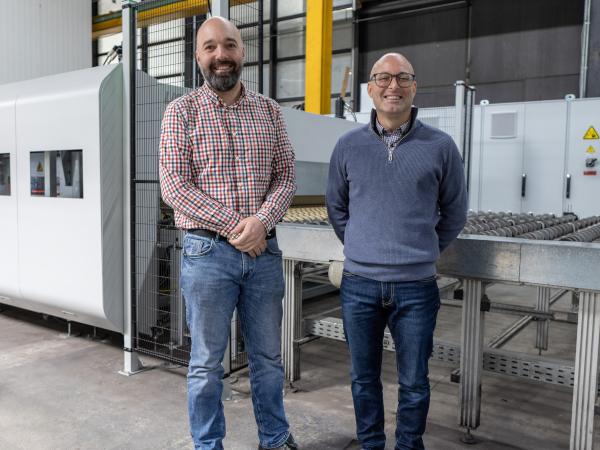
Date: 17 July 2024
Arbonia Glas in Deggendorf manufactures high-quality laminated safety glass made of toughened safety glass, heat-strengthened safety glass and float glass for the interior sector, with rapid delivery times and a high degree of delivery reliability. The company now uses a LiSEC pre-lamination furnace for the final process step – the bonding – which is critical to success: Product quality and energy efficiency.
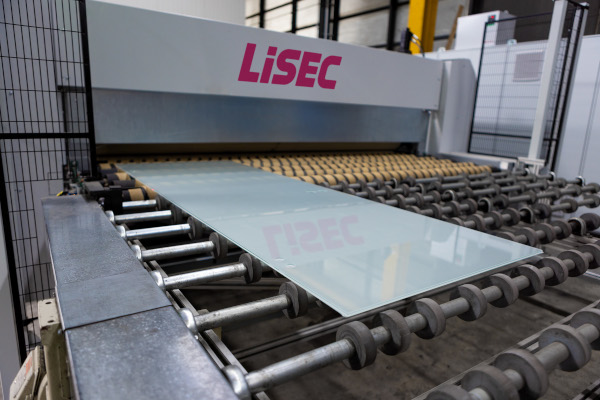
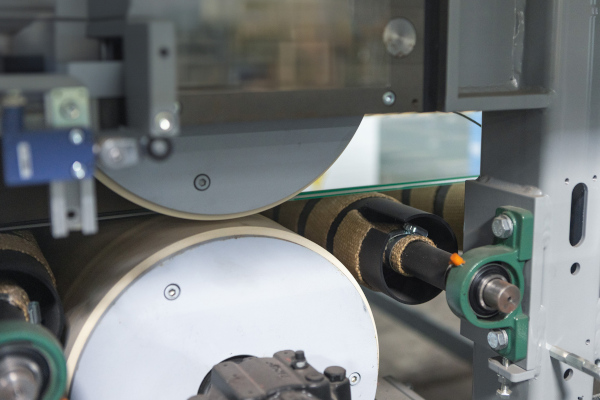
PROJECT GOAL: PRODUCT QUALITY
Matthias Baumgartner, Technical Operations Manager at Arbonia, explains the background to the project: "The idea of replacing the pre-lamination system came about due to the increased energy costs, which are largely incurred in the pre-lamination system in the LSG process. Added to this, our KPI is speedy delivery. Because the LSG process is the last step, it is particularly critical; the glass has already been cut, drilled, contains cutouts and countersinks and is toughened at this point – we are talking about up to five days of production before the glass even arrives at the laminated safety glass line. If we have promised the customer a delivery time of two weeks, for example, we have to get it right first time. Not to mention the labour and energy costs that have already been incurred by the product when it arrives for lamination."
