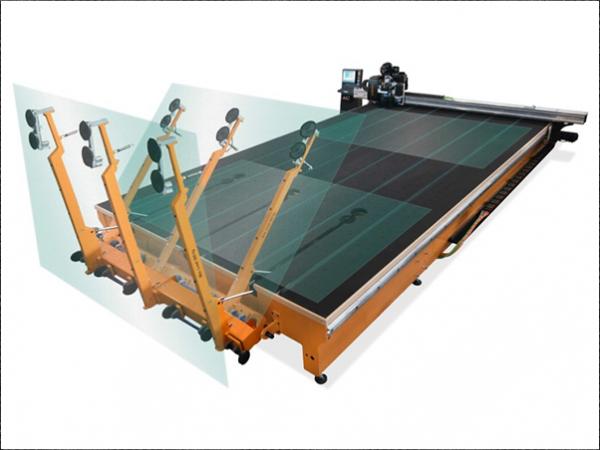
Date: 5 August 2020
In the 80’s decade, TUROMAS engineers detected that the loading phase slowed down the rest of the flat glass processing. To cope with that bottleneck, they developed a system composed of tilting arms with suction cups to load the sheet of glass and unload it on the cutting table.
Since the launch of this pioneering, reliable and secure solution to date, more than 1,200 units have been manufactured and sold worldwide, with a significant expansion in Spanish, Brazilian and Portuguese markets.
This technology has been in use for more than three decades under any condition, however, it has not remained inactive and has evolved into new models as the ones which incorporate belts to position and evacuate glass sheets in a completely automatic way.
Currently, the TUROMAS R&D department is developing a new version to work with jumbo-sized glass and a new immediate separation system. Advances that without a doubt, will revolutionise the glass industry.
Benefits of TUROMAS loading system
The TUROMAS loading system has multiple benefits for the customer who decides to purchase it. Benefits regarding increased productivity, plant distribution optimisation, economic savings and factory safety.
1. Automation of glass loading and cutting for improved efficiency and productivity
To automate the glass loading and cutting process, TUROMAS offers different solutions depending on the customer’s investment, or to the complexity of the plant installation.
The most standard solutions would be to combine a RUBI 303VA table for cutting monolithic glass with a break out table or to add an MV-300 loading table to a compact laminated glass table. Both are equipped with tilting arms with suction cups that allow the glass sheets to be loaded regardless of the thickness and type of glass.
The arms with suction cups that perform the loading function are incorporated into the structure of the same table, thus eliminating the need for an external loader or a transfer table.
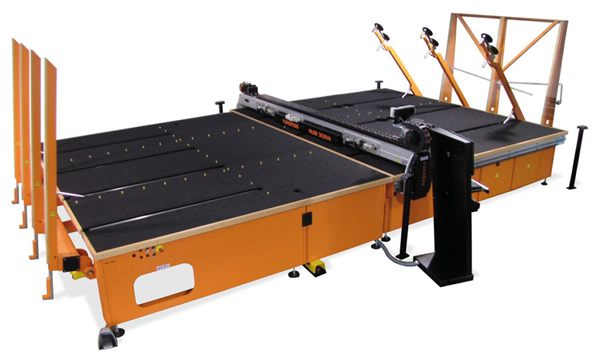
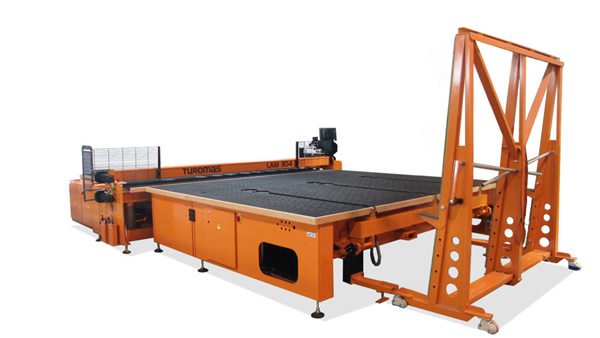
Together with the suction cups, the arm structure is equipped with stops that allow to manually feed the cutting table as if it was a conventional loading arm. In this way, the loading system can be adapted for customers with highly variable production and demanding a flexible loading system in accordance with their needs.
