In modern glass production there are also numerous respective developments that have outgrown the research stage. However, there are also other aspects in this respect that we would like to shed some light on in the following article.
Engineering has made enormous advances over the past few years. Machines boast increasingly higher output, they operate more precisely and as a rule consume significantly less energy than just a few years ago. This last parameter is becoming more and more important, especially against the backdrop of sustainability.
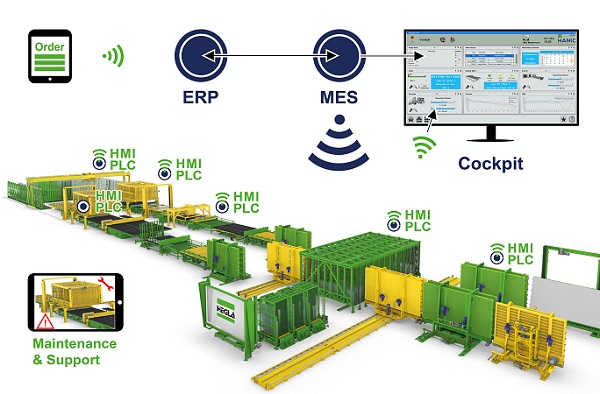
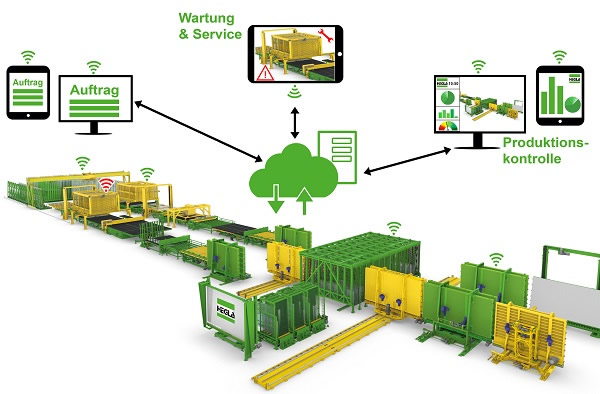
In the course of events new technologies achieve market readiness while other technical solutions become obsolete and vanish from the market. One example of this trend is most definitely laser technology, which was considered exotic and too expensive especially for glass finishing until a few years ago. However, machines became cheaper and more efficient so today they can be economically used for drilling and drill intercepts or for sizing display glass. Even laser-based surface finishing is growing more worthwhile, now offering more possibilities than sandblasting, for example.
