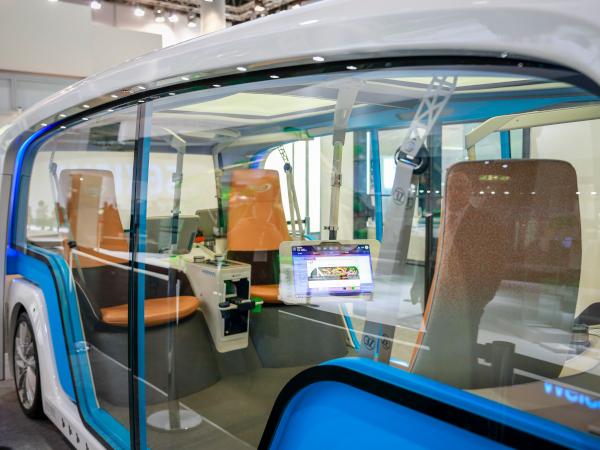
Date: 10 April 2024
Digital technologies and AI are on the advance – also in the glass industry. They hold great potential. Some companies are already using digital and AI tools to optimise products or processes in the value chain.
With increasing digitalisation the glass industry is entering a new era worldwide. Innovation and efficiency can be increased enormously by using digital technologies and Artificial Intelligence (AI). The potential they hold for all segments of the glass industry is vast – from the container glass and flat glass industry to glass machinery building and glass processing and finishing. Possibilities are far from exhausted. The world is currently undergoing a digital revolution – driven by Artificial Intelligence, data analysis and automation. With the help of digital tools processes can be optimised, costs cut, efficiency increased and competitiveness boosted, to name but a few advantages. In a nutshell: digital technologies break new ground in terms of quality, growth and innovation; and glasstec as the world-leading trade fair is right in the middle of it.
Valuable potential by using digital tools
1. Process optimisations by data analysis and AI
Progressive data analyses and AI algorithms can be used to optimise manufacturing processes. From raw material sourcing and manufacturing to quality control, AI-assisted data capture and evaluation enable producers to increase efficiency and reduce rejects.
2. Smart maintenance and servicing by means of IoT sensors
By installing IoT (Internet of Things) sensors combined with learning digital instruments service and maintenance expenses can be minimised – and what’s more – defects, errors or repair needs of machines and technical equipment can be detected early on, avoiding high manpower needs and long, costly downtimes.
3. Virtual Reality (VR) and Augmented Reality (AR) in design and production
VR and AR help to optimise design processes and visualise the finished products faster and better for customers. This applies to both custom “glass” solutions such as container glass design and to customer or staff training. Virtual Reality and Augmented Reality already form an integral part of this industry – and will increasingly do in future.
4. Quality control and inspection by image processing
Extremely advanced image processing techniques and tools are needed to enable machine vision and, hence, an extremely precise quality control and visual inspection of glass products. Defects or irregularities can be quickly detected and remedied this way. This positively impacts product quality and substantially reduces rejects.
These are just four benefits of digital tools but one thing is for sure: digitalisation changes the glass industry and opens up entirely new avenues for many firms – from more efficient processes and optimised production workflows to innovative automation solutions. The use of digital and AI tools is progressing – in the industry just as much as with glass producers and companies involved in the glass cycle, as the following examples of our exhibitors’ use cases show.
Digital technologies as #HotTopic at glasstec 2024
Look forward to glasstec from 22 - 25 October 2024 where under the Hot Topic “Digital Technologies” further approaches will be presented by exhibitors and experts from the industry as part of glass technology live or the glasstec conference.
Four use cases for the successful deployment of digital tools in the glass industry
Case 1: Şişecam improves the colour quality in glass production and optimises carbon emissions with Artificial Intelligence
Şişecam is a leading Turkish producer of flat glass, glassware, glass packaging, automotive glass as well as glass fibre and is a key global player. With its pioneering Glass Color Optimization Project (CROP) Şişecam shows how Artificial Intelligence in combination with machine learning can not only improve the colour quality but also reduce carbon emissions. Using advanced algorithms and machine learning the system automatically identifies colour differences in the production process. This improves the colour quality while reducing production waste – and, hence, carbon emissions. CROP aims to create an infrastructure to quickly identify and eliminate colour differences. The root causes for colour issues are to be quickly found and removed with the help of AI models to thereby minimise undesired colour differences.
Case 2: Saint-Gobain enhances its digital solutions portfolio to accelerate its customers’ decarbonisation
Saint-Gobain, a world-leading company in the field of lightweight and sustainable construction, develops, manufactures and distributes materials and services for the construction and industrial markets. In January 2024 Saint-Gobain announced the acquisition of another specialist for digital solutions. The advanced control systems and simulation software of the acquisition candidate make it possible to reduce energy consumption in glass furnaces. Closing of the transaction is subject to antitrust approvals and is expected by the end of the first half of 2024. Saint-Gobain’s digital solutions form part of their strategic plan “Grow & Impact” which aims to offer customers end-to-end solutions and accelerate the decarbonisation of their products and processes.
Case 3: AGC and Citrine Informatics cooperate to develop new glass technologies using AI
AGC Glass Europe, the European market leader for flat glass and the technology platform Citrine Informatics are cooperating in the field of Artificial Intelligence (AI) to accelerate the next generation of glass. After all, there is great demand for the optimisation of optical and mechanical properties of especially scratch and abrasion-resistant glass in both the automotive and communications industries worldwide. The cooperation is expected to give rise to innovative solutions that satisfy this demand for increasingly performant glass. The Citrine platform derives independent AI models from the AGC measured data and then gradually tests the proposed materials. Citrine improves these models using sequential learning processes oriented towards identifying the ideal process conditions for producing high-performance glass. This kind of AI-based material development is the future of the material industry.
Case 4: BISS.ID promises gapless digital product labelling, rack management, product tracing and documentation
The up-and-coming innovative Start-Up BISS.ID offers a platform that simplifies the digital data exchange in the construction supplies and construction elements sectors. Manufacturer’s individual product data is to be made easily available to business customers, specialist retailers, installers and end users in a cloud-based IoT environment. The big benefit for the glass industry: this digital platform makes it possible to map the product labelling complete with rack management and the logistics process starting with shipping from the insulation glass unit manufacturer. In addition, GPS trackers can be integrated, the data transfer of rack and customer data can be synchronised, order data exchanged and digital delivery bills can be generated complete with full documentation. BISS.ID wird 2024 in der Start-Up Zone der glasstec dabei sein.
BISS.ID will join the fray in the Start-Up Zone at glasstec 2024.
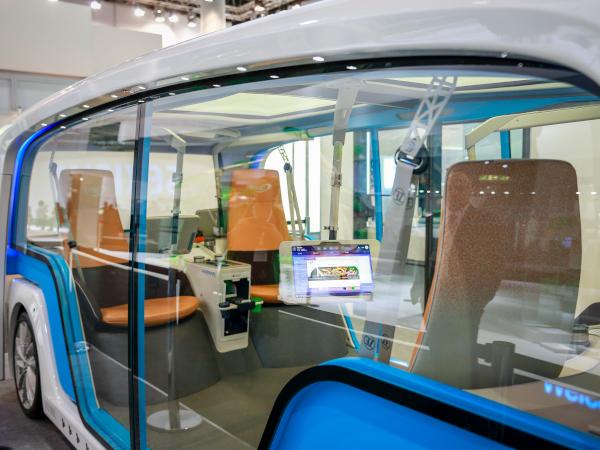

Add new comment