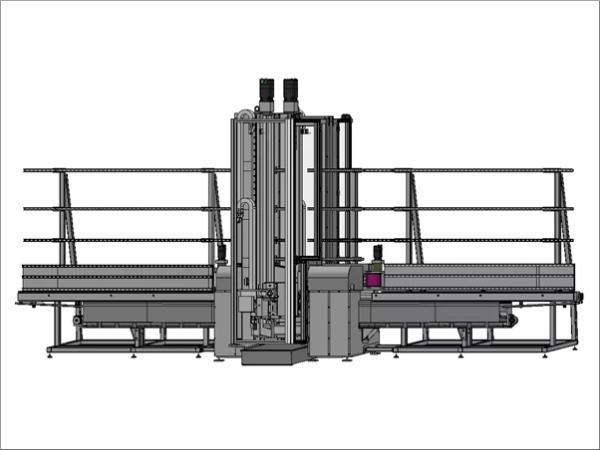
Date: 13 June 2024
Even more modern and lighter than its previous version, the new TFV 1600 is a vertical milling drill designed to perform drilling up to diameters of 85 mm and milling shapes on glass of thickness from 3 to 19 mm. The machine is made up of 3 independent sections: an input conveyor, a central body with a cabin where the processing takes place and an output conveyor.
Solid materials for maximum durability
The choice of materials and components is aimed at maximizing corrosion resistance and minimizing the entry of dirt into critical areas of the machine.
Modularity and optionals
By using a single head and by mounting a specific tool, it is possible to perform "milling" to create shapes (e.g. notches for assembling locks and hinges). With the application of the automatic tool change device (Optional), it is possible to combine drilling and milling in a single cycle, creating a finished door in a single pass.
Precision
Drilling and milling are carried out with ultra-precise electro spindles, ISO 30 tool holders, pressurized so that external agents such as air, dust, etc. do not enter the spindle and do not compromise its operation.
The spindle, which allows a rotation speed of 12,000 RPM, is air-cooled when in operation.
Inlet and outlet precision and stability
The glass is conveyed in and out via conveyors equipped with belts that slide on supports that allow the loading of large sheets with transport speeds of up to 12 m/min. The movement of the glass inside the central body takes place using toothed belts, equipped with an external covering that allows maximum friction in order to keep the glass firmly in place while the internal lining in contact with the guide is made of a special low-friction material allows better sliding of the belts on the guide, avoiding tears and making position control precise.
The guides are also made of special material, helping to maximize the performance of the belts.
The advantages of the new version
The updated version of the TFV 1600 chooses a new tool change position, which brings the following advantages:
- time-saving in tool change (faster for a consequent reduction in downtime),
- does not interfere with the machining
- facilitates maintenance operations,
- better vision of operations,
- 10+10 tools (8+8 in the previous version)
- better processing quality thanks to the increase in the rigidity of the spindles
Evolution towards convenience and precision
The new version is immediately characterized by its economic convenience, whilst enhancing the performance already provided by the previous version and increasing advantages such as reliability and precision in the processing.
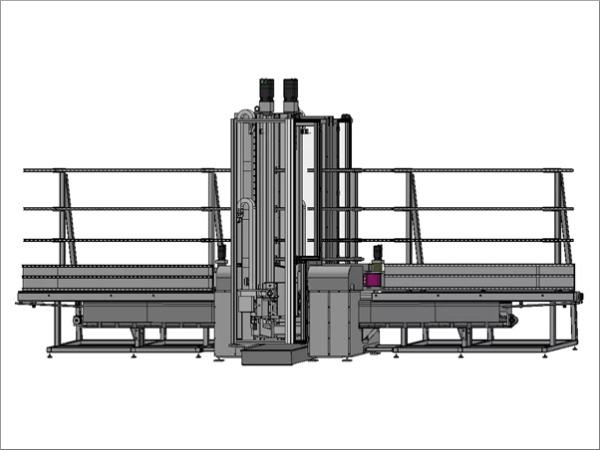

Add new comment