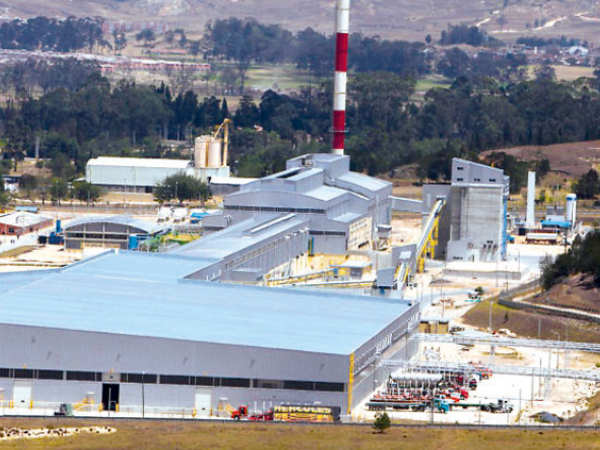
Date: 17 March 2016
The Hy.REC system is designed to recover the used hydrogen-nitrogen gas mixture so it can be reused in the glass production process.
Saint-Gobain is continuously seeking for innovative technologies to optimise the glass production process and improve the glass quality. One of these technologies is the Hy.REC® system, developed by HyGear. Saint-Gobain is testing the system in Herzogenrath on performance and reliability.
“It is great to work with such a leading company as Saint-Gobain”, says Mr. Niels Lanser, sales director at HyGear. “Saint-Gobain has provided us with valuable input during the design phase of the Hy.REC®. Their feedback on the system performance is also of great relevance for the further improvement of the system”.
Advantages of gas recycling
The Hy.REC® system is developed to recover the gas mixtures from the tin bath in float glass production and metal industry. Currently, significant amounts of the hydrogen-nitrogen gas mixture are – in combination with pollutants – left at the exit of industrial processes and left unutilised. The Hy.REC® system can recover this used and polluted mixed gas atmosphere from the process in a very cost-effective way. By feeding the polluted gas mixture into HyGear’s Gas Recovery System, a significant fraction of the hydrogen and nitrogen can be recovered and reused as a new reductive gas mixture. This reduces costs and improves the product quality due to the increased atmosphere refreshment rate.
Other gas recovery systems
HyGear is not the first company that offers a gas recovery system. The reason for the limited market penetration of the formerly launched systems is the low internal rate of return, caused by the high capital investment and high-energy consumption. Since the economical viability of industrial gas recycling systems depends on the value of the recovered gas in relation to the energy consumption of the system, the Hy.REC®mix is designed to consume the lowest possible electricity, which results in the highest economical rate of return. Key part of the integrated post-treatment module is the advanced Temperature Swing Adsorption (TSA) with ultralow pressure drop to further reduce operational expenses.
Working principle
In the first section of the Hy.REC, dust and contaminants are removed from the gaseous mixture. In the second stage, sulphur and oxygen are removed from the main stream. The third gas recovery stage is the post-treatment module. Key part of the post-treatment is the Temperature Swing Adsorption (TSA) to dry the hydrogen-nitrogen stream. Optionally, the customer’s waste heat can be used for the regeneration phase to increase the energy efficiency even further.
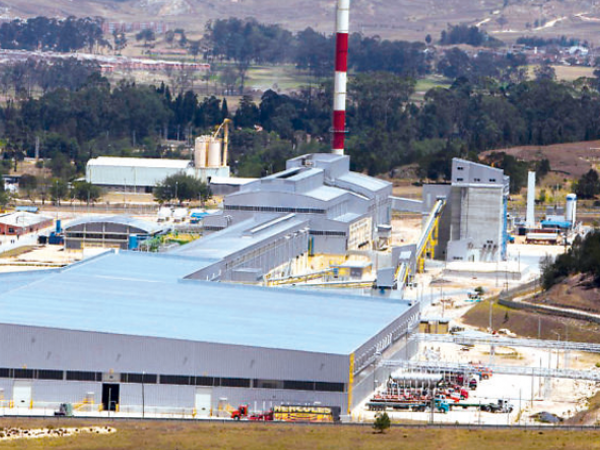

Add new comment