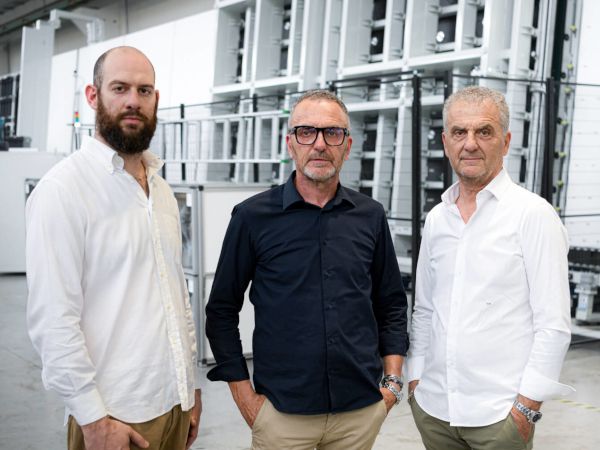
Date: 11 November 2024
Established in 1985 as a small artisan store, Artigianvetro found its roots in Graziano Marcantonelli‘s passion for working with glass by hand. With a workbench and a few tools, he laid the foundations of a business destined to grow rapidly.
A few years later his younger brother Daniele joined him, thus strengthening the team and consolidating the company.
Soon, with increasing orders and a desire to perfect machining techniques, the growth process began, which saw the workshop expand, reaching the big step of building new headquarters.
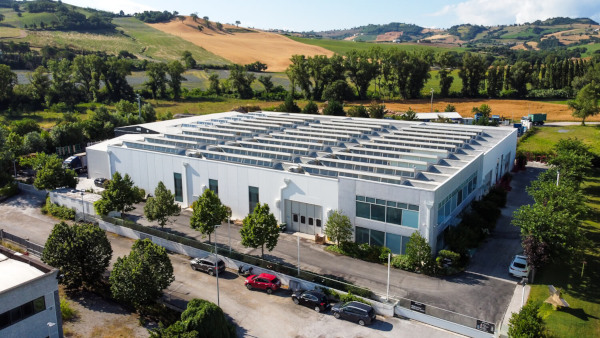
For the real leap in quality in the insulating glass sector, we have to wait only a few years: in the mid-1990s, with the introduction of the first cutting benches, the washing machine and the first Forel flatbed press, investments are made that automate much of the production, guaranteeing ever greater precision and quality. Rapid but gradual growth that rewards the courage and foresight of the Marcantonelli brothers in intercepting the future and investing in cutting-edge technology.
The relationship of collaboration with Forel intensifies more and more over the years, thanks also to the introduction in the glassworks of glass bender, salt loader, sealer and edging machine that, together with washing machine and press, complete a real fully automatic insulating glass production line.
In 2012, following a new location change, Artigianvetro decides to invest again in innovation together with Forel. In fact, a new insulating glass line is installed with two important innovations: vertical grinding machine and automatic flexible profile applicator, among the first plants in Italy.
With the entry into the company of Nicola Marcantonelli, Graziano’s son and current Production Manager, the change of step that leads to the concretization of the concept of Industry 4.0 and the consequent increase in the fluidity of production processes is realized.
It is 2017, the year in which the new Forel system of evolved logistics is introduced in the San Severino Marche glassworks: the Sorting System. The latter makes it possible to significantly increase operator safety, optimize the production flow, increase the level of industrial automation thanks to the modular and flexible control of spaces and, above all, to quickly manage the succession of plates between the various processing lines.
Thus we come to the most recent installation, we are in 2023, Artigianvetro is ready for a Jumbo Line.