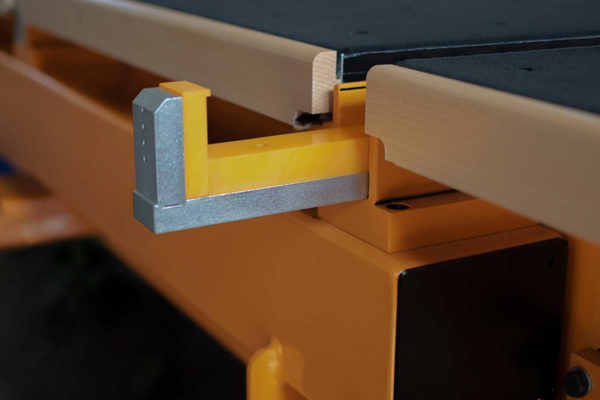
For companies with a significant range of glass, the alternative would be to combine a basic intelligent warehouse with a cutting table incorporating the TUROMAS loading system. The combination of both machines allows to optimize the space and allocate the non-used area of the loader to expand the storage capacity of the system.
This is the case of the VAC cutting models with TUROMAS loading system and positioning belts. An extremely compact and high performance automatic glass loading and cutting solution.
In particular, the RUBI 403VAC-6 model allows having 2 sheets of glass on the table at the same time, with synchronized movement, allowing the second sheet to enter the cutting area during the evacuation of the first sheet to the breaking system. In addition, the RUBI 403VAC-6 model offers the possibility of extending the useful cut to 6100 x 3300 mm.
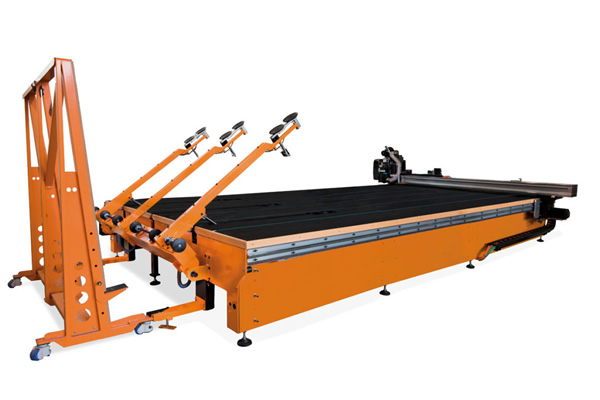
Finally, a fully automated solution would be integrating an automatic warehouse – Rack-Shuttle SR and an automated cutting line. A simple and economical alternative that allows automatic storage, loading and cutting glass with a 300% increase performance.
Each plant is different and all of them have elements that hinder or block the installation of the machines or their operation, limiting the effective working area to the space between columns of the same hall and always subordinated to the availability of a bridge crane over the entire storage area for glass reloading.
The SR system was born to break with limitations, since it can work between different halls by skipping columns and eliminates the need for a bridge crane covering the entire storage area. Glass is reloaded in the storage area on a specific rack that will be moved within the warehouse by the machine itself.
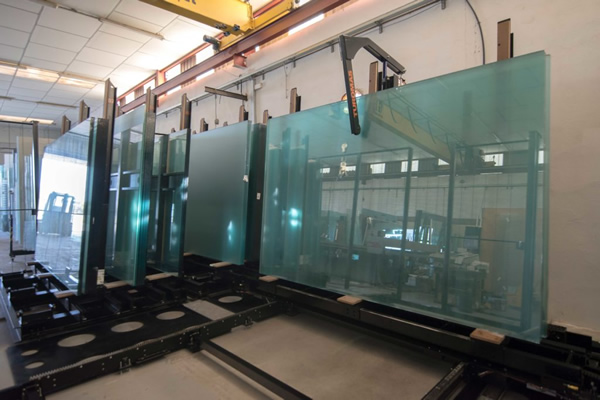
In addition, these storage systems have been designed modularly so that the machine can keep growing as the company’s needs do, increasing the number of racks and the storage area gradually.
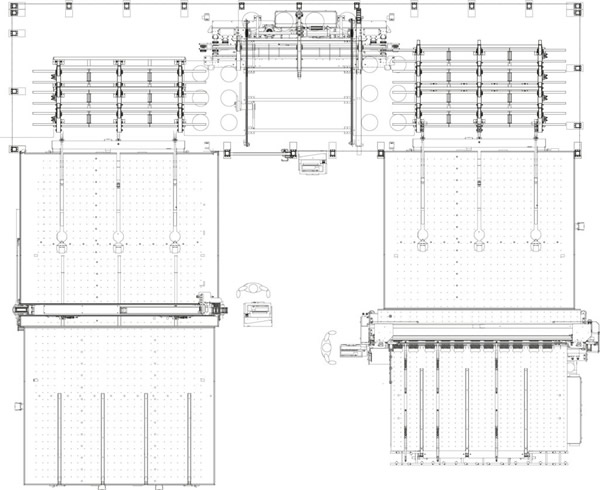
The cutting tables, thanks to the TUROMAS loading system, are able to load the glass sheets directly from the warehouse rack. In addition, the Rack-Shuttle SR allows simultaneous fed to two lines arranged in parallel, increasing the workflow and glass supply to the following processes.
