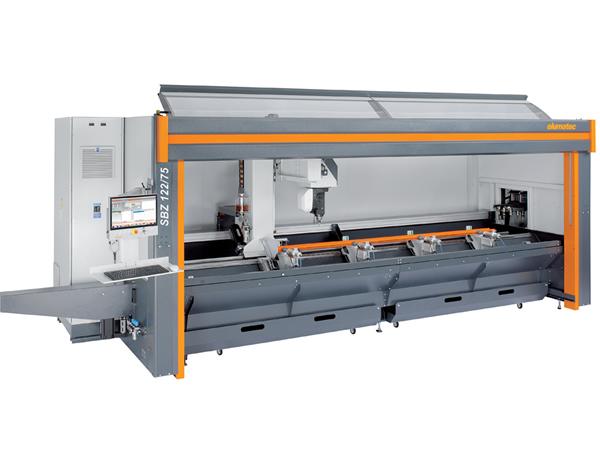
Date: 10 March 2017
This should come as no surprise, as the unit comes with various outstanding features that show elumatec raising the bar once more. In fact, no other system in this market segment offers greater versatility for a broad variety of applications or larger profile dimensions, all while taking up a minimal amount of space.
When customers order a profile machining centre even before production has ramped up, it's clear that there must be something quite special behind it. And that may very well be an understatement when it comes to the SBZ 122/75.
The 5-axis system, which has been designed for window and door manufacturing, is able to machine PVC, aluminium and thin steel profiles with a length of up to 3,300 mm (optionally with overlength machining) and dimensions of 210 x 230 mm on five sides with one single clamping operation.
"This type of machining capacity and versatility is usually found only in significantly larger and more expensive systems", says Achim Schaller, who is responsible for developing the software for the system, when explaining why exactly this system is considered to be a prime example of cost-effectiveness with soaring demand.
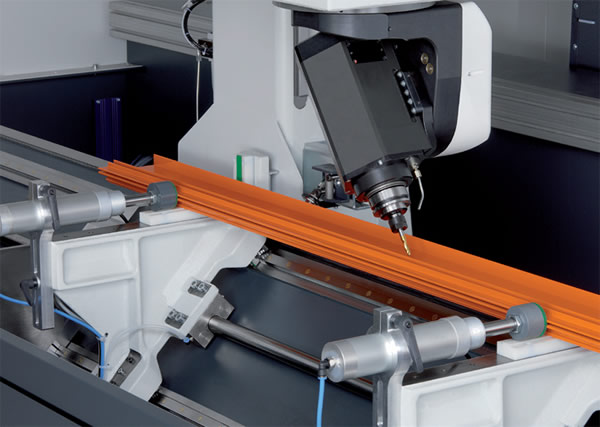
Maximum expansion. Minimal space
A team featuring members from our Production, Engineering, Application Engineering and Sales departments developed the SBZ 122/75 with one thing in mind: our customers' needs and requests. Which also meant there were a few tough nuts to crack.
After all, even though the SBZ 122/75, with an additional A-axis and C-axis, is the largest expansion in the newly designed SBZ 122 family, one of the requirements was for it not to take up more space than the 3-axis centres from the same series.
A challenging engineering problem to be sure, but not one that could not be overcome with a clever platform approach: "Replacing fewer components was the key", reports Dieter Grau, who works at the Mechanical Engineering department.
This translates into an enormous advantage for companies that specialise in window and door manufacturing: They can perform all the profile machining operations they need on a single station that takes up a small amount of space, saves a significant amount of time and features the precision characteristic of all elumatec products.