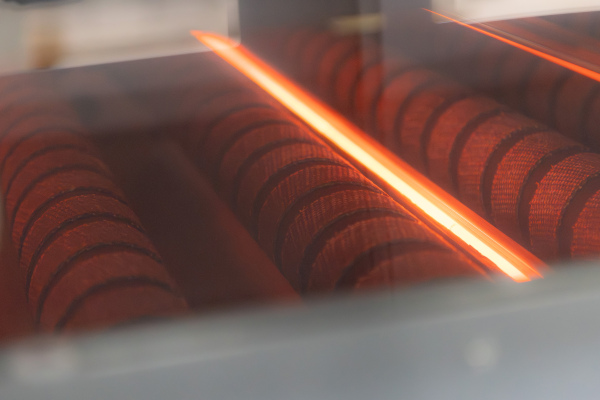
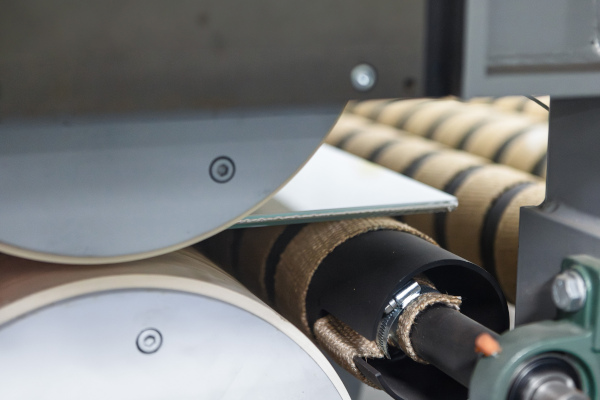
"Customers will only order again if they get what they have been promised." Mr Baumgartner shares his customer service mantra with LiSEC.
While laminating float glass is relatively simple, toughened safety glass can be quite a challenge, as Mr Baumgartner explains: "During tempering, the glass is subjected to stress, which causes it to lose some of the flatness it still had as float glass. We have been looking for a solution that forgives more errors in the tempering process and produces as many good glass lites sheets as possible. Factors such as the optimum temperature, as little air as possible between the glass sheets and constant contact pressure per surface area are crucial."
The LiSEC pre-lamination PNM is designed to satisfy these demands. The foil is heated and then pressed against the glass by rollers to remove as much air as possible from the glass package and create a firm bond between the glass and foil. Thanks to a unique servo spindle drive, it is possible to accurately and automatically meter the pressing force and always press in parallel. To avoid misalignment or breakage, the glass package is pressed on the glass surface and not on the glass edge.
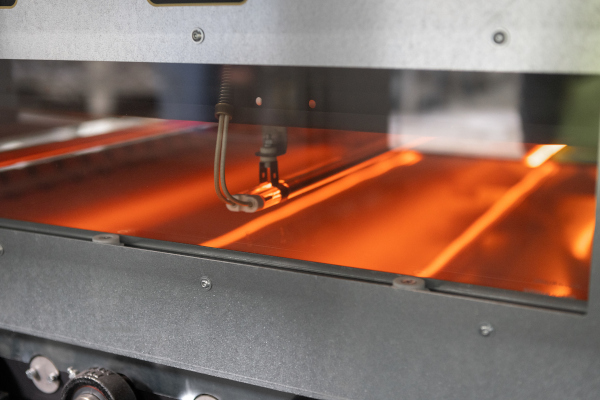
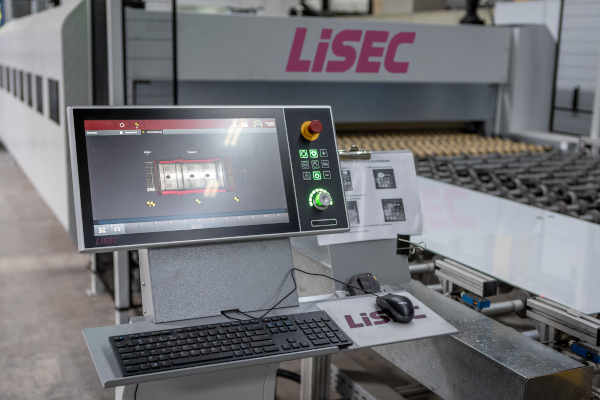
PROJECT GOAL: ENERGY EFFICIENCY
The decision-making process was based on facts and figures, recounts Mr Baumgartner: "Our first step was analysing the energy data and the speed of the existing process. The furnace was a bottleneck, which is why one thing was quickly clear: the throughput per time unit had to become faster and the furnace more energy-efficient overall. LiSEC accommodated us here by providing the requisite data."