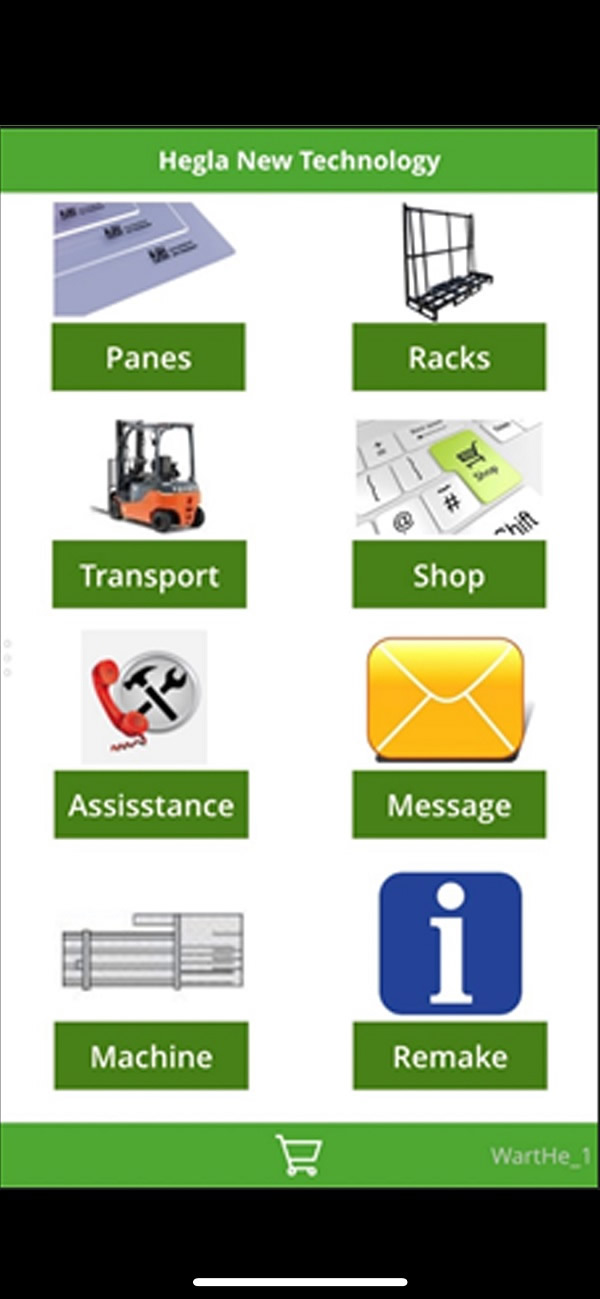
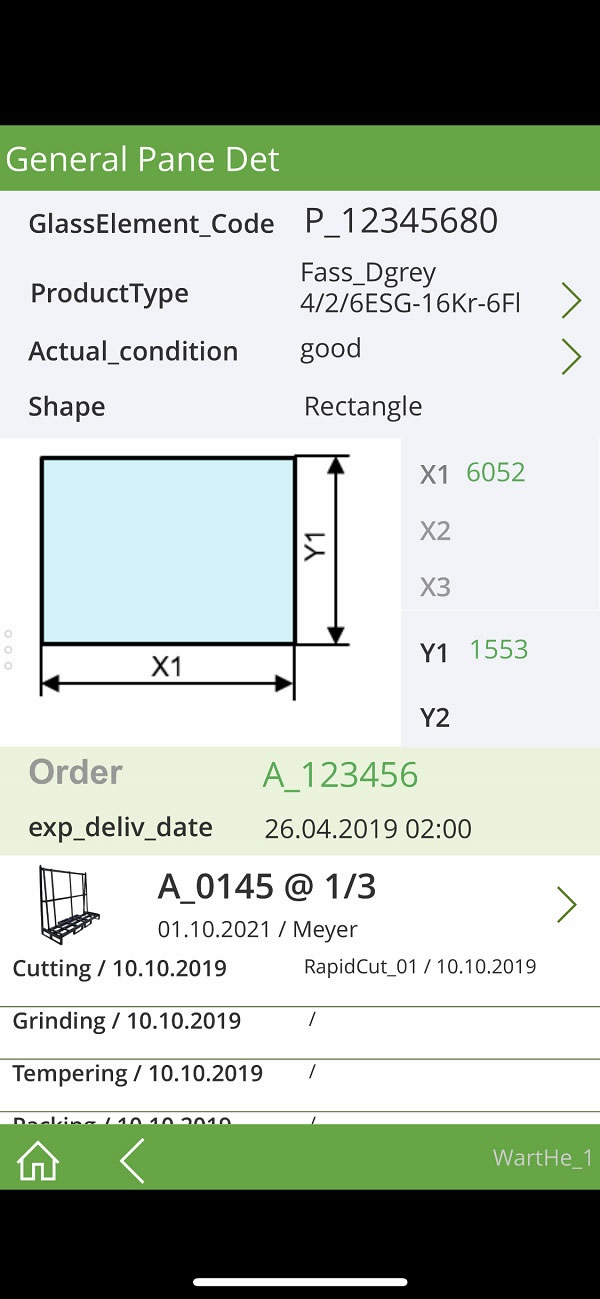
Drastic Digitalisation
While for years automation was in the foreground, the focus has now shifted to other areas thanks to the ever-new possibilities of digitalisation. As a result, manufacturing is reshuffled into a holistic, over-arching process geared to further optimising the transitions and interactions between machines and machine operators, cycle times and material flows.
“So as to fully leverage the potential of this equipment, the tasks associated with, and the correlations of, internal glass logistics in manufacturing must also be identified as the degree of automation rises. The term ‘Shop-Floor Logistics’ aptly describes this change process occurring in classic production: after all, with up-to-date equipment, efficiency in production is no longer decided by machine output but rather by the speed and precise cycle time needed for the glass to arrive at the various finishing stations,” explains Bernhard Hötger, General Manager of the Hegla Group. The volume of glass and great time pressure require a smooth, precise and transparent material flow in order to reduce or avoid downtimes caused by manual handling or missing sheets.
