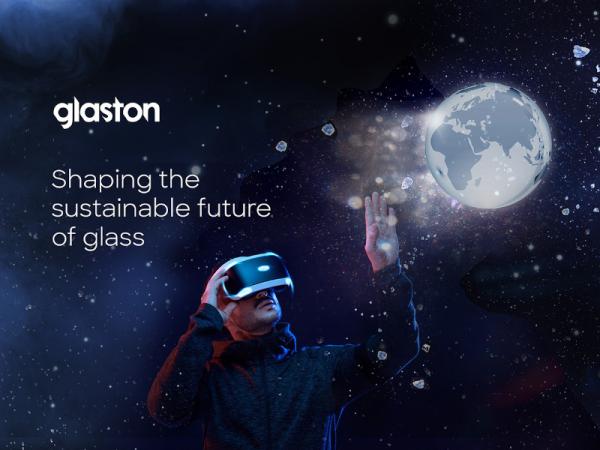
Date: 5 May 2023
Below are just some of our latest developments that will be showcased to the participants at this year’s China Glass.
In insulating glass manufacturing:
Glaston COMFORT’SEALER – New Sealing Robot
For those who do not wish to seal IG units manually, Glaston has a new solution. With the aid of the automatic sealing robot COMFORT’SEALER, one can upgrade the Glaston IG line COMFORT BOX from an entry-level solution for industrial IG production to an automated production line. The main advantage of the new COMFORT’SEALER is its high material dosing accuracy due to the convincing gear pump dosing technology. This volume-controlled dosing function precisely determines the sealing depth and width and then subsequently applies the exact volume of sealing material required. The high-quality dosing technology is developed in Germany and assembled in China.
TPS® – the most flexible way in IG manufacturing
TPS® is not just a machine. It is a system solution for highly efficient insulating glass manufacturing. Glaston is the inventor of this technology with more than 160 installations worldwide. Production is greatly simplified as the Thermo Plastic Spacer material can be applied directly onto the glass plate. This eliminates any need to stock different spacer profiles and connectors. The spacer width can be changed as desired during operation without any time loss. TPS® is the most flexible way of producing IG units, multilayer or solar panels.
In flat glass tempering
Glaston CHF Solar – Combine high capacity with high quality
When production quantities are vast, achieving the highest capacity is of utmost importance. Just as important is to secure the reliability and constant operation of the machine.
Glaston CHF Solar tempering line provides the best solution for large production series of all glass types. The real key factor in terms of spotless glass quality is the Vortex heating and convection system. It enables unlimited heating uniformity and accuracy with its equally unlimited profiling and heating control.
All aspects of the line underline the reliability and the long lifetime of the furnace. The modular design enables high reliability with the lowest downtime. High reliability has also been designed for the technical solution of the drive system. The servomotor-based drive system provides extremely accurate roller speed control and minimized glass gaps to maximize production. Practically zero maintenance is required.
Glaston TC Series – Cut production costs
Effective and accurate heating is key to high-yield, high-performance glass production. The Chinook circulated air convection system used in the TC Series furnaces reduces energy consumption close to the absolute minimum. Thanks to faster heat transfer, the cycle times of the TC Series furnace are shorter. This allows you to cut down on overall production costs, including manpower costs per square meter.
Chinook is the market’s most efficient heating system, based on the highest number of measurements, combined with automatic process adjustment. In practice, this minimizes operator input while maintaining constant high capacity.
Glaston’s 50 years of know-how in glass heat treatment technology has been used to create super-tempered, fire-resistant glasses without compromising on yield. The TC Series meets the increasingly more stringent global safety criteria for fire-resistant glass and all other demands when super-tempered glass is recommended or obligatory to use.
In automotive glass processing:
Glaston CHAMP EVO – An evolution in automotive glass pre-processing
Glaston CHAMP EVO represents the latest evolution in the CHAMP automotive glass pre-processing line. The newest CHAMP EVO generation includes high-precision features in a grinding machine. Maintenance costs and wear and tear have been reduced considerably with energy-saving, state-of-the-art linear drives that are accurately adjustable and a freely moveable glass holding system for short changeover times. The optimized cell also features lighter moving parts, such as the cutting bridge or grinding table and many other technological improvements.
Glaston MATRIX EVO: The best technology for tomorrow’s automotive glass
The new Glaston MATRIX EVO automatic bending furnace is now available to revolutionize the way automotive windshields and sunroofs are bent to perfection. The line is specifically designed to meet the most challenging requirements in today’s automotive industry. It offers the best optical quality for applications, such as advanced driver assistance systems (ADAS), head-up displays (HUD) and coated glasses when combined with the most complex shapes.
Meet Glaston at China Glass 2023, Hall E1, Booth #419!
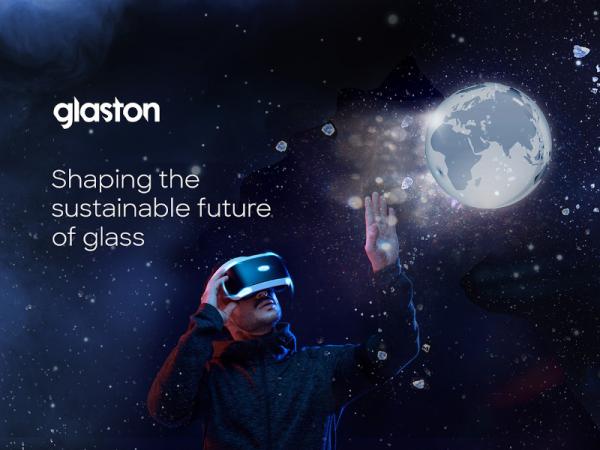

Add new comment