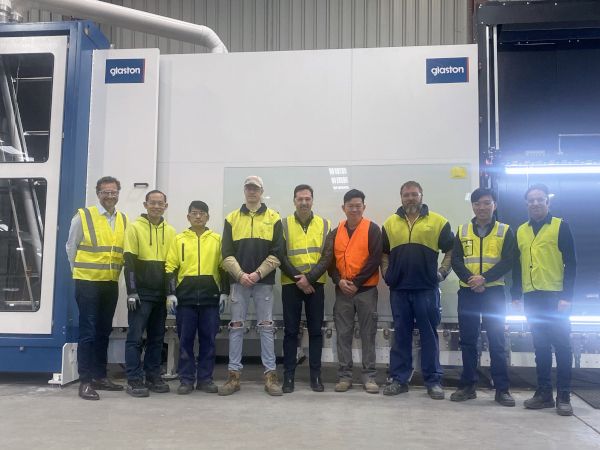
Date: 19 November 2024
In the photo - from left: Dean Haritos, CEO at Viridian; Sopheap Suong, Operator; Bora Tuon, Operator; Logan Mensforth, Viridian Team Leader; Paul Rainbird, Viridian General Manager; Alan Lim, Glaston; Christopher Hume, Viridian Production Team Leader; Jeffrey Mao, Viridian Operations Manager and Tarun Bhatia, Viridian National Operational Excellence Manager.
As building regulations require more energy-efficient glass, Viridian Glass has stepped up its game. Purchasing Glaston’s COMFORT BOX IG manufacturing line enables its Woodville plant in Adelaide to meet burgeoning demands with visibly better quality and shorter lead times. “High-quality insulated glass is the future in Australia,” says Tarun Bhatia, National Operational Excellence Manager at Viridian Glass.
Viridian Glass, the largest glass processor in Australia, has 7 processing plants across the eastern seaboard with an equivalent number of regionally located sales center branches. All of Viridian’s processing sites have the capability to produce high-performance, Low-E insulated glass units (IGUs).
LONG HISTORY WITH GLASTON
Viridian and Glaston have been working together for many years, although mostly with tempering lines. Today, Viridian Australia has 8 Glaston tempering lines at its different sites.
The company also has one original Bystronic, currently part of Glaston, TPS® line, the first IG line in the world. “We still have it, and it’s running well at our Clayton facility,” adds Tarun.
Viridian’s newest IGU line is from Glaston and located at its Woodville plant in Adelaide, South Australia. Until recently, the Woodville site was purely producing single-pane glass.
“Since producing IG was new for the Woodville site, we decided to move an old IG line from our New Zealand business there in 2022. It was a good Glaston IG line – nearly 20 years old.
Our Woodville team gained invaluable experience running the Glaston line and learning how to manufacture insulated glass,” Tarun says.
MOVING PAST LIMITATIONS
With time and changes in requirements, however, the Woodville IG line was not capable of processing Low-E glass or performing the argon gas filling.
“These were the two big limitations moving forward,” Tarun says. “So, we decided to purchase something that would be capable of running Low-E and filling the gas to meet the flourishing demand.”
The decision to purchase the new line was made at the end of December 2023, and the line was delivered in July 2024. Tarun says the Glaston technicians were very knowledgeable during the installation.
And for the Viridian team on the factory floor, running the new line is much easier.
NEW IGU LINE HELPS ADELAIDE SHINE
“Quality-wise, everyone is very happy with the IG units being produced on the new line. There’s excellent feedback coming from our customers,” Tarun says. “The quality of the seal is great. Sometimes, the primary and secondary seals can leak onto the glass. It’s messy. But the quality from this line is outstanding.”
STAR IN AUSTRALIA
Over the next five years, Viridian has plans to replace older equipment with new machinery to better match market requirements. “IGUs are the future,” he says. “The market is also trending toward adopting TPS® technology.”
“Australia now requires a 7-star energy rating for all new houses and buildings. That’s where double glazing comes into effect – especially double glazing with highperformance, Low-E energy-efficient glass. This is what our Woodville site was missing before. Now, they too can produce their own high-quality glass while reducing lead times to customers,” Tarun adds.
“Today, our Woodville plant is producing the highest quality IG units in Australia,” he says. “They’re happy being the star!”

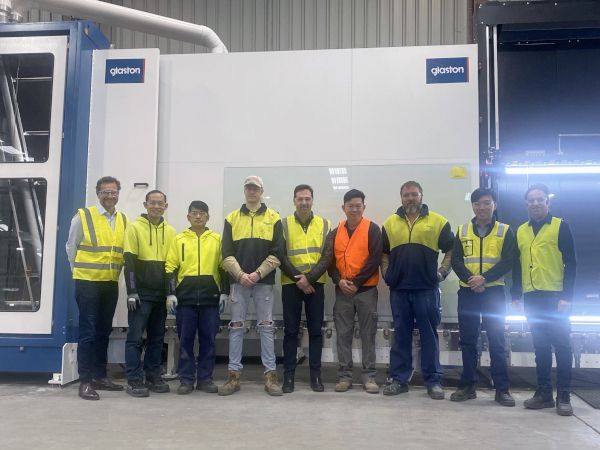

Add new comment