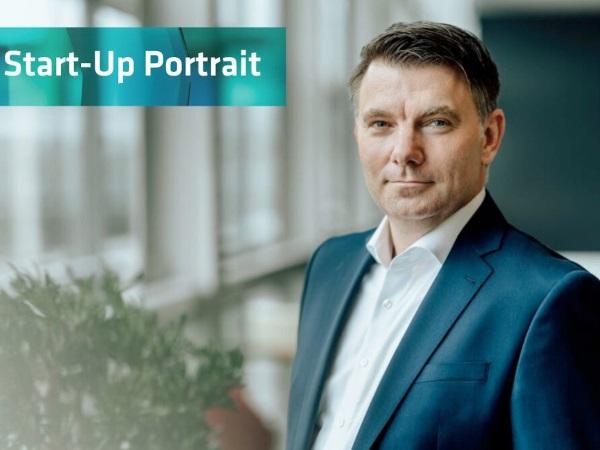
Date: 19 February 2024
Here are some initial insights into their innovative, digital approaches.
Glasstec spoke to Jürgen Huber, Managing Director at BISS.ID GmbH, about his start-up, digital solutions and innovative approaches in the field of digitalisation. An exciting topic that arouses our curiosity to find out more!
First off: What digital solutions does your start-up offer?
Jürgen Huber: “Our focus is on using our platform to simplify data exchange in the construction supply sector, specifically in the construction elements industry. The big challenge here is that despite the many specific software solutions available they don’t communicate with each other. Particularly in the field of construction elements – where every product is manufactured to the highest technical standards, but above all according to custom requirements in terms of shape, material, equipment and colour – every construction element is unique and not an off-the-shelf product. This means the product data is only created at short notice during order-based production. This is precisely where we come in. We want to make this individual product data, as well as data relating to production and delivery, easily available to all subsequent users. We do this via the cloud so anyone with a computer, tablet or smartphone can access the relevant data – securely and protected, of course, depending on their user profile. Manufacturers can transfer data to their customers, who in turn can transfer it to their specialist dealers, fitters or end customers. The cloud environment eliminates the need for software installation, as everything is web and app-based.”
How does the glass industry benefit from your digital solutions?
Jürgen Huber: “The major advantage of our solution is that we operate in an IoT (Internet of Things) environment and can map any type of identification within it. Especially for the glass industry, it is not just product labelling that is important – so here we can also map the entire logistics process starting with shipping from the insulating glass manufacturer as well as the ever-nerve-wracking issue of rack management. In our solution, we can record all of the manufacturer’s racks and it makes no difference to us how they want to record them, i.e. whether they use barcodes, QR codes or NFC- type tags. We link the IDs to the respective rack like fingerprints. What’s more, we can also integrate GPS trackers, either our own or existing ones. This makes it possible to always track the exact position of the racks. The data transfer between the customer ERP and the BISS.ID platform not only synchronises the rack and customer data, but also the order data. This enables digital delivery notes to be generated when the racks are unloaded, including signatures and photos. Full documentation can be made available to the customer as well as the manufacturer. Any service and complaint cases can be triggered directly via the ID of the glass unit and the reference to the product and order is immediately established and documented. All actions can generate emails to various addresses via the notification manager, all automated and archived on the platform.”
What is your vision for the next few years?
Jürgen Huber: “Our vision is for more and more software companies to open up to integrating flexible, innovative solutions. This will benefit the entire industry. No company can solve all the issues on its own. But by bringing together the leading systems from each sector and working with the existing data, we have a chance to use digitalisation in the construction supply industry to a greater extent than other sectors already do. Despite some still open and unresolved issues relating to artificial intelligence, we should also recognise the opportunities offered here, particularly in SMEs and trades-based industries. For instance, it may make more sense to install a web-based language manager rather than to try to teach every employee German by hook or by crook. We can already set up any language centrally in our solution. With this in mind, we are also continuing to expand our platform so we can integrate leading solutions into our portal, like route planning, complaints management and assembly planning. In addition, we have established and continue to establish further partnerships with leading software manufacturers from the glass and window industry who are creating interfaces to our solution.”
To your mind, what economic policy measures are needed to ensure Germany remains an attractive location for (industrial and medium-sized) companies?
Jürgen Huber: “I see the expansion of the digital infrastructure as essential. Be it mobile network coverage or the availability of sufficiently good Internet connections. We can develop good digital solutions, but without fast enough data connections, it will be problematic. Cloud solutions offer many opportunities, especially for the manufacturing industry and SMEs, but also for tradespeople.”
Do you already know what you will be showcasing at glasstec 2024?
Jürgen Huber: “As well as further developing our BISS.ID tracking platform for the digital management and processing of deliveries, we will also be showcasing the newly developed version of a digital fingerprint for insulating glass units. This ID can not only be used to provide the unit with product data and properties, but also to digitally record and control processes in production and logistics, as well as in assembly and after-sales. In terms of sustainability, all components of the part can be identified at any time, which is a big plus for the subsequent recycling of the product.”
And finally: Describe the DNA of your start-up in four words …
Jürgen Huber: Practice-orientated, flexible, sustainable, passionate.
For further information and contact details go to www.biss.id.


Add new comment