Greater flexibility, on the one hand, and a higher production rate, on the other, the Rack-Shuttle – SR warehouses, in combination with automatic loading machines with tilting arms and suction cups, form a production system capable of meeting the needs of the most demanding processor and, at the same time, adapting to virtually any space and type of glass.
2. Save space and money without sacrificing absolute performance
Compared to other conventional systems, that do not integrate automatic glass loading, the TUROMAS loading system saves customers between €10,000 and €12,000 per year as there is no need for an operator to feed the cutting table and the same can be assigned to other tasks.
Additionally, the bridge crane can be used instead of being used to feed the cutting table can be reserved for other industrial processes such as loading / unloading of raw material and finished product.
Another major benefit of this technology that integrates the loader into the cutting table itself is the optimisation of the space and consequently the cost savings of the automatic loader. There are companies that do not have enough infrastructure and it is essential for them to make the most of the available space.
3. Safety, an important aspect that is not neglected
The TUROMAS loading system increases well-being at work by increasing employee safety by preventing accidents that could occur when feeding the cutting table manually.
Prevention of labour risks and also a considerable reduction in breakages due to collisions since the suction cups on the arms detect when the surface of the glass is close and only then activate the vacuum to prevent possible impacts.
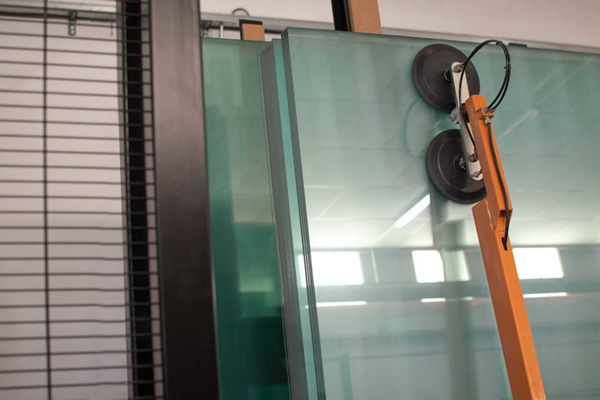
To control the grip of the suction cups, a vacuum pressure switch indicates when the optimum vacuum level for each glass size is reached. In addition, the design of these suction cups is designed to only pull one sheet of glass from the package in each cycle.
All this data is monitored and displayed on the control desk of the table and the office monitor.
4. Loads all types of glass
Glass is a material which has a wide variety of typologies and applications depending on its composition. Therefore, the TUROMAS loading system has been specifically designed to work under any circumstances.
This system allows the automatic loading of standard sheets of monolithic glass with thicknesses from 2 mm. to 25 mm. as well as sheets of laminated glass up to 12+12 mm.
In particular, laminated glass is heavy and therefore difficult to move. In order to facilitate its handling, the Spanish manufacturer offers to the glass processor the most compact solution for loading and cutting laminated glass currently available on the market: an MV-300 loading table plus a LAM 304 cutting table.
In addition, the loading system has been designed to avoid contact with the top layer of the glass at all times, transporting and loading the glass without touching it and therefore without affecting the quality of the low-emisive layer.
Every warehouse is unique and every customer has different requirements, therefore, TUROMAS handling equipment is versatile and tailor made. State of the art technology solutions that suit not only the entrepreneur who is taking the first steps towards automation but also the one who needs maximum automation and productivity.
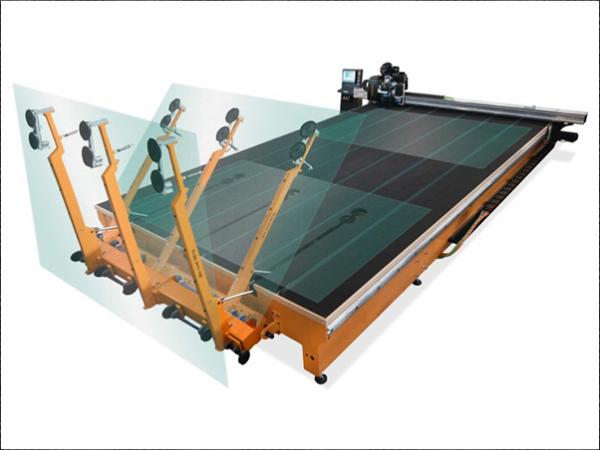

Add new comment