Determining real energy consumption values based on specific production data was a challenge that LiSEC was happy to take on. Mr Markus Ensafi, Sales Manager HUB Region North West Europe, comments: "We knew we had to deliver figures that we could guarantee. We are still in the process of establishing ourselves on the market in the pre-lamination sector and are delighted with the confidence shown in us."
A combination of convection and infra-red heaters ensures energy efficiency in LiSEC pre-lamination. The IR heaters are used for thin glass units, e.g. double laminated glass (glass-foil-glass), because the aim here is to heat the foil rather than the glass. This saves time, money and energy. Convection is necessary for thicker glass units, while a combination of convection and radiation is used for coated glass. Low-E, which is located on the top of the glass package, reflects the IR energy, allowing the energy to be introduced from below and through the air around the glass package.
"We liked the idea of the combined system. We had experience with the heaters. Convection brings with it the benefit that less process heat is lost. The excess heat is not dissipated, but retained within the process in the best possible way," says Mr Baumgartner. So is there a discernible difference? "Standing at the furnace used to feel like being heated up by a red light lamp. It is totally different now."
The Eco-Heaters ensure additional efficiency, because the entire width or only half the width of the furnace is automatically heated, depending on the size of the glass. Furthermore, the temperature of the glass surface on the top side and underside is measured after the press. If the glass is too warm, the machine is automatically accelerated; if it is too cold, the transport speed through the furnace is slowed down. This saves energy and ensures the best possible result.
PROJECT GOAL: INSTANT READINESS FOR OPERATION
During project planning, the focus was on replacing the pre-lamination in the shortest possible time and then being ready for operation as quickly as possible. Mr Baumgartner remarks: "Machinery replacement went well, dismantling and assembly ran according to plan. When issues arose, the focus was on finding a solution. The productivity we expected in the first week of production was also achieved thanks to a few spontaneous changeovers." Replacement of the machinery took just four days of the company holiday in December. Production approval was issued at the start of January and final acceptance of the complete modification took place at the beginning of April.
SUMMARY
Mr Baumgartner reflects back on the project: "My advice for anyone looking for a new pre-lamination system would be to: look at the complete package. The complete package that LiSEC offered us is perfectly tuned. We got what we were promised. I was pleasantly surprised by the throughput speed, which in real operation is a little faster than advertised for all thickness distributions. I think many things have been well thought out and cleverly resolved, and we have not yet identified any major weaknesses when it comes to maintenance requirements and accessibility. From time to time there has been a need for minor adjustments for special build-ups, but so far we have found a solution for every requirement together with LiSEC Support. If the system continues to run for ten years like it has for the last two months, I will be very happy indeed."
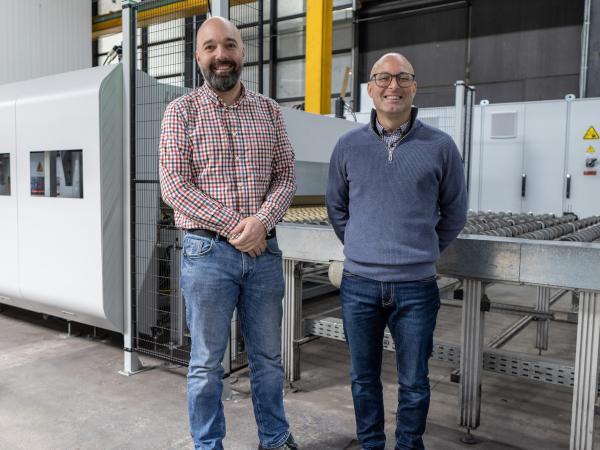

Add new comment