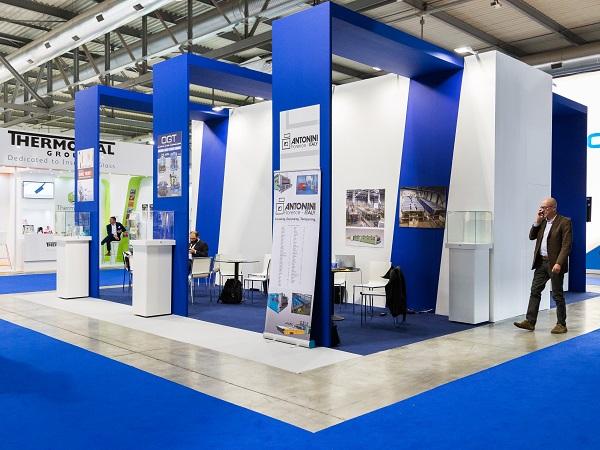
Date: 2 October 2017
One feature of the show is the return of Italian Hollow Glass.
The 2017 edition of Vitrum promises a major comeback. Italy’s Hollow Glass sector will be on hand, emphasizing the importance of this major global industry trade show. The hollow glass sector will be located in Pavilion 7.
Antonini Srl, Colorobbia Consulting Srl, Glass Service Srl, Ocmi OTG Spa and Olivotto Glass Technologies Spa are the companies that will represent Italian-made products for Hollow Glass at Vitrum (Stand D25). In addition, the Hollow Glass division of Bottero Spa will showcase a selection of its machinery for both flat and hollow glass, as well as products and systems for float, laminated and packaging lines at Stand E21-G30, also in Pavilion 7.
“Technological know-how and high qualitative standards are the true distinguishing factors of Italian brands across international markets. Bottles, tableware, pharmaceuticals, cosmetics -- Italian-made hollow glass ensures complete solutions, customizations capable of satisfying all the needs of their customers and the ability - almost unique in the industry - to join forces and form a united front. We plan to leverage these strengths this year at Vitrum 2017. In the group exhibit area, we are ready to meet clients and buyers from around the world, in order to nurture, plan and launch new relationships and projects”, remarks Michele Gusti, president of GIMAV’s Hollow Glass Group, and president of Ocmi OTG Spa.
The latest findings from the GIMAV Study Center provide further evidence of the sector’s value: more than 85% of Italy’s hollow glass revenue comes from exports, with a +1.05% increase over the previous year (when sales were up by nearly 3.5%).
According to the most recent data, exports of Italian machinery and technology for Hollow Glass processing continue their upward growth trend (begun in 2015) with the EU as the top destination (France out in front) and the strong recovery of the American markets (North America at +41%; Central and South America at +75.7%). Asia, too, left its mark, compared to the previous 12 months, with a 25.61% share of total global exports.
Summing up the key indicators for the Italian Hollow Glass sector:
- Mexico is the number-one importer of Italian technologies and machinery for Hollow Glass processing with an 11.75% share
- followed closely by China, accounting for a healthy 10%
- in the United States, the import share of Italian machinery doubled
- Russia, after the major crisis of 2015, is on a rising curve, climbing from 15th to 9th position.
EXHIBITORS IN THE ITALIAN HOLLOW GLASS AREA - Pavilion 7, stand D25
Presentation and interviews
ANTONINI SRL
Founded in 1946, Antonini is a well-established presence on all five continents, with more than 1,700 installations in 82 countries around the world. Its production is focused on annealing and decorating furnaces, glass block tempering furnaces and HV insulator furnaces (that make Antonini a leader in the Chinese market), cold-end treatments and dosing pumps for cold-end treatment.
Moreover, the company is an outstanding plant overhauls and upgrades provider. Mexico and all of South America are target countries for the company, but major work orders also arrive from Southeast Asia, Thailand, the Philippines and Vietnam, to name the top few. The European market also continues to strengthen its position; in France, Antonini systems are in high demand, while Italy is experiencing a promising turnaround.
