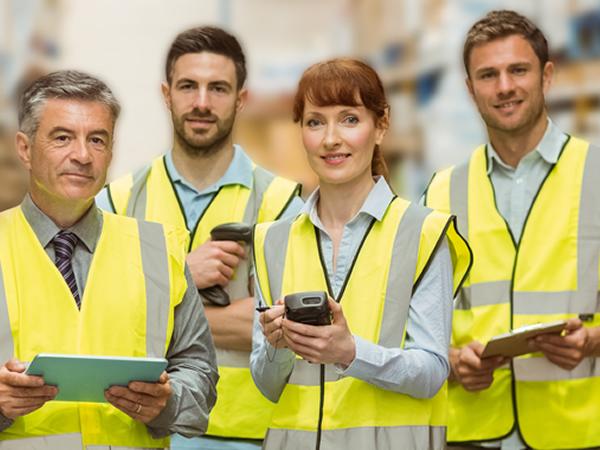
Date: 8 March 2021
While optimisation almost always refers to machines and their availability, digital support for staff holds the promise of additional potential, too.
Depending on the organisation, processes include the transport of glass and racks, searching for panes, provision of work materials, picking of orders, and maintenance of machines and systems and generally speaking, other activities on the side that have a negative effect on productivity. With the Shop-Floor Assistant, HEGLA New Technology now offers an app that maps individual or pooled processes, structures them, and provides assistance for the tasks.
“When we visit our customers, we observe that irrespective of how varied the types of production are, the themes around work organisation are very similar,” explains Dr Markus Schoisswohl, Managing Director of HEGLA New Technology in Paderborn, Germany. “That provided extra motivation for the creation of a diverse, adaptable solution that could be used to support staff no matter what software and machines they work with.”
To handle the different tasks of a glass-processing operation, the app was subdivided into groups of functions. Based on the shop-floor transport, pane identification, material provision, and machines and maintenance sections, customers can integrate a variety of processes into the app as required.
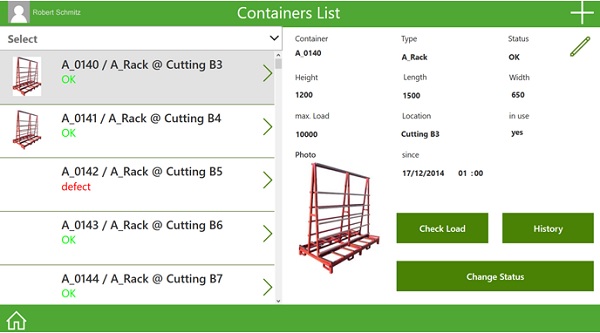
Shop-floor transport, pane identification, and rack requests
They are a time-consuming irritation: improperly stored glass racks, panes that are not provided in time for further processing or have to be found. Missing information or labels that fall off racks regularly lead to delays as well. For operations that want to organise internal glass transport centrally, Shop-Floor Assistant provides an opportunity to give the related processes a digital structure.
Upon scanning a QR code permanently installed on the rack, for example, its intended parking location and when it is needed are displayed. If the app is used for notification of completion, it can also be used to generate the internal transport order. The relevant employee selects the transport, carries it out and acknowledges it at the new location via scan.
If a rack does end up unparked, another scan will provide information on the goods or order that it currently holds. Operators benefit from a precisely defined glass flow, there is no need to search for missing panes and the location of any rack is known at any point in time. Once these processes have been organised digitally, it becomes possible to extend them by means of automatic guided vehicle systems (AGVs).
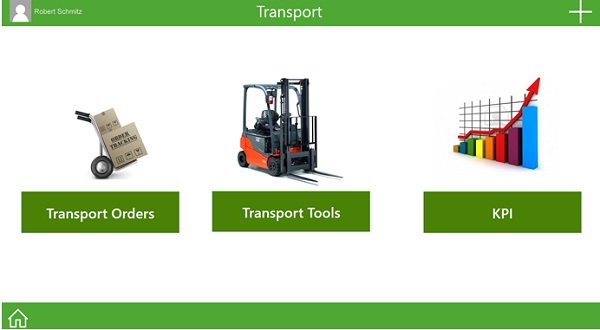
Mobile glass identification in production or at the customer’s location
When the daily work routine requires the identification of a single pane, the app has a function that can do so. By scanning the QR code on the paper label, laser marking, or via manual input, the data stored in the end device are displayed and used to uniquely identify the glass. To do so, the app accesses its own database in which the relevant information of the ERP system is stored.
