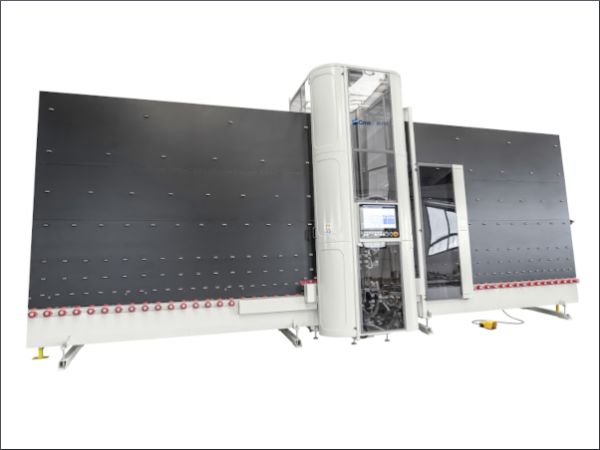
Date: 18 September 2024
In Normandy, near Rouen, there is Normanver, a French company that has been a leader in the glass sector since 1986, with a wide range of action in northern France.
In their factory they work and produce many types of glass from the beginning to the end of the production chain: flat, safety, tempered or laminated glass, insulating glass with thermal or solar control and decorative glass.
We first meet Tony Binard, president of Normanver since 2003, who explains to us how fundamental it is for them to be able to guarantee their customers the highest quality of their products, and tells us how they have moved away from the concept of volume production and have approached production of smaller quantities, but with a significantly higher level of quality.
DRY SEAMING BEFORE TEMPERING
With this idea in mind they turned to the solutions proposed by CMS and this led them to purchase an aura, the vertical dry seaming machine from CMS which "really corresponded to our needs", as Tony Binard claims. In Normanver we needed "a dry seaming machine that would allow us to offer solutions for both double glazing and tempered glass".
The important use of aura in the Normanver production chain is the dry seaming of glass, a process that allows the edges to be finished precisely and cleanly, removing the sharp part left by cutting the glass sheet. The big benefit of seaming is that these glasses, once processed, are directly inserted into the oven for the tempering process, thus guaranteeing greater resistance and safety of the final product. Dry seaming is essential to prepare the glass for heat treatment, ensuring that each piece meets the high-quality standards required by Normanver.
VERY LOW MAINTENANCE AND USE COSTS
Aura requires little maintenance, low running costs and is very simple to use. A big benefit comes from the fact that the tools do not require water to function. This saves both on water consumption and on the cost of purification systems.
Aura is equipped with four operating groups, each made up of two heads for seaming the four sides of the glass and each head is equipped with a flap disc tool designed for dry working. To better manage the suction of glass dust generated during processing, aura has a system of pipes that conveys dust to the back of the machine into a multi-stage filter, leaving the work environment clean and safe.
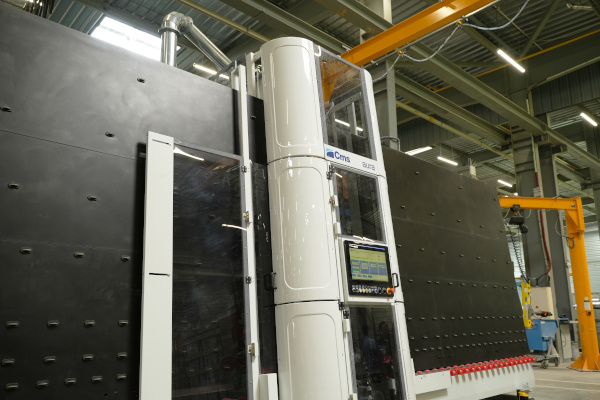
SIMPLE AND FAST
We go into more detail about glass processing with the dry seaming machine with Martial Millard, who deals with glass processing in the company and who seams glass with aura every day.
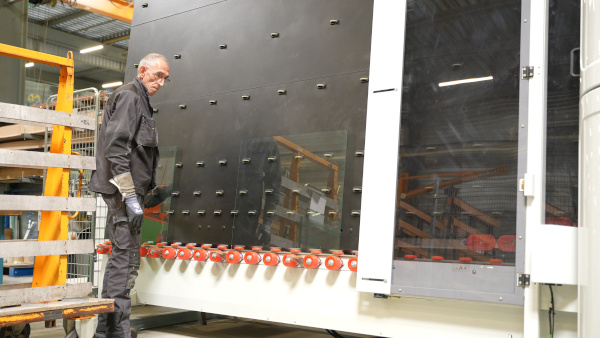
Martial is satisfied with how Aura has made his work easier and faster thanks to the automation of the process of recognizing the dimensions and thickness of the glass once loaded into the machine. “I can take any glass of any size and thickness, one after the other and everything is automatic!” he says smiling. In about 15 minutes he manages to dry fillet a series of 50 pieces of glass!
Aura can seam 1x1 m glass in 18 seconds and can be used as a single machine, in line with a vertical washing machine or in an insulating glass line.
ZERO THOUGHTS FOR THE OPERATOR
“At the software level, it handles everything!” continues Martial, “It's an incredible software, I don't have to enter parameters such as height, length, thickness. You position the glass, the sensor reads it and understands what it is like and then it goes."
Today aura is well integrated into the Normanver production chain and has contributed to bringing superior quality to their products while also responding to the most particular needs of their customers.
“We quickly oriented ourselves towards CMS”, underlines Tony Binard, “because it gave us a technical solution in line with what we needed”.
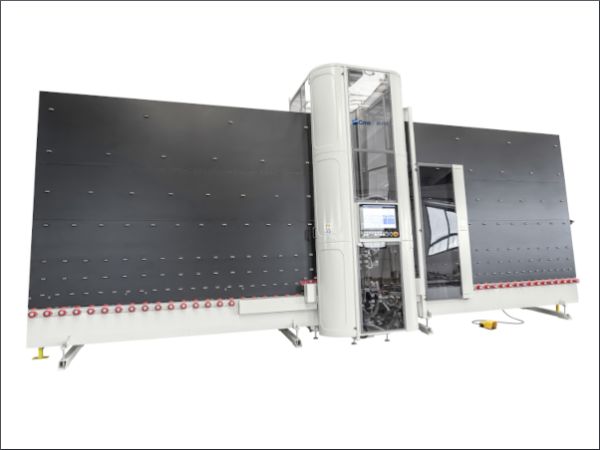

Add new comment