coating lines. The PVD process is a vacuum-supported procedure for layer removal. The sputter process has a significant effect on layer growth, with the involvement of excited atoms and molecules and/or ions generated in plasmas. This allows manufacturers to produce all coatings on large surfaces, from sun protection applications to high-quality thermal insulation glasses (low-E layer systems).
Grenzebach recently installed a system for an American manufacturer that produces more than 500 km of sheet glass worldwide every day, demonstrating just what this procedure is capable of. The glass is intended to ensure a pleasant temperature and high energy efficiency in buildings. The production line can coat more than 12 million m² of sheet glass with thermal insulation or sun protection coatings every year.
The processing section of the coating system is equipped with eleven process chambers and a range of coating stations, which apply various coating systems to the glass in a precisely defined order. Two of Grenzebach’s three stackers work constantly to add new sheets of glass and remove them at the end of the production line. As the product is sensitive to touch both before and after coating, the stackers are arranged in such a way that they pick up the coated sheets from underneath.
Stacking, coating and unstacking on racks: the entire line covers 9,300 m², or the size of 1.3 football pitches. 110 m of the coating system is under a vacuum, while the section equipped with conveyor technology measures 450 m in length.
No autoclave required
Laminated glasses undergo a complex process. They generally consist of three layers: a glass layer at the top and bottom, enclosing a layer of PVB, SGP or EVA film, for example. An autoclave is used in the standard process, but this is complex and cost-intensive. Robert Bürkle GmbH has developed inline flat lamination – a new multi-stage process that can be used for laminated glass or laminated safety glass, and even switchable glass. Lamination is faster and is flexible in terms of glass structure. Moreover, set-up times are short when switching between different products.
The glasses enter the laminator in batches. As the batches are only formed on the feed belt, the process enables a high level of flexibility. A vacuum removes the air between the layers before lamination, which then begins with a vacuum flat press heated on both sides. Steel plates heated with thermal oil ensure symmetrical and homogeneous temperature input across the entire surface.
Simple glasses such as tempered glass can be processed at a temperature of around 150°C. The effective area is 2,600 mm by 5,000 mm and the cycle time is less than 10 minutes. Lamination of particularly thick glasses can be completed in a second step, thereby reducing the cycle time. Another flat press then cools the laminated glasses and completes the process.
This procedure allows fast and even lamination without overpressure at the edges, which is a particular problem in membrane laminators. Cooling both sides simultaneously under pressure prevents internal tension and deformation. These flat presses are suitable for safety glass, decorative glass, solar modules, and especially multifunctional glasses that are to be equipped with sensor technology or contain functional films.
Bright and warm
Windows and fully glazed tower façades today do a lot more than just letting light into the building. Numerous functional layers meet the requirements of modern working environments and personal preferences. Electrically conductive layers are in just as high demand as self-cleaning surfaces and thermal insulation. Glass that both lets light in and keeps heat inside the building demands a special metallic coating. Manz AG worked with Trumpf GmbH + Co. KG to develop a laser process that makes this surface treatment more efficient for a French glass manufacturer.
The goal was to improve the thermal insulation properties of very large glass substrates while also allowing the greatest possible quantity of light to permeate. Manz has many years of expertise in producing thin-film solar modules. The company was therefore responsible for the conveyor line with consistent synchronisation, the high-precision kinematic control of the laser optics including all sensor technology and inline measurement technology, and the overall integration of all individual components to form a system ready for production. The glass manufacturer integrated this into its production flow, downstream of the inline coating system.
Eight line optics arranged next to each other make it possible to process the glass sheet running underneath at a width of 3.30 m. Twelve laser sources with 12 kW of power each feed into the line optics, which Manz has constructed as a bridge across the width of the conveyor line. A continuous laser line across the entire width of the glass sheet requires precise control.
The Gaussian width and edge characteristics at each end of the line must be ensured. Homogeneous energy input within the individual lines and the correct focus depth were further requirements for the quality of the products. With a width of less than 100 µm, the laser line only briefly heats a silver coating that is just a few micrometres thick on the glass substrate. The coating thus switches from an amorphous to a crystalline state, thereby enhancing the insulation effect and transparency of the material.
The more constantly the glass substrate, which can weigh up to 750 kg, is transported along the line and the more constantly the laser inputs the energy, the higher the quality of the coating. In order to adapt the system to various products quickly, flexibly and based on the recipe, the line optics are mounted on very stiff, moveable fixtures to ensure the highest level of precision. Cooling units and radiation protection equipment provide the necessary safety.
Important links:
glass.vdma.org/en/
If you have any questions, Gesine Bergmann from the Glass Technology Forum (+49 69 6603 1259 or gesine.bergmann@vdma.org) will be happy to assist.
The VDMA represents around 3300 companies in the medium-sized mechanical and plant engineering sector. With a good 1.3 million employees in Germany and a turnover of 230 billion euros (2019), the industry is the largest industrial employer and one of the leading German industrial sectors overall.


Add new comment