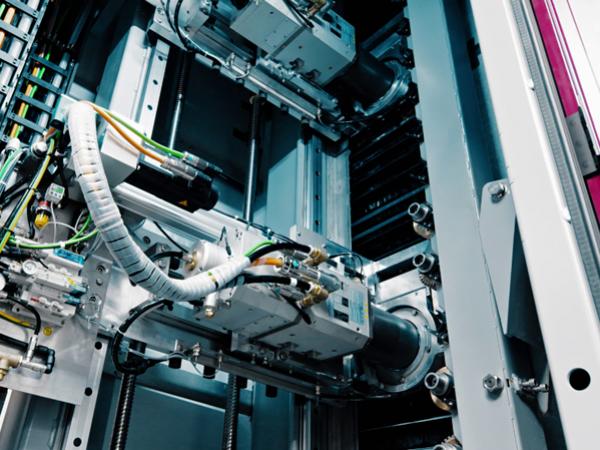
Date: 10 July 2019
In addition to the production requirements for the scope of functions and the commercial calculation, there is another point to be clarified before the final decision is made: What happens if the line stops at an unplanned point?
A smartphone is used on average for 18 to 30 months, a notebook for four to five years. Manageable times, limited costs – that is where a faulty purchase can be overcome or quickly corrected. The situation is different for large investments. The decision about new machines and systems in industry is a generation project with consequences for the next 10, 15 or even 25 years.
At the beginning of the decision-making process there is, of course, the efficiency of a system: What functions does it offer? What are the throughput times? What are the options for expansion and improvement? And what does all this cost? A lot has changed in this respect over the past ten years. This is because, in addition to pure investment costs, operating costs have become more important.
It is not only personnel expenses, regular maintenance and material wear that are to be mentioned here, but also the question of careful handling of resources such as water and energy or the avoidance of production waste. However, small and medium-sized companies in particular still often lack an important part of the total cost of ownership (TCO): the costs incurred by unplanned outages and the question of what happens to the system at the end of its life cycle.
AVAILABILITY IS CRUCIAL
The world's fastest vertical processing line for flat glass, the LiSEC SplitFin system, enables a higher contribution margin per shift due to its short cycle times and high throughput. But the operating company can only generate this as long as the system runs without restrictions. Any unplanned downtime, on the other hand, would also mean higher failures per hour, which would have a more negative effect on the TCO calculation.
LiSEC therefore not only focuses on high production output, but also on ensuring system availability. The first steps along the way are installation service, training and instruction, so that the function of the system and high quality of operation are ensured from the very beginning. Support during operation is provided by the remote maintenance service, which consists of a combination of telephone and online support.
Remote maintenance is carried out using secure remote services. The corresponding software is pre-installed on every new system and can be used once a remote maintenance contract is concluded. Any access shall be made exclusively with the permission of the client and always under their supervision. A multi-level security concept ensures that only authorised support access to the system is possible.
In this way, an immediate diagnosis can be made in the event of malfunctions, in order to be of assistance directly or by telephone hotline in rectifying malfunctions and errors. The system operator has complete transparency over the work carried out by remote maintenance. The service is available on weekdays 24/5, from Sunday 22:00 hrs until Friday 21:00 hrs (CET or CEST respectively). Outside these hours a weekend standby service can be reached.
WORLDWIDE ON-SITE SUPPORT
If remote maintenance is not sufficient, the manufacturer can offer its customers worldwide on-site support via a service contract. LiSEC serves around 4,700 customer locations in over 100 countries through more than 45 branch offices and agencies, including 20 of its own subsidiaries. The 160 fitters employed here constitute the largest service network in the flat glass processing industry. They ensure that response and recovery times remain low even outside your home country.
Points such as maintenance, service, repairs or spare parts delivery can be agreed in the service contract. In addition, LiSEC offers the optimisation of parameter settings and recipes, functional checks of safety devices and the secondment of specialist personnel.
The regional representatives also ensure a rapid supply of spare parts. Within Europe, customers can choose between the low-cost Economy variant (delivery within five working days) and Express delivery (within one working day). In addition, there is the possibility of ordering Saturday delivery and special transports. LiSEC guarantees the availability of spare parts for 10 years. During this period original or equivalent parts are available.
LIFE-CYCLE ORIENTED
Apart from services for safeguarding or restoring ongoing operations, LiSEC also offers support for retrofits with its Long-Life Service. PC upgrades, drive conversions and similar modifications are developed in a separate department and made available to customers. With modern technological developments, existing systems are brought back up to date. Thus, the system can be modernised without major investments in new machines.
If, on the other hand, you decide to opt for a completely new development, LiSEC will help you to recycle the old system. Glastronic, part of the group since 2016, purchases used LiSEC glass processing machines from customers, reconditions them according to customer requirements and resells them.
LEARNING FROM OUR OWN EXPERIENCE
This service offered by LiSEC has not come about by chance. The machine constructor differs from all its competitors in one key respect: It is also its own customer and therefore knows its own systems and services from a user's perspective. Originally founded as a glass manufacturer, machine construction has since become a central pillar of the company's nearly 60-year history. Nevertheless, the company has always remained faithful to glass production and further strengthened this area in 2015 with major investments.
The Glass Forum at LiSEC's headquarters in Hausmening with a production area of 10,000 m2 has been designed as a LiSEC centre of excellence in which the latest in-house technologies are always used. LiSEC does not only gain experience in production here. Questions that are answered in the Glass Forum also include enhancing the reliability of the systems, simplifying maintainability and which services can be offered. This operator know-how enables LiSEC to develop customer-oriented solutions and the appropriate services.
CONCLUSION: PREVENTING MACHINE DOWNTIME
The day will come on which the machine comes to an unscheduled stop, that is inevitable. The only question is how to ensure that this day is shifted as far into the future as possible, and what happens when it finally arrives. How well are your employees prepared for circumstances that deviate from normal? What is the manufacturer's support like, with know-how, with spare parts, with its own technicians? How good is the expertise, is the time until the first reaction appropriate, and how long does it take until the stoppage is rectified and production is up and running again?
LiSEC provides clear answers to these questions. Competent support from installation to the end of the life cycle, both to maintain trouble-free operation and to minimise unplanned downtimes, the service portfolio covers all areas. However, this is only an offer – it is up to the system operator to decide to what extent they utilise it.
By Filip Miermans
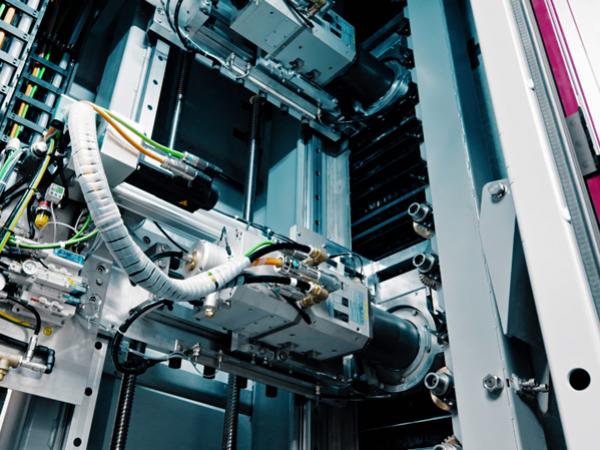

Add new comment