In the words of Barbara Antonini, Sales Manager for Antonini Srl: “We also have high hopes for positive outcomes from this year’s Vitrum show. I firmly believe that the International Glass Show in Milan has everything it takes to become a competitive trade show for Hollow Glass as well. We have worked together and will continue to work to ensure this happens because, if we can manage to attract more foreign visitors for Hollow Glass, it would be a win-win result for everyone: for us, for Vitrum, for our Association and for our country. The excellence of our industry is well-known around the world and Milan is a very attractive city. Everyone loves it -- exhibitors and visitors. International by nature, it has near-perfect logistics and organizational possibilities”.
GLASS ENGINEERING - COLOROBBIA CONSULTING SRL
Design and engineering of turnkey industrial plants for the production of glass and vitreous enamel. This is the core business of Colorobbia Consulting - Glass Engineering & Contracting Division. Glass Engineering was established in 1987 and today, armed with its robust synergies and integration with all the other divisions of the Colorobbia Group, is able to provide a full spectrum of services and solutions to the marketplace and to the Group itself.
According to Alessandro Bandini, CTO of the Colorobbia Consulting Glass Engineering Division: “Vitrum has, once again, brought together Italy’s leaders in Hollow Glass. This is likely thanks to new, lasting synergies among industry leaders, through a renewed spirit of cooperation among the Italian and international associations involved in the promotion and dissemination of information about the world of glass. Nowadays, there is an increasing awareness and consideration of ‘green industry’, and we are focusing our efforts in this direction.
We intend to concentrate on electric fusion or, in any case, a fusion process aimed at reducing harmful emissions as much as possible. Our strengths are, and remain, the same as those that set Italian products apart around the world: the quality of our products, the reliability of our machinery, our attention to after-sales customer service, and, above all -- the extra plus that we are most known for -- our adaptability and desire to create anything new that other global manufacturers have not yet produced. Made in Italy also means “Italian industry in motion”, evolving, moving toward ‘green and smart’ targets.
For Vitrum 2017, we plan to bolster our well-established commitments in the East, pleading the case of reduced emissions, without neglecting the developing markets in Africa and South America. This year, in Milan, we decided to ‘show up’ because we believe in the validity of, and the possibilities offered by, this Italian event. It is our hope that the Vitrum management gets hard at work now and, even more, in the near future to funnel the greatest number of trade professionals toward Hollow Glass, so that at future editions there is an even greater outpouring of industry interest in participating in this event”.
GLASS SERVICE SRL
Glass fusion technologies and the Robotic Division: these are the company’s two macro-departments that provide “turnkey” plant installations around the world, directly with their own staff, and through supervision of staff provided by the customer, as well as the start-up of auxiliary furnaces and systems.
All the plants designed and produced by Glass Service meet the growing demands of international markets in terms of energy efficiency, production flexibility, ease of use and the highest quality standards of the final product. The company also ensures complete after-sales service for every product, around the world, including repairs under operating conditions and replacement of electrode holders.
Giulio Isernia, Sales Director for Glass Service comments: “We believe in Vitrum because we feel this event can quickly become a real drawing card for specific areas of interest. With the proliferation of trade shows in our industry, Vitrum’s advantage could be, and certainly will be, the possibility of firmly establishing itself as a magnet for all those companies for which ‘Team Italia’ is able to offer solutions, both specific (furnaces, machinery, etc.) and global (turnkey plants).
This year, at the show, we are exhibiting our most recent developments in the area of advanced combustion systems for forehearths and working end, system parts dedicated to furnaces, as well as our developments in terms of turnkey projects. Our recipe for success? Having gained a foothold and strengthened, day after day, a constant presence in all markets, thanks to a combination of products, technological innovation and field presence. All of this was, and is, possible thanks to our staff that really does work 24 hours a day. Skilled professionals able to measure up against the fiercest international competition.
Indeed, each of us has developed products of absolute excellence and the constant communication among our groups is finally allowing us to orchestrate much more efficient teamwork than in the past. Our expectations for this year, compared to the past, are high; that is because the tireless and extremely efficient assistance efforts of the organizational team have allowed us to focus our attention on specific customers”.
