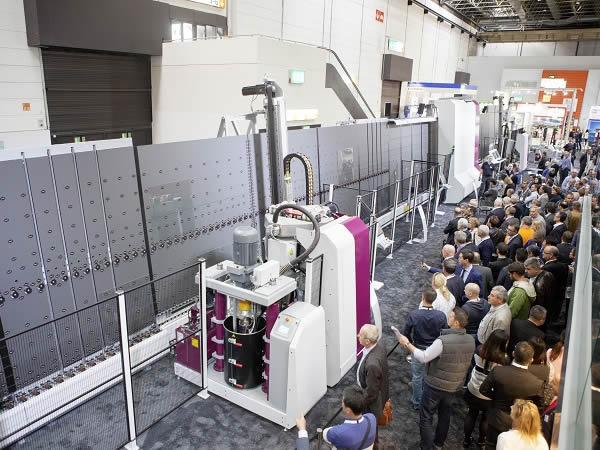
Date: 5 October 2016
LiSEC, the world market leader for plants and software for the processing of flat glass, presented many hits at the glasstec trade fair 2016 – among them was also a completely new concept for the processing of thermoplastic spacers.
The new system is efficient, effective, fast and a real hit also from the outside due to the new LiSEC machine design.
At the leading trade fair of the glass industry, the glasstec, LiSEC presented the TPA line with the Fast Lane concept (vertical lift-over system) for the first time.
The name Fast Lane says it all: sheets which do not require a TPA application are led past the applicator head and are thus overtaking other ones.
At the glasstec show, an enormous crowd of people was interested in the exhibited line; the visitors were able to appraise the benefits of the new plant several times a day:
Application on the Fast Lane
The new LiSEC line contains a unique feature. In order to increase the cycle time, the sheets which are not applied are transported beyond the applicator station.
This is the LiSEC Fast Lane concept: only those sheets are passing through the sealing plant which are actually sealed.
Thus, cycle times of 35 seconds are possible in case of standard triple insulating glass elements, a double insulating glass element needs only 24 seconds which corresponds to a capacity of approximately 100 elements per hour. This does not only save time, but also the investment costs for the second applicator.
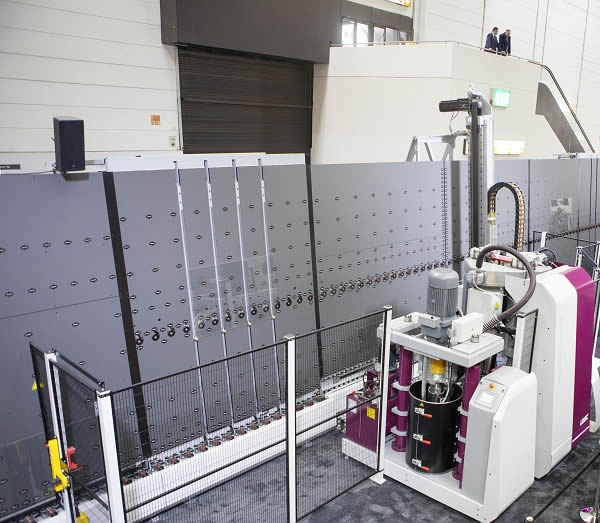
Automatic fully-automatic
The line runs fully-automatically from the cutting (to size) to the stacking of the finished insulating glass units and is monitored and controlled by a control station.
This method does not only ensure a consistent process, it is also ensured that the sheets do not have to be handled manually during the process.
That means: less occupational accidents (cuts) and no defective sheets due to contamination.
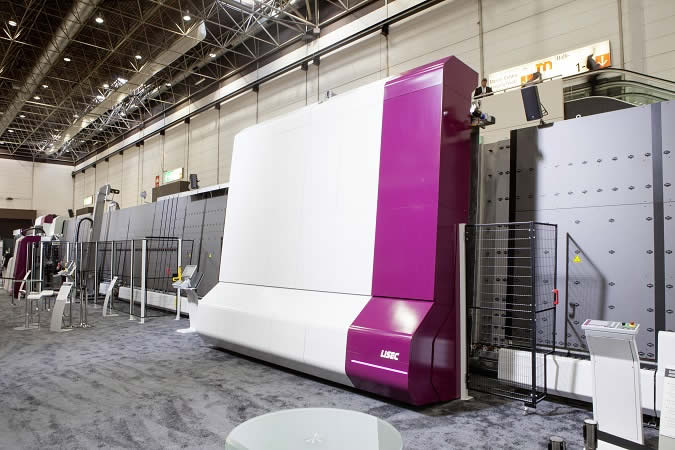
One-Man-Operation
The new LiSEC TPA line with its Fast Lane concept is designed so that only one operator is required in order to control the entire insulating glass line.