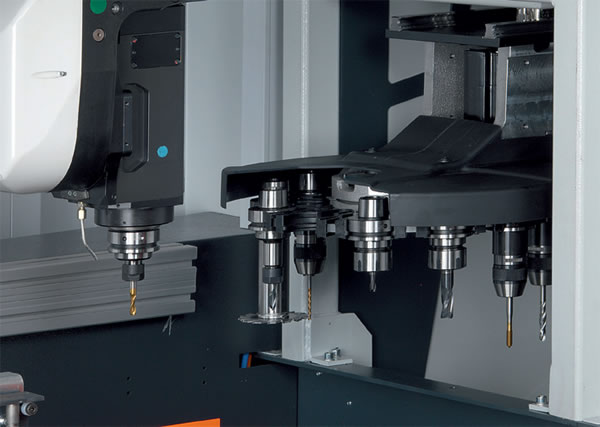
Precise as always, versatile as never before
All five axes can move simultaneously with RTCP (Rotation Tool Centrepoint). Moreover, the additional C-axis makes it possible to machine the face of profiles from the left and right.
Another extra: The two-axis add-on unit with the A-axis and C-axis can also accommodate a saw blade with a diameter of 180 mm, enabling companies to perform all required compound cuts and notches, such as those needed for door spreader bars.
This saw blade is held with the automatic tool changer with the spindle, can be inclined from -120 to +120 degrees and can be swivelled from -220 to +220 degrees with perfect accuracy, including all angles in between.
The router spindle is sized with a powerful 7 kW, ensuring that it can be used for threading, milling and forming operations. Finally, the speed-controlled drive and the use of optimum drive control parameter sets assist with exact and precise handling across a wide variety of loads.
The "overlength machining" option even makes it possible to machine profiles of up to 6,300 mm on the SBZ 122/75. For this purpose, an additional roller conveyor with a stop can be set up on the left side, or two short roller conveyors can be set up on both sides of the machine instead.
"This option is ideal for companies that have to machine workpieces with a length of more than 3,500 mm every once in a while", says Dieter Grau. The machining is programmed for the entire length, with the machine software computing the required part machining operations accordingly.
Changes on the fly
The rotating magazine with a 12-tool changer and the V-axis with autonomous clamp positioning allow for fast, easy setup and minimise non-productive times. In fact, the latter allows for individual or multiple clamps to be repositioned simultaneously even during ongoing machining.
And these features are complemented by a variety of other details designed to enhance productivity, including an inclined machine bed, which was placed 180 mm lower than the standard height of 1,050 mm in order to ensure that profiles can be fed ergonomically, and a height-adjustable control unit.
In addition, the safety hood can be moved back and out of the way in order to make access easier so that operators can work as closely as possible to the profile. The SBZ 122/75 is controlled with the eluCam GUI, which is intuitive and easy to use. Moreover, all inputs are made on a touchscreen with clearly laid out user interface screens.
"Due to the wider range of applications, we expanded the software in order to make it possible to easily enter new machine operations such as complex notches", Schaller says.
In addition, options such as an input wizard make it easy to quickly show new operators the ropes as they are guided through the input menu and assisted by a visualisation of the workpiece on the machine PC so that they can correctly enter required data, such as the profile geometry and the profile machining operations.
This is further enhanced by functions such as a validation check, which comes as standard, and an optional 3D preview, which help ensure that programming will be error-free.
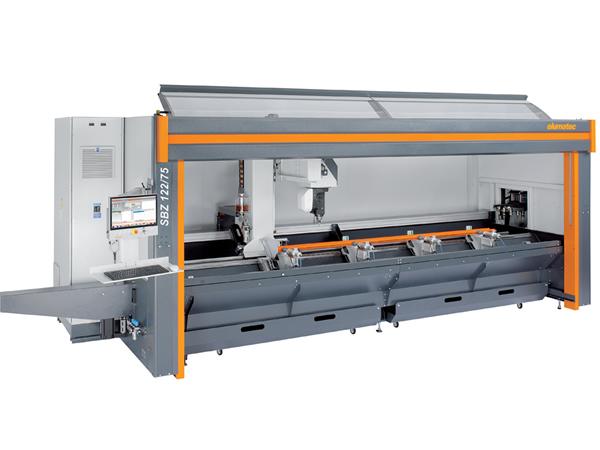

Add new comment