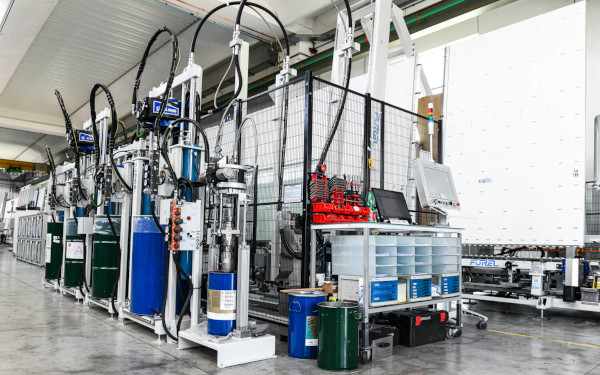
“The decision to invest in a new Jumbo Line matured during 2022, following analysis of market trends that indicated a growing demand for larger glazing and faster delivery times. After a careful study phase with Forel, a long-standing partner known for its ability to innovate, we looked at several options to expand our production capacity.” – Nicola explains. ”Considering we have seen this company always look ahead and grow in small steps, the choice of a new Jumbo line was dictated by the desire to take one more step forward to offer our customers a larger size that we were previously unable to produce.”
In detail, the adoption of the High Tech Jumbo insulating glass line, featuring the flexible T-Shape applicator and the SR HT automatic sealer with the unique non-stop double-bracket dosing system and dual products (polyurethane and structural silicone), has enabled Artigianvetro to improve efficiency and repeatability of results even more. The SR HT’s technology, in particular, ensures that sealing is always centered on the chamber. Its innovative “Special Inset” system automatically ensures normal, partial and retracted sealing on the same double glazing unit whether the panels are aligned or staggered.
Looking to the future, new frontiers of exploration in the field of glass processing are clear at Artigianvetro: technological innovations, environmental sustainability and the relationship between customization and flexibility. The idea is to continue to invest in new technologies that can improve the efficiency and quality of machining processes, gradually including the support of artificial intelligence and data analysis with the goal of optimizing results.
An increasing focus will be placed on environmental sustainability by developing technologies and processes that reduce the environmental impact of IG processing, such as reducing energy consumption and adopting environmentally sustainable production practices. In this regard, the Sorting System has enabled the company to better manage glass waste, anticipating the cutting of defective pieces so as to avoid subsequent downtime during insulating glass production.
Ultimately, tailor-made production must be supported by the ability to be able to propose innovative solutions, pandering to limitations and putting the human relationship of collaboration at the center for each project. It is precisely that human relationship that has marked the bond between the two companies, based on mutual trust and the sharing of common values such as innovation and sustainability, that is the solid foundation on which to build new ambitious projects and investment opportunities.
Artigianvetro is a story of growth and expansion that has rewarded resourcefulness, transforming a small village glassworks into a leading industrial vanguard on the national scene, able to differentiate production between residential and commercial insulating glass, now also in large sizes and thicknesses. An industrial vanguard that remains with an artisan soul. “And the soul is very important, it is fundamental ” – as Daniele Marcantonelli points out.
“We aim to obtain a superior finished product because we are aware that, in order to live in a comfortable environment, it is necessary to have in one’s home glazing that approaches perfection and worked with the utmost care” – concludes Daniele.
The partnership with Forel has certainly been a turning point for Artigianvetro, allowing the company to introduce cutting-edge technologies and optimize its production processes. Thanks to this partnership, Artigianvetro looks to the future with optimism, ready to face new challenges and seize the opportunities offered by a constantly evolving market. The goal is to consolidate its leading position in the area, continuing to invest in order to offer its customers products and services of the highest quality.
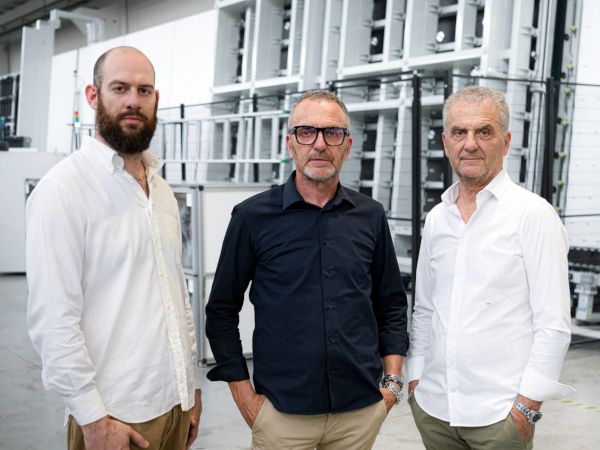

Add new comment