OCMI-OTG SPA
Leading global supplier of complete production lines for borosilicate glass vials, ampoules, droppers and cartridges, Ocmi OTG fully meets the needs of the increasing number of operators looking to automate quality control processes, production line loading and final product packing operations. But OCMI is also a supplier to the leading global manufacturers of crystal and soda-lime stemware.
Our crown jewel is the SA model. Available in 42, 48 and 60 station versions, it ensures the highest degree of flexibility in response to the most diverse production requirements. Although European demand for products differs from that of markets in the United States or the Far East, in terms of glass type and design, OCMI has proven to be a reliable long-term partner, one that truly listens and complies with even the smallest changes final users may request to optimize productivity and efficiency.
A peak performer in the design and production of machinery for processing pharmaceutical hollow glass and tableware, thanks to its partnership with MT Forni of Venezia (which specializes in glass melting furnaces, annealing and decorating lehrs), OCMI can also supply the technology and know-how required to produce technical glass articles such as glass blocks and HV insulators.
According to Alex Crescentini, Sales Manager for Ocmi OTG: “At Vitrum, we will showcase our SA stemware sealing and stem stretching machines, PAS blow-presses for jugs, custom-designed hydraulic or pneumatic presses, and the possibility of supplying turnkey production lines for glass block and high-voltage insulators. We expect these solutions will be of interest to those Vitrum visitors who typically arrive from Eastern Europe, the Middle East and Mediterranean Africa.
However, thanks to extensive pre-event promotional efforts, we also expect to see many pharmaceutical glass manufacturers at the GIMAV group stand dedicated to Hollow Glass where they can find detailed information not only on the borosilicate glass tube forming machinery offered exclusively by OCMI, but also on the equipment used to produce the glass tubes themselves”.
OLIVOTTO GLASS TECHNOLOGIES SPA
Olivotto Glass Technologies has worked in the hollow glass industry since 1946, when it began marketing its first rotating hollow glass blowing machine. Research, innovation and ongoing technological development have enabled the company to become a leading brand worldwide, supplying turnkey systems and services designed to meet any and all production needs.
In August 2003, Olivotto acquired the glass division of Antas (Italy), a company with time-tested experience in hollow glass. In June 2007, the company then acquired Lynch Systems (USA), one of the longest-established hollow glass forming machinery manufacturers in the world.
In April 2008, it acquired W. Lindner Maschinen (Germany), known for its production of high-quality machines for all types of glass (lead crystal, soda lime, borosilicate). All leaders in their respective market sectors, the four companies have joined forces and combined their capabilities to become the benchmark in hollow glass, as manufacturers of plants, systems and machines.
The Group guarantees perfect integration of all its machines, along with complete assistance and service at all phases, from design to start-up of the production process.
Olivotto GT offers technological solutions designed and developed in such a way as to create synergistic effects with the customer’s production strategies and to quickly adapt to all customization needs. They are all turnkey machines, complete lines and systems for the production of: stemware (all processes); tableware; ovenware; carafes; large containers; lamps and lighting elements; automotive headlights; insulators; glass tubes; laboratory glass; glass insulators; mineral wool; and automatic packaging of stemware and drinking glasses.
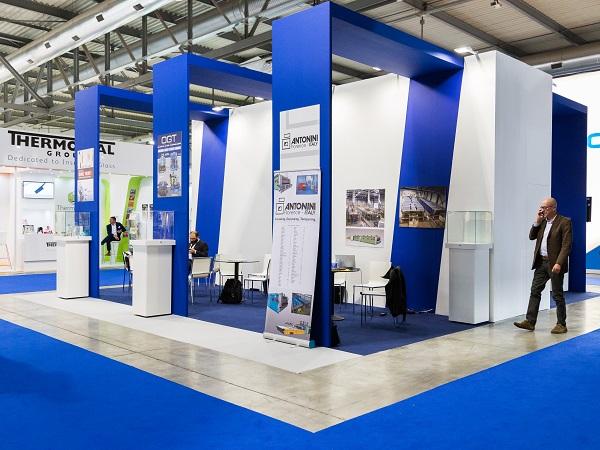

Add new comment