If desired, the information can be made available via a cloud or relevant interface to the downstream further processing party such as a window manufacturer or glazier. One scan is enough to re-order an identical piece of glass, window or shower screen directly on the construction site. This function is also useful in production.
By scanning laser-marked glass or the order documents, notification of breakage can be sent to the shift foreman, Head of Production or work preparation from any location, and replacement production is initiated without a long coordination process.
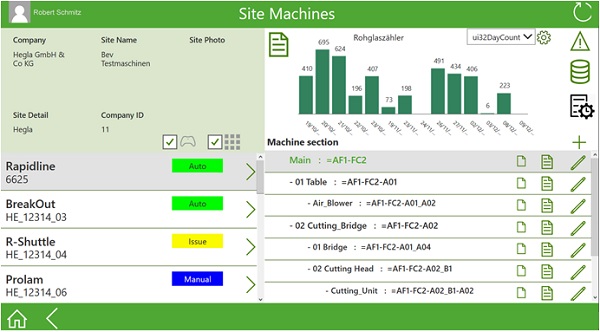
Picking: Finding instead of searching
The app’s picking function is designed to provide a fast and current overview of the orders that have already been completed. In many companies, pick lists are printed out and comments are added by hand, so they are only as current as the time of the last print-out. To simplify the process and support staff, an overview of orders that are ready for shipment can be displayed, selected, edited, and grouped by planned route in the app.
The function displays the current production status subject to the notifications of completion and at the same time, provides the option of adding extra comments to the pick list. For even greater transparency and managed processes, staff can also display who is currently working with which order. The added information and comments are saved directly in the document, which makes them available to the driver, Head of Production, and Sales, for example.
Material provision
Gloves, cutting wheels, or cutting oil – when urgently needed consumables are unavailable, this quickly leads to system standstill. For staff, in the worst case this means having to go to the warehouse to fetch what is missing. ‘Shopping’ is the name of the section of the app in which such things are collected and can be ordered internally, like in an online shop.
Either a warehouse employee delivers the order so that production can continue, or the required things are provided and can be picked up from a central depot the next day. To make things even easier, an internal warehouse management function is also integrated into Shop-Floor Assistant. As soon as stock falls below a minimum level, the warehouse is informed and can initiate a paperless material order or special coordination.
Machines and maintenance
Although personnel may work well on the machines and operate them based on years of specialist expertise, at some point they will require maintenance or a wearing part must be replaced. In this case, too, the app has a section whose functions centrally record the schedule of appointments and provide the required information.
Once the documentation has been stored in the Cloud, it is available at any time and does not have to be found and fetched when needed. Depending on how centralised maintenance should be, the app contains a ticket system for requesting help from internal operations technology transparently, by means of a standardised and traceable procedure.
“Heads of operations or production always have an overview of the upcoming work and are able to prioritise it as needed,” says Dr Markus Schoisswohl. “Depending on the degree of integration desired, they also have access to machine data independent of location and the current status of the workflow, as well as receive information as to whether they need to support or relieve the employee carrying out the work.”
HEGLA New Technology’s Shop-Floor Assistant was designed as an overarching application that can be integrated into existing systems and processes. “With this app, we aimed to close digitalisation gaps for which there has been no solution or whose solution was unfeasible within the framework of existing software systems and machines,” explains Bernhard Hötger, Managing Director of the HEGLA Group.
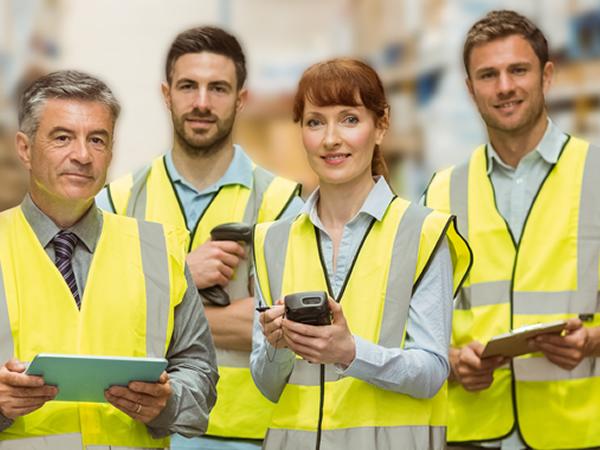

Add new comment