The operator’s only responsibility is to monitor that the plants are running and to intervene in case of interruptions.
Compared to conventional TPA plants, the new TPA line is able to produce cheaper by 10 – 15% with the Fast Lane concept due to the faster cycle time and the minimal need for operators.
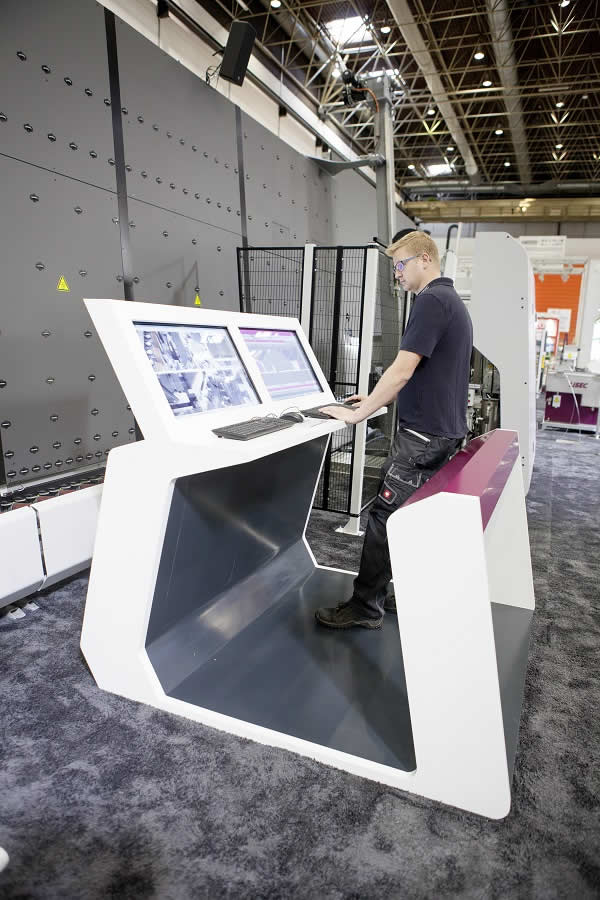
New Design
In case of the new TPA line, LiSEC can not only score from a technical point of view but also in terms of its look, in other words the machine design.
The new design was presented at the trade fair for the first time and it emphasizes LiSEC’s claim: best in glass processing.
When developing the new design, which comes from the Vienna design office spiritdesign, LiSEC has considered the production as well as the assembly: thus, metal sheets were designed smaller in order to ensure an easier handling and the number of colors was reduced.
The Production Process
The perfect interaction of all integrated plants ensures the high speed and process quality. In the first step, the unloading of the harp racks is done sequentially by the automatic unloading station.
Then, the sheets are running through the washing and drying plant and the quality scanner which checks them for their quality prior to the assembly.
The correct sorting of the sheets for the paired and tandem operation of the press is automatically taken over by the vertical lift-over system, a second transport route above the TPA plant.
Here, sheets which do not need any TPA application are able to pass other ones. The elements are assembled and filled with gas in the press and after that they are finished in the sealing plant.
Both the press as well as the sealing plant were specifically revised for the Fast Lane concept.
Maximum quality from the intake to the finished element with an excellent cycle time – the TPA line in the Fast Lane concept is best in insulating glass production.
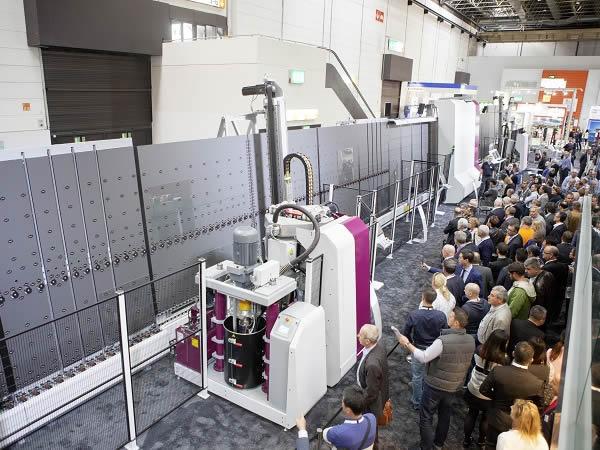

Add new comment