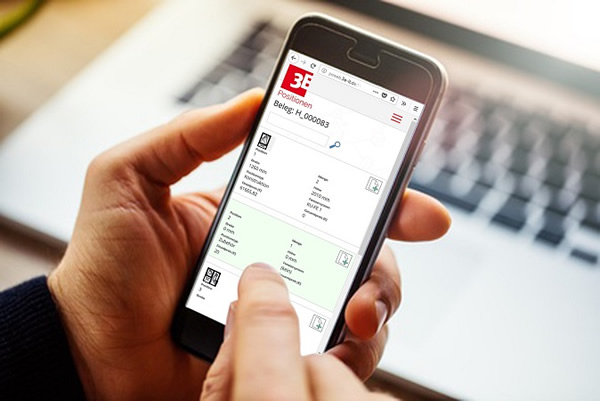
Photo: 3E Datentechnik GmbH
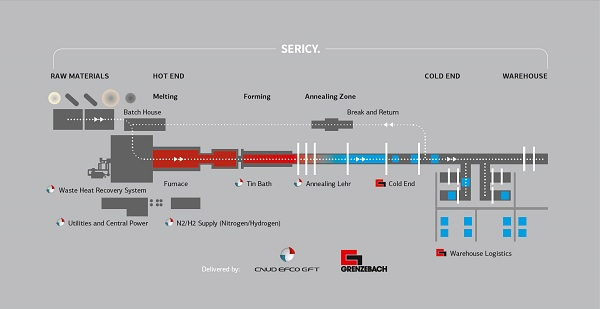
New Challenges for Enterprises
Despite plenty of optimisation and a high degree of automation, companies come up against their limits time and again. One reason is the current labour market because many companies are already today lacking skilled labour. Even though companies’ machinery and equipment capacities are frequently sufficient to process customers’ jobs in theory, the increasing shortage of skilled labour paired with often high demands made on coordination plus rising time and cost pressure causes bottlenecks in many firms in practice.
Digitalisation that ideally covers a complete company promises to bring improvements here. Modern software in manufacturing can – depending on the control concept and integration depth – not only map parts of production but even display individual “slices” digitally and optimise their workflow.
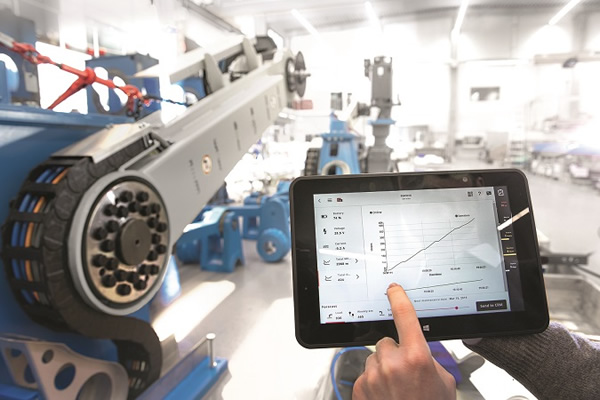
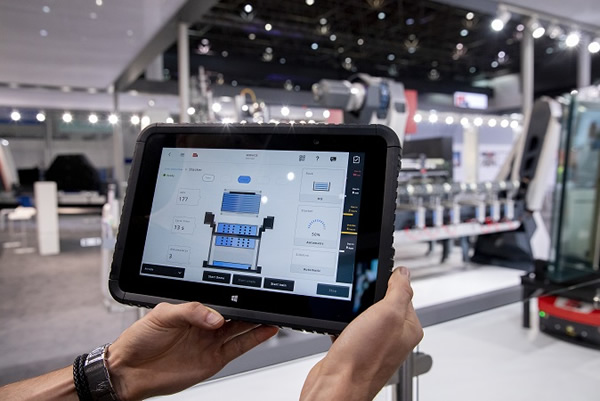
One prerequisite for this is to select, capture and collect the required data and output parameters thereby making them actionable insights. Furthermore, staff on the machine side of the business must be consistently supported in their efforts. This is done by providing assistance for workflow, supplying data for jobs, by control instructions and information on the equipment state or by even more user-friendly and intuitive controls.
As digitalisation and connection increase, additional possibilities for digital support and process control will emerge. Machine operators will be less and less dependent on local data access at the machine or the control panel, and will be able to use an App to trigger a new job order for a damaged glass sheet, find the storage place of a glass rack or establish the downstream process, retrieve maintenance information, report malfunctions or re-order consumables.

In modern manufacturing man and machine virtually work hand in hand. The system sets the cycle in this process and man supports it.
“Of course, this encompasses the complete value chain from the batch plant and furnace, the cold end to the warehouse and downstream processing. In a nutshell: A consistent digitalisation of all processes speeds up the workflow, makes it transparent, thereby ensuring that all required information is highly available at any time,” stresses Egbert Wenniger, Senior Vice President Business Unit Glass at Grenzebach.
Of course, digitalisation does not stop at the company premises. The field team at digitalised companies naturally also has App-based access to all required data when talking to customers or working on site.
Many larger companies have already jumped on the “digitalisation bandwagon”. But there still are many SMEs that view this development with a critical eye. They probably shy away from the associated investment. But just like in people’s everyday lives where digitalisation is on an unstoppable advance, the digitalisation of processes is indispensable for glass manufacturers to remain competitive and future-proof in their business.