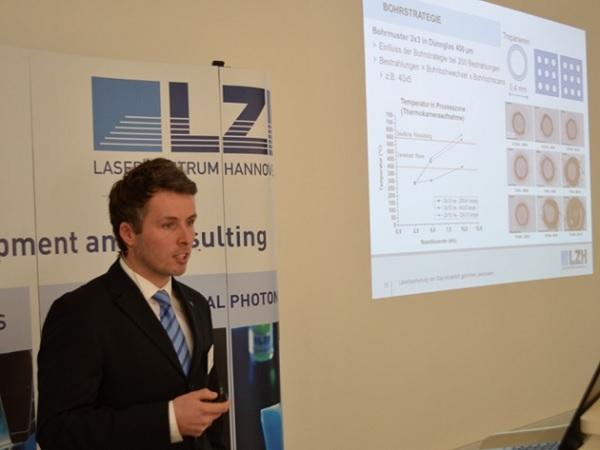
Date: 19 December 2016
Considerable progress in process technology and automatability has opened up many new perspectives - both technically and economically.
More than 70 manufacturers, users and scientists saw this for themselves during the event that was organized in cooperation with the Bayerisches Laserzentrum GmbH (blz).
Today, laser-based glass processing is state-of-the-art in many industrial sectors. But still this technology field is highly dynamic.
Innovative process technology and systems are providing further important improvements in the processing of thin, flat and tubed glass for the future.
Processing results can now be predicted more and more accurately by numerical simulation. "The models have reached such a high degree of maturity that the simulations are very close to reality," said Prof. Jörg Hildebrand of the Technical University of Ilmenau.
In addition, the correlation between the wavelength and welding seam quality has been demonstrated for ultrashort pulse laser welding (USP) welding.
And in the field of separation processes, hybrid approaches with laser and plasma radiation have proved to be a promising topic for the future.
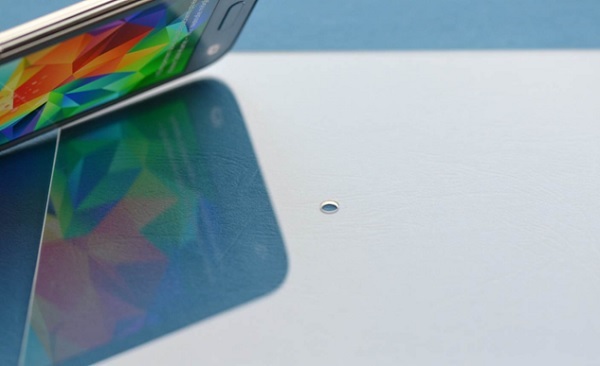
Major step forward in thin glass drilling
In order to optimize the laser drilling of thin glass, the team of Philipp von Witzendorff, Head of the Glass Group at the LZH, has developed a novel drilling strategy: "Our goal was to avoid edge chippings completely - and we have succeeded. We combine single pulses with different pulse durations.”
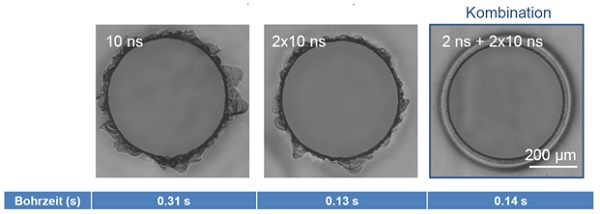
Lower unit costs with laser technology
Then the focus was on economic considerations. „Commercially available laser systems for glass cutting have not only quality advantages compared with mechanical processes.
They also offer significant increases in productivity due to fewer process steps”, explained Christian Meyer from Coherent (Deutschland) GmbH.
Even when compared with the water jet, the laser is one step ahead: Up to 4 mm thick glass can be laser-drilled for 3 cents cheaper.
The combination of lasers and robots also enables fully automated processes – with high process reliability and without tool wear.
Jörg Zander from Aachen Quartz-Glas Technologie Heinrich confirmed that the increasing automation and the use of lasers in the manufacturing of complex hollow glasses has economically strengthened companies.
He has implemented the results of a project with the LZH concerning the automation of a manual process in a medium-sized enterprise. As a result, the company can now keep up with their Asian competitors.
Valuable impulses for many industrial sectors
"The innovations and further developments in laser-based glass processing presented today provide valuable impulses for chemical process equipment, telecommunications and many other industries," concluded Dr. Oliver Suttmann, Head of the Production and Systems Department at the LZH.
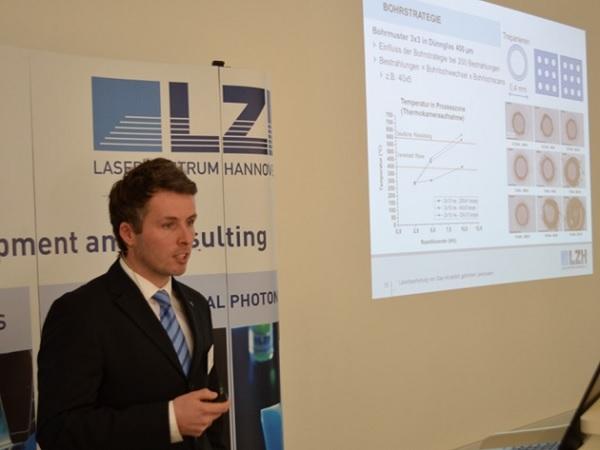

Add new comment